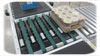
This right-angle transfer unit from Dematic diverts cases to order assembly and then shipping. Belts pull the cases onto the diverter; rollers rise up and send them on to the next conveyor.

The screening section of the Triple/S Dynamics Tex Flex vibratory Conveyor was designed to remove loose pieces that may enter the product stream from unsealed pouches. Source: Triple/S Dynamics.
If the circulatory system breaks down, everything breaks down. Robust design, washdown capability, affordability, accumulation, flexibility, quick changeover times and automation are the mainstays food producers look for in conveyor solutions.
Today, orders are becoming more complex. Larger retailers take dedicated pallets because they deal in large volumes and have the space to store products before putting them on shelf. Smaller operators, however, ask their suppliers for mixed pallets of disparate products because storage space is limited, and volumes aren’t as high.
Every production environment is unique and defined by a number of factors-product type, package type, processing speed, filling speed, space constraints, budget, automation requirements, accumulation needs and more. To get the right solution at the lowest cost, it’s best to consult an expert.

The Allpax conveyors shown here use specially designed stainless retort baskets. Conveyor systems are modular and use common frames, shaft sizes, bearings and other components, no matter the size or configuration of the line. This reduces spare parts and maintenance for processors. Source: Allpax.
Accumulation, buffering are key factors
According to Jim Streblow, vice president of sales and marketing at Wisconsin-based Nercon, a vital capability of every conveyor system is accumulation. “More and more producers are focusing on that aspect,” he says, and for good reasons. Manufacturing machines in a production line are bound to have problems from time to time. Be it the unscramber, the filler, the labeler or case packer, a line can be kept alive with accumulation and buffering zones that allow production to continue while short stoppages occur.“Is accumulation the heart of the production line’s circulatory system? In a way, it is. Accumulation and buffering can provide the breathing needed to feed machines when unexpected problems occur, and protect efficiency and profitability,” notes Streblow.
Short delays can happen any time on just about any type of equipment. Priming the labelers, cartoners or case packers are planned delays, but unplanned delays can happen too, such as an incorrectly oriented package jamming in a wrapper. And these short delays can add up. For example, six 10-minute stops in an eight-hour shift translate to one hour of lost production. If machines shut down at different times, which they almost always do, productivity losses can peak to 40 percent or more at times during the day.
“Add potential spoilage of product to lost production time, and the effect can be huge,” says Streblow. “A plant design with effective accumulation will help protect the bottom line.” Choosing the right type of accumulation and buffering solution for each product and application can be a critical factor in long-term performance and competitiveness.
Accumulation occurs on conveyors in the spaces between the packages. Controls are added to conveyor systems to allow for accumulation as well as buffering-the breathing-of product transport on the line.
Accumulation can be designed into a single lane, as well as into multi-product wide lanes depending on application specifics such as the product, line speeds and machine capacities.
Belt speed determines buffering capacity. For instance, if the product is 12-in. long, and the rate of output from the filling machine is 60 products per minute, a 60-ft. long conveyor operating at a speed of 60 ft. per minute (fpm) will be continually full, offering no buffering capacity. If the belt speed is increased to 120 fpm, the line can accumulate 30 products at any given time during a downstream interruption.
Utilizing conveyors for an accumulation solution typically costs less than a machine solution because transport conveyors are needed between equipment anyway. Simply adding controls and perhaps additional conveyor length may meet the accumulation and buffering needs of some production lines. However, when the amount of accumulation is greater than the spaces between the products, investing in a storage device or accumulating machine is necessary.
Accumulation machines
In addition to accumulating conveyors, there are a number of other accumulation machines on the market that provide greater capacity and more sophisticated product handling. Accumulation equipment can be first-in-first-out (FIFO), or first-in-last-out (FILO). First-in-first-out is useful where more sensitive products need to be coded and tracked on a case-by-case basis before final shipment. First-in-last-out is used where close tracking is not required. Many types of accumulation equipment deliver products randomly or somewhere in between FIFO and FILO, such as:• Alpine system: Alpine machines elevate or lower products on a single product-wide vertical serpentine conveyor and, with controls, can provide both accumulation (between product spaces) and buffering capabilities.
• Drum spiral conveyor: The drum spiral conveyor utilizes a wide chain that has the ability to accommodate rows of product for accumulation. It can also be controlled to respond to fluxes in downstream production.
• Vertical accumulator: Products are backed up in rows and then are “parked” on a flight and indexed up until the accumulator is full. The vertical accumulator uses a small footprint compared to the volume benefits.
• Recirculating accumulation table: Two wide belts traveling in opposite directions cause a recirculating motion of products on this accumulation table. Products flow randomly out of the discharge area.
• Bidirectional accumulation table: When the main conveyor senses a back-up, the wide belt on the bidirectional table located adjacent to it begins to move perpendicularly to the main conveyor, and accumulates products. When the back-up is cleared, the belt reverses direction and discharges products back into production.
• Variable length accumulators: Offering true buffering capabilities, variable length accumulators are designed with an expandable and contracting product path that is controlled to respond to minute surges in production.
• Serpentine accumulators: Built on a vertical accumulation concept, these accumulators offer variable length accumulation in three dimensions. The product travels on rows and makes use of vertical space.
But simply adding accumulation machines and buffering conveyors into a production line isn’t enough to fix inefficiencies. The machine layout and conveyor configurations need enough space to allow for each machine’s threshold. Conveyors must also be properly specified to feed and discharge accumulating equipment. And buffer zones must be completely cleared; downstream equipment should always run faster than upstream equipment. This not only creates the required buffering capacity, but also enables accumulated packages to be purged as required.
Kevin Mauger, president of NCC Automated Systems (NCCAS) in Souderton, PA, says introducing redundancy is an effective alternative or complement to buffering. “This involves adding extra conveyor and packaging lanes that can take product if the main line goes down,” he says. “It’s generally a more expensive route, but the payback is in production efficiency.”
NCCAS is an integrator that uses packaging equipment from all the major suppliers. “Our approach is to pre-engineer a line. We assemble all equipment, wiring and automation inside our production facility; test the customer’s product in a series of trial runs; and then deliver the complete package for reassembly in the customer’s plant. This process minimizes installation and start-up times-from a month or more to a week or less,” Mauger says.
Modularity and flexibility
Dematic of Grand Rapids, MI has been in the conveyor business for 72 years. Dematic engineers and builds modular conveyors that can be mixed and matched according to processor requirements, and then assembles them on-site. Once complete, the modular concept allows optimum flexibility. “In the past, it was typical for a company to set up a conveyor system and use it for years with few changes,” notes Ken Ruehrdanz, industry manager for Dematic. “Today, however, we may implement a conveyor system, and in less than a year, the user will want to modify it because of a change in business requirements, which supports the need for modular conveyors.”The modular concept also provides capital cost savings, because equipment does not have to be specially engineered. “Everything is built around a universal side frame,” says Ruehrdanz. “If you wanted to change divert points in your conveyor system in the past, there were multiple diverters built with completely separate designs. Today, all diverters/sorters are made from common parts and universal side frames that make changes much easier, faster and less costly.”
For example, a section of roller conveyor may need to be converted to belt surface conveyor, or a transportation conveyor to an accumulation conveyor. “These modifications can be made without the need to remove or replace sections of conveyor. Instead, by utilizing many of the existing components and using the same side channel foundation, a new system configuration can be created more easily,” he explains.
Food companies are introducing new products-and increasing or decreasing volumes-faster than before. Some changes are driven by economic needs-reducing the size of a frozen entrée, for instance, to drive cost per unit down while keeping the same price point. Others are driven by sustainability-switching from corrugated to film overwrap, for instance, to reduce package volume and waste, or switching from one package format to another to achieve easier, more economical recycling.
Dematic’s automatic storage and retrieval system (ASRS) employs stacker cranes that take loads and store them on racks for later use. When products are needed for an order, the stacker crane retrieves the load and sends it to the point of use. Through PLCs and HMIs, operators know exactly where everything is at any given time, which is important not only for production and reporting, but also for traceability purposes.
Dematic also has a system it calls “Multi-Shuttle”-essentially a sequencing staging buffer. It stores a number of different product SKUs in a racking system, then releases each load as required for order fulfillment, palletizing or shipping according to each day’s orders from customers.
Upgrading
Conveyor systems have a long lifecycle, and to extend their life further and avoid new installation costs, a number of options are available. First, a conveyor can be modernized by simply changing the rollers. Worn rollers can produce a lot of noise and damage the side frames. Replacement rollers have universal dimensions and fit into the side frames of almost all conveyor brands.Replacing mechanical sensor rollers with electronic versions allows lighter weight cartons to be conveyed, reduces sound levels and improves carton control. Meanwhile, line shaft conveyors can be upgraded to motor driven rollers (MDRs) as a retrofit. MDR conveyors offer sleep mode (saving energy), accumulation mode, variable speed control and improved carton flow. Pulley motor assemblies, meanwhile, can be replaced with a motorized pulley, which is essentially a drum motor that dramatically reduces energy usage, sound, parts and maintenance.
When DelGrosso Foods of Tipton, PA, one of the oldest and largest family-owned producers of pasta sauce in the US, wanted to increase capacity by 50 percent in its existing plant, it hired Nercon to provide field verification, line layout, engineering and installation.
The high-speed expanded line (500 jars/min.) starts with a new high-speed, pressure-less, single-file conveyor handling empty glass jars. A live drum spiral conveyor feeds a rotary jar rinser and three heat tunnels to pre-heat the glass. The jars are then filled with hot pasta sauce and sent through a horizontal head space and cap sterilizer. The conveyor uses a cylindrical drum that assists in driving the chain, providing low belt tension, increased elevation and increased speed. The full-jar conveying system is engineered to demand-divide and mass flow into two spray coolers. Out of the coolers, jars are recombined using mass flow conveyors with multiple bidirectional tables. A high-speed pressureless single file conveyor delivers full jars to labeling operations. A final bidirectional table is utilized to buffer case packaging operations. Nercon also provided the automated controls and numerous menu-driven HMIs.
“To increase our production speeds, it was critical to have a smart accumulation plan for this whole line,” says Vice President Joe DelGrosso. “We needed to prevent short-term line stoppages that can kill efficiencies. Nercon’s mass flow conveyors and bidirectional tables allow us to continue to run our filler and cooling operations while short-term stops in labeling and case packing are resolved. We designed the labeling and case packaging operations with additional capacity to handle the full production rate and work off the accumulated backlog. This line has improved our overall capacity by 50 percent through higher filling speeds, good accumulation planning and effective line design.”
Innovation, changeovers and hygiene
Some companies are stretching the envelope to satisfy their customers. One of them is Triple/S Dynamics of Dallas, TX, which historically had focused on the production side with a Slipstick Horizontal Motion conveyor, as well as other vibratory conveyors for bulk food. But after a major client ran into a problem on the other side of the filler, Triple/S Dynamics went to work to modify its technology.The vibratory conveyor the company provides on the processing side is called TexFlex. The customer had a problem, however, with the 3- x 3- x 1/2-in. pouches that weren’t spreading out well enough into a monolayer for cartoning. Furthermore, the pouches were occasionally contaminated by food contents escaping from pouches that weren’t sealed properly.
Triple/S modified its traditional TexFlex unit to create a specially designed post-filling vibrating conveyor to spread the pouches in the manner the customer needed. The unit has springs under the conveyor trough and a rotary electric vibratory motor to shake the pan at a predetermined angle and stroke. Immediately after being spread out into the required monolayer, the pouches pass over a screen bed so any loose food pieces fall through and don’t wind up in the cartons later in the line.
“It worked like a charm,” notes Triple/S Sales Engineer Tim Talberg, “and has potentially added a new offering to our portfolio.”
Beyond equipment efficiencies, speeding up changeover times is becoming increasingly important in food plants, and conveyor manufacturers provide a number of solutions. “Many producers run multiple packages in a day, and when they switch to a new package size, they want to be able to reset their machines and conveyors as quickly as possible,” says Nercon’s Streblow. Options range from simple tool-less adjustable guide rails up to automated rails operated by optically controlled PLCs or an HMI. “More automation is able to reduce labor costs, and all the big 100 food companies are going in that direction,” he explains.
Allpax of Covington, LA supplies retort systems and dedicated conveyors to connect the different parts of the lines it manufactures. A critical concern of producers they supply is retort bypass-accidentally sending raw product to labeling. To prevent this, Allpax developed an automated Allen Bradley-based tracking system called Alltrak that controls and tracks basket status from start to finish.
“Our conveyor systems are all modular. What changes is the basket size,” says Allpax General Manager Greg Jacob. “No matter the size or number of our baskets, we use the same shaft sizes, the same bearings, shaft sprockets and chains. This allows users to inventory a common set of parts for their entire plant. For them, it simplifies maintenance.”
One might think that in smaller applications this could result in expensive overkill. Jacob notes, however, when looked at from an overall perspective, savings in lead time, labor, maintenance and common spares outweigh the cost of being modular.
Allpax uses Eurodrive motors, known for their gear reducer design. Shafts are manufactured using an alloy called Silvaloy for optimum durability and electroless nickel plating for corrosion resistance. Lines feature Martin sprockets, a common brand, and Hitachi Perfect Coat chain.
Dorner Mfg. Corp. of Hartland, WI has three levels of hygiene for food plant applications-AquaPruf® and AquaGard®, which are both stainless steel conveyors, and DustPruf®, an aluminum frame conveyor.
DustPruf conveyors include SmartSlots™, which feature flat sides rather than T-slots for attaching stands and accessories, such as sensors, metal detectors and more. “The problem we found with T-Slots in particular applications is they can potentially catch dust, food particles and other debris,” says Marketing Communications Director Jay Schoenwaelder. “The flat sides of a SmartSlot™ eliminate potential build-up, while maintaining all the functionality and flexibility of a T-slot. Plus, the side of the frame can be easily and effectively cleaned.”
AquaPruf provides the highest level of hygiene with completely stainless steel welded frames that can be washed down entirely and eliminate catch points for dust and bacteria growth. AquaGard also offers many hygienic features, but uses bolts in some areas that are welded on the conveyors. The bolts, however, are kept clear of the food zone. This system has become particularly popular in bakery applications.
End-user demands are changing, and producers and their conveyor suppliers have no choice but to follow suit. Every process needs connectivity-the right “circulation system” to provide optimum hygiene, flexibility, fast changeovers and ease of maintenance at the lowest possible cost.
For more information:
Jim Streblow, Nercon, jstreblow@nercon.com, 920-233-3268
Kevin Mauger, NCCAS, kmauger@nccas.com, 215-721-1900
Ken Ruehrdanz, Dematic, kenneth.ruehrdanz@dematic.com, 877-725-7500
Kyle Sobke, Baldor-Dodge Bearings, klsobke@baldor.com, 864-281-2238
Tim Talberg, Triple S/Dynamics, ttalberg@sssdynamics.com, 612-802-8252
Greg Jacobs, Allpax, gregj@allpax.com, 985-893-9277
Jay Schoenwaelder, Dorner, jay.schoenwaelder@dorner.com, 800-397-8664

Baldor-Dodge washdown bearings feature a patented Quadguard sealing system and max-Life Cage design to keep grease in and fluids out. Source: Baldor-Dodge.
Bearings make the world go ‘round
It’s been said that love makes the world go around. Bearings do too. Their absence or failure can cause conveyors and other food plant machinery to shut down-one of the reasons bearing factories were such a high priority target for Allied bombing raids in World War II. In a plant, conveyors connect everything, but it’s the bearings that enable the conveyors to run, the motors that drive them to operate and the reducers to control speed.The main enemies to bearing life and performance in a plant are moisture, contamination, corrosion (rust) and inadequate lubrication. Product Business Manager Kyle Sobke at Baldor-Dodge Bearings in Fort Smith, AR says average bearing life in food plants, which are typically characterized by tough washdowns, can be limited substantially by the harsh environment. “When bearings fail, part of the plant has to be shut down. So it’s not just the cost of the replacements you need to consider, but more importantly, the lost productivity.”
According to Sobke, Baldor-Dodge bearings used in food plants can provide improved performance and longer life. “Our approach is to offer higher-quality products that save the user costs associated with frequently replacing failed bearings.”
Two main factors contribute to this-the Quad Guard sealing system and the Max-Life Cage design. The Quad Guard system features a geometrically designed triple-lip seal along with a rubberized flinger (a disc with wide-angled spokes) that physically prevents water and caustic washdown fluids from entering the inner workings of the bearing. The Max-Life Cage, a specialized retainer that holds the rolling elements in place within the ball track, is geometrically designed to keep the lubricating grease from being washed out.
“The standard lubricant in a food plant is H1 food-grade grease, which doesn’t stand up as well as non-food-grade grease to moisture, hot-pressure spraying and caustic chemicals,” notes Matt Frady, Baldor-Dodge roller bearing product business manager. “That’s why we’ve put such an emphasis in building a robust sealing design to protect this more delicate grease from liquid exposure.”
Baldor-Dodge does a business with OEMs that build new conveyors, as well as directly with end-users that want to retrofit or upgrade their existing lines. Bearing housings are generally built to standard dimensions across the industry, so replacing one brand with another is usually easy to do.
“We completed a retrofit for a large meat producer in Nebraska in early 2010, and when I visited that plant a year later, our bearings were still running fine,” says Sobke. “This facility went from replacing ball bearings every two to three months to realizing more than a year’s worth of life out of their ball bearing solution. With the number of mounted bearings in a plant ranging from the hundreds to the thousands, the goal is to get as much life as you can before you have to replace any of them.”

Campbell Soup v-8® v-Fusion beverages in 12-ounce PeT bottles move down the line on a new conveyor with adjustable rails. Source: Campbell Soup.
New conveyor systems speed changeovers at Campbell Soup
Infinite adjustability, quick and repeatable changeovers, and ease of use were some of the key items a Campbell Soup plant in Paris, TX was looking for in the conveyor solution for a new beverage production line it installed in early 2010.The line produces V-8® vegetable juices, V-8® V-Fusion beverages and V-8® Splash juice beverages in five different PET bottle sizes, ranging from 12 to 64 ounces.
“We were looking for a side rail system that could provide rapid changeovers between the current package sizes, and possible new ones that we may introduce in the future,” says Campbell Soup Group Engineering Manager Bob Gibson. “We ended up using a system that is interconnected by shafts and adjusted using guide blocks, zone by zone, by a hand crank. It’s easy and precise to go from one package size to another,” says Gibson. “Adjusting corners is as easy as the straight sections.”
According to Gibson, to optimize conveyor performance, particularly for PET bottles, it is critical that lubrication is maintained to reduce friction between the belt and the containers. Rather than using the standard soap and water approach, which results in wet floors and corrosion on conveyor bearings and other parts, he and his team decided to use a dry lubricant. “All it takes is a couple of seconds of spray every hour to reduce pressure on the line,” explains Gibson. “It’s more sanitary, there’s no mess to clean up, and you save money by not having to install drip pans.”
The following vendors were used on this project: Barry-Wehmiller Companies Inc., Septimatech Group Inc, Ecolab and Intelligrated.