Dry Processing Technology
Snack maker finds a better way to control ingredient flow.
For more than 50 years, Zweifel Pomy-Chips, AG, (Spreitenbach, Switzerland) has been one of the largest snack food manufacturers in Europe. The company produces about 5,000 tons of potato chips annually, and another 1,200 tons of snacks are produced from grain and corn.
Known for innovative chip flavors and recipes such as Nature, Paprika, Provençale, Curry and Mexican, Zweifel strives for quality coating and consistent delivery of the seasoning blend to the potato chip manufacturing process. The problem was that existing equipment wasn’t delivering consistent quantities and perfectly repeatable blends to the coating process. This not only affected flavor but also wasted expensive ingredients when greater-than-needed amounts were delivered. Zweifel needed a better way to meter the ingredients to the coating process.
The processor looked at volumetric feeders and loss-in-weight (LIW) feeders. Volumetric feeders are relatively inexpensive, but are open-loop and don’t take into account fluctuations in material density. LIW feeders work on weight or mass and can be used in a closed-loop control system. Zweifel considered LIW feeders a good solution for controlling its ingredient flow, and it chose K-Tron LIW gravimetric screw feeders.
Martina Burger, manager technical services for Zweifel, describes the process. “During the coating process, the seasoning ingredient or blend is fed directly to the feeder hopper, which delivers the product to an extended single screw.” She adds, “Screw feeders are used due to their ability to deliver difficult flowing materials (e.g., seasoning powders with high oil contents) directly and evenly to the process and without surges in flow. The seasoning powder flows from the screw directly to the coating drum, in which potato chips are rotating at a fixed rate.” The precisely measured flow of seasoning results in consistent coating of the chips while maintaining quality and taste.
Single screw feeders equipped with a 60mm-diameter screw deliver salt, paprika and other seasonings at rates of 5 - 200 kilo/hour (1 - 440 lbs./hour). A control system manages recipes. Depending on the seasoning to be added, the operator chooses which recipe is required, and the controller adjusts the feeder variables accordingly. Zweifel finds the feeder is easy to clean and maintain, allowing quick process changeovers when the spices/ingredients are changed.
Zwiefel’s LIW feeder consists of a hopper and feeder that are isolated from the process so the entire system can be continuously weighed. As the feeder discharges seasonings, system weight declines. The LIW feeder controller adjusts feeder speed to produce a rate of weight loss equal to the desired feed rate setpoint. With this technology, a constant mass flow is ensured, providing consistent product delivery to the coating device. LIW feeder controls verify the material is flowing and send an alarm if material flow is stopped by an upstream problem. u
For more information, Sharon Nowak, 856-256-3119, snowak@ktron.com

Eriez, 888-300-3743, www.eriez.com
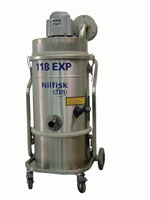
Nilfisk, 800-645-3475, www.stop-the-dust.com

Littleford Day, Inc., 800-365-8555, www.littleford.com
Bindicator, 800-778-9242,
www.bindicator.com
NBE Inc., 616-399-2220, www.nbe-inc.com

Flexicon, 888-353-9426, www.flexicon.com

Sweco, 800-807-9326, www.sweco.com
Powder-Solutions, 877-236-3539,
www.powder-solutions.com
Fortress Technology Inc., 888-220-8737,
www.fortresstechnology.com

Great Western Manufacturing, 913-682-2291, www.gwmfg.com

Sweco, 859-371-4360, www.sweco.com

Modern Process Equipment, 773-254-3929, www.mpechicago.com

Material Transfer & Storage, 800-836-7068, www.materialtransfer.com
Radio Frequency Company, Inc., 508-376-9555, www.radiofrequency.com

At Zweifel, K-Tron loss-in-weight feeders accurately deliver the right amount of seasoning mix, producing consistently flavorful potato chips. Source: K-Tron
Known for innovative chip flavors and recipes such as Nature, Paprika, Provençale, Curry and Mexican, Zweifel strives for quality coating and consistent delivery of the seasoning blend to the potato chip manufacturing process. The problem was that existing equipment wasn’t delivering consistent quantities and perfectly repeatable blends to the coating process. This not only affected flavor but also wasted expensive ingredients when greater-than-needed amounts were delivered. Zweifel needed a better way to meter the ingredients to the coating process.
The processor looked at volumetric feeders and loss-in-weight (LIW) feeders. Volumetric feeders are relatively inexpensive, but are open-loop and don’t take into account fluctuations in material density. LIW feeders work on weight or mass and can be used in a closed-loop control system. Zweifel considered LIW feeders a good solution for controlling its ingredient flow, and it chose K-Tron LIW gravimetric screw feeders.
Martina Burger, manager technical services for Zweifel, describes the process. “During the coating process, the seasoning ingredient or blend is fed directly to the feeder hopper, which delivers the product to an extended single screw.” She adds, “Screw feeders are used due to their ability to deliver difficult flowing materials (e.g., seasoning powders with high oil contents) directly and evenly to the process and without surges in flow. The seasoning powder flows from the screw directly to the coating drum, in which potato chips are rotating at a fixed rate.” The precisely measured flow of seasoning results in consistent coating of the chips while maintaining quality and taste.
Single screw feeders equipped with a 60mm-diameter screw deliver salt, paprika and other seasonings at rates of 5 - 200 kilo/hour (1 - 440 lbs./hour). A control system manages recipes. Depending on the seasoning to be added, the operator chooses which recipe is required, and the controller adjusts the feeder variables accordingly. Zweifel finds the feeder is easy to clean and maintain, allowing quick process changeovers when the spices/ingredients are changed.
Zwiefel’s LIW feeder consists of a hopper and feeder that are isolated from the process so the entire system can be continuously weighed. As the feeder discharges seasonings, system weight declines. The LIW feeder controller adjusts feeder speed to produce a rate of weight loss equal to the desired feed rate setpoint. With this technology, a constant mass flow is ensured, providing consistent product delivery to the coating device. LIW feeder controls verify the material is flowing and send an alarm if material flow is stopped by an upstream problem. u
For more information, Sharon Nowak, 856-256-3119, snowak@ktron.com

X-ray cabinet inspection system
Eriez’s model XR-21 series cabinet inspection system identifies contaminants, scans for missing or broken products and detects packaging voids. The device can be used with both packaged and continuous bulk product flows, and is capable of handling products up to 12 in. wide with varying speeds. With a Windows XP-based GUI, the system includes a 15-in. full color screen display that displays real-time images and diagnostic data. USB and RJ-45 connectors located on the outside of the machine make it easy to connect to computers and industrial networks.Eriez, 888-300-3743, www.eriez.com
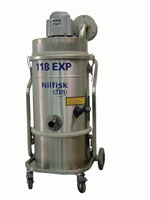
Hazardous locations vacuums
For use in hazardous, potentially explosive environments, Nilfisk’s CFM 118 EXP series of explosion-proof, intrinsically safe vacuums is available in two electrically-powered models: the 118 EXP for the pickup of dry materials and the 118 EXPW for picking up liquids and other wet, hazardous materials. The 118 EXP series is CSA-approved for use in Class I, Group D and Class II, Groups E, F and G. For use in environments where electricity is undesirable or unavailable, the pneumatic A15EXP series consists of two separate models for dry or wet pick up. All models are composed of stainless steel; the pneumatic models come with a conductive, 50-ft. air supply hose.Nilfisk, 800-645-3475, www.stop-the-dust.com

Easy-to-clean mixers
Littleford Day’s Ploughshare mixer is available for batch or continuous material processing and has a full access door across the front, making it easy to clean. The mixer can be used to prepare bakery mixes, dry soups and gravy mixes, spices and flavorings, powdered drink mixes and more. The mixer is available in average working capacities from 0.11 cu.ft. to 2.77 cu.ft. in 4 lab versions and in production versions from 6 to 533 cu.ft. in 13 models.Littleford Day, Inc., 800-365-8555, www.littleford.com
Level measurement
Bindicator’s TDR-1000 provides a continuous, non-mechanical level measurement by means of low-power radar pulses guided along a stainless steel cable. The device is well suited for determining the level of solids, granules and powders as well as a variety of liquids. For several applications, the gauge can be used instead of conventional capacitance, ultrasonic and plumb bob technologies.Bindicator, 800-778-9242,
www.bindicator.com
Automated bag discharger
For applications where food industry copackers accurately feed a wide variety of materials to its packaging lines in an automated dust-free manner, NBE has integrated the discharger’s automated controls package with the copacker’s downstream packaging line. This provides the allocation of materials based on actual demand from the packaging line.NBE Inc., 616-399-2220, www.nbe-inc.com

Sanitary bag unloading system
Flexicon’s model BFC-F-X unloading system eliminates dust during untying, discharging, retying, collapsing and removing of bags while allowing a thorough washdown. The unloader is equipped with a clamp ring that forms a dust-tight connection between the clean side of the bag spout and the clean side of the equipment. The airtight system is vented to an integral dust collector that vacuums displaced air and dust and collapses empty bags dust free. All stainless steel construction with continuous ground and polished welds meets food and dairy standards.Flexicon, 888-353-9426, www.flexicon.com

Conveyor, feeder, screener
Sweco’s Feed-Vac Vibro-Energy separator system combines the functions of conveying, storing, feeding and screening of dry materials into one complete unit. The separator can size product into 2 to 5 fractions and can be combined with the company’s Accu-Feed system, a conical storage bin with an adjustable feed controller. The combination eliminates the need for a separate feeder and hopper. An adaptable vacuum conveying system transports most dry powder and granule products through a dedicated pipe system to the Accu-Feed and separator.Sweco, 800-807-9326, www.sweco.com
Flexible connector
Powder-Solutions’ BFM snap-in flexible connector system prevents product build-up between flexible connectors and the side wall of spigots. Each connector system is made up of two 304 stainless steel BFM fitting spigots, which are permanently attached to existing pipes or spouting and a flexible, snap-in connector.Powder-Solutions, 877-236-3539,
www.powder-solutions.com
Low-profile metal detector
Fortress Technology’s compact metal detector, the Phantom series Vertex, fits in restricted spaces and features aperture sizes of 6.5/8.5 inches (165/216 mm). Available in a painted aluminum case (standard) or stainless steel, the metal detector integrates with vertical form-fill-seal machines for pouch packing solutions, typically situated beneath a multi-head weigher in snack food and powder processing applications. The detector works well in applications where packaging is metallic or too large for standard detectors.Fortress Technology Inc., 888-220-8737,
www.fortresstechnology.com

In-line sifter
Great Western’s QA36 pneumatic, in-line sifter handles more than 500 lbs./min. of soft wheat flour and more than 650 lbs./min. of hard wheat flour using a 30 mesh screen. The device’s sanitary design and light-weight components plus snap-on neoprene gaskets make maintenance tasks relatively easy. The sifter uses a gentle gyratory sifting motion, and can be inserted into a vacuum or dilute phase pressure pneumatic conveying system.Great Western Manufacturing, 913-682-2291, www.gwmfg.com

Classifier for fine products
Sweco’s Alpha classifier (from Ecutec S.L., Barcelona) handles dry powders from 150 microns down to 6 microns. Depending on the fineness required, the equipment can be fed by gravity from the top or in the main airstream from below, and can be customized with either stainless steel, ceramic or polyurethane for wear protection and specific material requirements. The device is also available with options to meet a variety of air classification needs.Sweco, 859-371-4360, www.sweco.com

Granola grinder
Modern Process Equipment (MPE) Corp.’s model 88 WC granola Gran-U-Lizer particle reduction system uses water-cooled rollers and a proprietary tooth profile to cut and tear granola into a variety of grind profiles. Typical capacities range from 1,000 to 4,000 lbs. per hour, depending on the grind size setting. The machine eliminates the need for screens and simplifies the production process.Modern Process Equipment, 773-254-3929, www.mpechicago.com

FIBC filling system
Material Transfer’s Material Master PowerFill FIBC flexible intermediate bulk container filling system features a horizontal and rotating bag fill carriage. The bag support carriage and fill head lower to a programmed operator height, extend toward the operator, then rotate for reach-free bag strap and bag spout connection. PLC controls and discharge conveyor provide efficient operation.Material Transfer & Storage, 800-836-7068, www.materialtransfer.com
Radio wave pasteurization
Radio Frequency Company’s Macrowave pasteurization systems are well suited for batch or conveyorized applications for bagged or bulk products. A 40 MHz radio frequency generator creates an ac field between two electrodes, and as the material to be treated passes through the field, microbes are killed due to the rapid heating effect. The electrode arrays are designed to provide the depth of penetration needed and uniform heating throughout the material as it passes through. Systems are available for nut meats, spices, pasta, tobacco, fishmeal and other food ingredients.Radio Frequency Company, Inc., 508-376-9555, www.radiofrequency.com
Looking for a reprint of this article?
From high-res PDFs to custom plaques, order your copy today!