Tech Update: Wireless networks provide critical measures
Applications are vast as the imagination can create
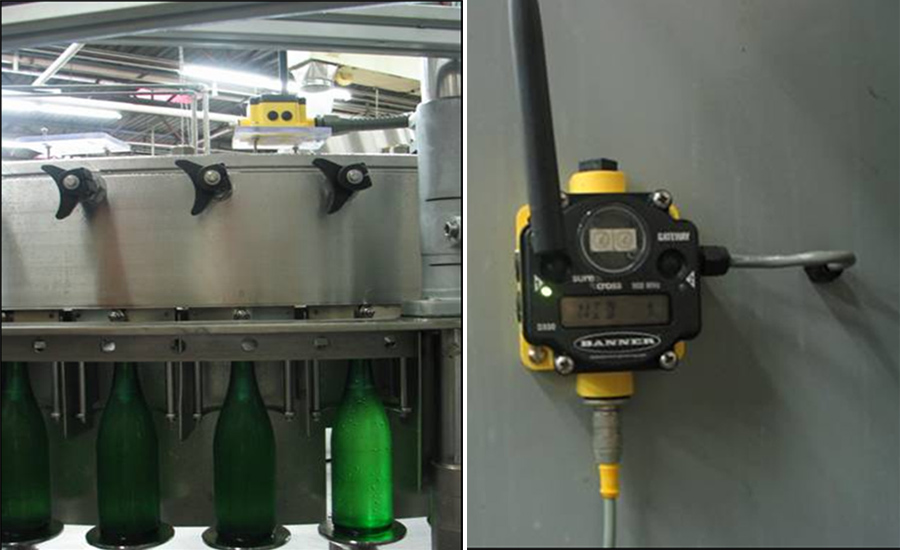
Say you’d like to keep track of what’s remaining in your ingredient storage silos. It’s not the cost of the level sensors that’s the problem. It’s the trenching and running underground and overhead wires that cost more than five high-end level sensors. Say you want to measure critical temperatures at key points in your process, but you’d like to be able to move these sensors at a moment’s notice to check other areas. What’s holding you back? Once again, it’s the wiring (and cost) issue.
Why not give wireless sensors a try? Depending on your budget, you can get wireless sensors from traditional controls vendors such as ABB, Emerson Process, Honeywell, Invensys and Yokogawa, or find devices from traditional sensor vendors like Banner Engineering and Omega Engineering. PLC suppliers such as Rockwell, Siemens, Schneider and Mitsubishi also have wireless solutions. You won’t be at a loss for choice; in fact, you might be overwhelmed by the available selection. And, to add to the confusion, some industrial wireless standards are still in limbo, creating a profusion of proprietary solutions-just like the commercial/home wireless market of not so long ago.
If you purchased a wireless router for your home network five years ago, you may have found it a little tricky to set up; and if you have honest neighbors, they may have told you they enjoyed surfing the Web on their laptops, thanks to the free wireless Internet access you offered because your router either lacked security, or the instructions were written so poorly you couldn’t understand the security set-up. Today’s wireless routers are a far cry from those of five years ago, and security features have improved as well. In fact, they’re almost “plug-and-play.”
This article will look at some of the issues affecting wireless sensor networks and “backhaul” networks; the latter networks help relay signals collected from sensor networks to the wireless access points of control or asset monitoring systems. Though cell phones, PDAs and RFID systems are already well employed in food and beverage plants for the obvious communications, email and Web-based warnings and product tracking, this article will concentrate on getting the process signals you need from challenging locations.

The self-organizing Smart Wireless system provides accurate minute-by-minute readings from 16 measurement points on a reaction tank located about 250 feet from the central control room. Source: Emerson Process.
Licensed systems for the long haul
In the past, if you needed to get a process signal from point A to point B, you paid a monthly fee to the telephone company (telco) for a secure, always-on, two-wire or four-wire tie line. If you had a lot of signals to monitor and didn’t multiplex signals on a single line, you found several tie lines could get pricey. Telco lines, however, were secure and could provide 99.999% reliability.
Another option, licensed narrow-band FM radio systems operating in VHF or UHF bands, provided an alternative to the tie line and are still viable today. Once in place, this equipment is relatively inexpensive to operate on a monthly basis, but an ROI may not be quickly realized due to high initial costs for the radio equipment itself, installation, site studies, license application and ancillary support equipment. Plus, maintenance and proof of performance for this equipment have to be done by FCC-licensed engineers or technicians.
One problem a licensed system is supposed to solve is interference. “Anyone who uses a license wants to insure he/she has no interference or issues with someone transmitting on the licensee’s frequency,” says Frank Williams, vice president with ElProTech.
Another issue can be a frequency-specific noise source, which according to Darvin Kaelberer, business development manager at Banner Engineering, may not be a situation that can be remedied by the FCC. Instead, locating the on-channel noise source and finding ways to reduce its emissions may be the only fix.
While a SCADA system operating on a licensed channel has advantages of distance and a clear channel, Williams points out that the recurring costs and narrow bandwidth may not fit the needs of some automation systems where high data throughput is necessary. But for a long haul, where a processor has two plants separated by 15 miles or more, a licensed channel may be a good option.
With distances of up to two miles separating various buildings (and just a little too far for reliable Wi-Fi), traditional hardwired networking proved to be too costly for Bacardi’s Cataño, Puerto Rico distillery facility. Bacardi chose to install five ESTeem 192C modem/radios to link key buildings at the complex. The licensed-based system operates at 19,200bps and provides a data accuracy better than one part per 100 million. Pulling together the SCADA system, a modem/radio at each building is interfaced with a Rockwell MicroLogix PLC. A central computer retrieves data from each remote system.
Cliff Whitehead, Rockwell Automation strategic applications manager, says licensed radios will persist specifically because they are licensed. Users want control over the radio system and can achieve more control within these bands. He adds, “As the [unlicensed] ISM (industrial, scientific and medical) bands get more and more crowded with devices and deployments, users will consider this option as they look for ways to optimize their communication. SCADA applications are still good examples for this class of communication.”
Today, when people think of wireless communications other than cell phones and PDAs, inexpensive wireless access points and routers found in home computer networks often come to mind. Wireless communications devices can generally be broken down into two major groups defined by IEEE. Both groups operate on low power and do not require the user to obtain an FCC license. The first group, IEEE 802.11 devices, refers to Ethernet-based wireless routers, gateways and portable computers. These “Wi-Fi” networks, while used in home and office applications, can also be used to link industrial and sensor networks.
Sensor networks, which consist of IEEE 802.15.4-compatible devices, are typically made up of lower-powered, shorter-range devices and can be placed in clusters to form a “mesh” network. All 802.15.4 devices are intended to operate at very short distances (typically less than 100m). One 802.15.4 technology with which most people are familiar is Bluetooth for personal communications. Other technologies intended for industrial applications include ZigBee, WirelessHART and the ever-evolving ISA100.11a. While IEEE specifies the basic physical layers and media access control (MAC) layers in the OSI seven-layer network model, it does not actually get involved with the all-important application layer seven. Layer seven actually defines the protocol devices will use, such as Modbus, Profinet, WirelessHART, ZigBee objects, etc.

Making it transparent
According to a Frost & Sullivan report entitled Wireless Devices in Factory Automation-An Overview of Adoption Trends, the key reason for wireless adoption in factory automation is the need for real-time data and workforce mobility. End-users indicate that constant monitoring of the process is a major requirement in the process automation set-up, as this enhances quality at every step of the process. Yet, major concerns about wireless adoption are reliability and security. End-users perceive that for a plant to operate around-the-clock, current wireless technology doesn’t provide the necessary robustness. Reasons cited are signal mismatch, interference from intended/unintended emitters and data loss in transmission.
Couple these issues with understanding wireless theory and practices, and it’s no wonder processors are reticent to adopt wireless. Bob Karschnia, VP of wireless at Emerson Process, explains, “If we were to train the entire industry on wireless technology, including parameters such as gain, path loss, receiver sensitivity, multipath degradation and all the rest of these wireless-based terms, we would find that our customers and my sales force wouldn’t have the time to learn wireless facts.” Technology gets deployed, adds Karschnia, when it becomes invisible-when it goes to the masses.
In some ways, radio suppliers are as perplexed as end-users while they try to focus new products at changing standards and market demands. Joel Young, CTO and senior vice president of R&D for Digi International, describes producing RF (radio frequency) modules called XBees, which he says can be easily adapted to any 802.15.4 networking standard. The challenge is keeping up with market demands for these modules, should WirelessHART and ISA100.11a take off. Digi already produces modules for ZigBee and its own Digi Mesh. “If WirelessHART takes off in the process industry, we’ll create an XBee module to put in a partner’s sensor to create a complete WirelessHART module,” says Young. By the time the ISA100.11a standard solidifies next year, he’ll have an ISA100.11a XBee module ready to go.
The real issue with all this technology, concludes Young, is that it must be transparent for the end-user. Users know what to do when their cell phone drops a call or how to locate another Wi-Fi network, but when you take out the human in an industrial application, the device has to work, and that can be a difficult challenge.
Wi-Fi for the longer haul

When most people think of wireless, they think of Wi-Fi. Wi-Fi is a trademark of the Wi-Fi Alliance, which was founded in 1999 as the Wireless Ethernet Compatibility Alliance (WECA). The group was formed because various vendors demonstrated little consistency in implementing 802.11 standards. (The most common Wi-Fi systems are summarized in the table at the end of this article.)
Since Wi-Fi systems operate continuously in master-slave configurations, they don’t make good sensor networks as they continuously use power and can’t run off batteries. Conversely, Williams adds, because 802.15.4 sensor networks don’t cover longer distances, they aren’t a good choice for the longer haul, the backhaul. However, Wi-Fi networks do make good relay systems in bringing data from sensor networks to wired LAN access points. Williams cited an installation at Gerber where both networks are used to grab process data for process control systems.
Further improvements are ahead for Wi-Fi. According to Whitehead, 802.11n (Wireless-N) looks attractive as a means to extend beyond infrastructure to peer-to-peer and lower-level, high-speed wireless communication in manufacturing operations. Currently, the speeds of today’s wireless mesh networks make it impractical for high-speed sensing needed in a packaging machine.
Wi-Fi is everywhere, but commercial-grade devices won’t suffice for industrial operations, warns Williams. While, of course, NEMA 4 or better housings make a difference, power levels and antenna design separate industrial Wi-Fi devices from the SOHO/commercial devices. Most commercial devices that sell for about $50 have a 10mW output, and the more expensive (about $250) units produce 100mW output. But an industrial-strength unit should have at least a 300mW output that can provide two-mile, line-of-sight coverage. Processors might choose to go the legal limit at 1.0W to get the maximum coverage, but they should expect to pay around $2,000 for the higher power rating.
Sensor networks
Wireless sensors take advantage of the 802.15.4 standard, which allows for data throughput of up to 250 kbits/s on three bands (868-868.8, 902-928 and 2400-2483.5 MHz). The standard defines full-function devices that serve as the coordinator of a network or just a common node, and reduced-function devices that are meant to have modest resource and communication requirements. Networks may follow either a point-to-point or star topology.
According to Tim Cutler, director of product marketing at RFM, ZigBee was one of the first protocols to take advantage of 802.15.4, and now uses ad-hoc, on-demand distance vector routing (AODV) similar to mesh networking. ZigBee Pro makes use of a newer routing scheme that keeps routing tables and allows routes to expire and be replaced with new ones. The ZigBee Alliance chose home and commercial electrical systems (lighting and HVAC) as a primary market, but also thought ZigBee might be applied to industrial applications. Limitations such as lack of frequency diversity and mostly mains-powered nodes, according to Cutler, slowed the adoption of ZigBee for industrial applications.
The heart of most 15.4 standards, mesh technology, says Williams, was built on the peer-to-peer model, where nodes communicate with one another to pass along data. As opposed to a master-slave system like Wi-Fi, there is more than one path (provided there are at least three or more nodes), which improves overall reliability. Nodes talk when they have something to say (report by exception) or relay data, which reduces power needs significantly, allowing long battery life. Early peer-to-peer networks needed some configuration so nodes knew which alternate path to take should one path fail. According to Williams, it was Dust Networks that took the concept a step further and created a low-power, self-organizing, self-healing mesh network.
In addition, says Cutler, Dust took a 15.4 radio, turned it into a frequency hopper and synchronized the entire mesh network so the nodes could sleep. This is what Dust called the time synchronized mesh protocol (TSMP). A joint project produced the protocol used in Emerson’s wireless sensors and became the germ of WirelessHART.
Three radio methods, says Karschnia, were key to the Emerson-Dust joint project in making a 15.4 mesh radio work in process control, and they all minimized the possibility that standalone wireless sensor nodes (or motes) would interfere with one another or experience interference from a nearby Wi-Fi node. The first method, TSMP, keeps motes from transmitting simultaneously. Frequency diversity allows motes to operate on different channels, and spatial diversity keeps pairs of motes that do communicate at the same time a safe distance apart to minimize interference.
WirelessHART and ISA100.11a
WirelessHART was approved by a vote of the HART Communication Foundation (HCF) general membership and ratified by its board of directors in September 2007 as part of the HART 7 specification. September 2008 saw the approval of WirelessHART specification by Europe’s IEC, and four major vendors have signed on to support the specification. These include ABB Instrumentation, Emerson Process Management, Endress+Hauser and Siemens. In addition, HCF, Fieldbus Foundation and Profibus Nutzerorganisation have formed a Wireless Cooperation Team to create interoperability among their respective protocols by developing a common interface to a wireless gateway.
According to Whitehead, like WirelessHART, ISA100.11a focuses on periodic process monitoring applications, predominantly for stationary transmitters that form a mesh. Features designed into the ISA100.11a standard will allow the development of devices for higher speed (10 millisecond) applications. The ISA100.11a family also includes work performed on other industrial wireless uses such as backhaul networks, factory automation (discrete/hybrid), people and asset tracking/locating, trustworthiness, etc.
WirelessHART addresses all seven layers of the OSI model-from hardware right up to applications-just like its wired sibling, HART, says Karschnia. Therefore, users buying HART-compatible products know their devices will work together. ISA100.11a is an umbrella specification that includes Modbus, Profibus, FOUNDATION fieldbus and other technologies. However, there is some concern that data on the network from all these protocols may not be able to intercommunicate without layer seven gateway devices-much the same as it is in the wired world.
With evolving standards and developing markets, radio suppliers are taking a wait-and-see approach to production of standards-based equipment. Kaelberer says that while Banner has made efforts to comply with ISA100, WirelessHART and ZigBee at some level, it will continue to use its proprietary platform until there is a solidified demand for devices with the other three protocols. In the meantime, a gateway will allow Banner’s sensors to connect anywhere or to Ethernet/IP and Modbus TCP devices.
Even though ISA100.11a isn’t finished, Williams says an over-the-air upgrade capability feature built into the standard will help backward and forward compatibility. Williams advises manufacturers that they don’t have to wait until next year for the final ISA standard to be published to purchase ISA100.11a-compatible devices. In the meantime, he says, when processors deploy wireless today, they need to verify from suppliers that the devices’ firmware can be upgraded over the air as the ISA specification becomes finalized.
Project considerations
It’s important to remember no one frequency or wireless standard will solve all application problems, says Eric Marske, ESTeem Wireless Modems product manager. Correct selection to match the application is critical. Typically, lower operating frequencies have greater range than higher ones (other factors the same). Inside buildings, higher frequencies tend to bounce around and fill in hard-to-reach spaces, but outside, they tend to be more quickly attenuated by foliage.
Marske points out that any wireless system project should consist of three phases: an RF design program (computer-based) to estimate RF results; a radio site survey consisting of an on-site analysis and confirming the results obtained in the RF design phase; and site commissioning, which includes building a system backbone after final installation. The site survey should include inspecting all locations in the system, performing RF testing at all sites and confirming the reliability of the RF design program.
Fortunately, security levels of wireless networks are improving; the weak link is often the human part-employees forgetting to set security encryption levels and user access, creating weak passwords, leaving open screens, etc. Karschnia says Emerson’s security is on a par with the security used in banks transferring funds to the Fed, and he thinks most hackers would rather go after a bank than read a tank or silo level.
Cutler says most wireless systems support AES 128 encryption, white listing and join-permitting. Security is well understood to be very important in all systems, and the standards groups are all implementing security in a similar fashion.
Applying wireless
There are many wireless applications, such as reading a silo/tank level/pressure from across the street, tracking temperatures in a winery’s cellar, monitoring temperatures in a freezer to make sure all zones are correct, verifying oven temperatures are correct or using wireless-based sensors to check all the HACCP data to ensure product is kept at the proper temperatures and CIP fluids meet regulatory requirements.
Another natural application for wireless is monitoring environmental parameters whether inside a building or outside, for example, monitoring the ground moisture content, temperature and humidity for improving growing conditions or yields in agriculture, says Shana Farley, Crossbow Technology sales manager. The wine industry has been intent on increasing quality and quantity while minimizing resources, so remote monitoring allows exact control of a precious resource, water.

Applications for wireless are as vast as the imagination can create them. But before choosing a specific technology, be sure you know what you want to accomplish. Don’t necessarily rely on one vendor or supplier to have all the answers.
Looking for a reprint of this article?
From high-res PDFs to custom plaques, order your copy today!