Developing Quality Cannabinoids
The right equipment and processes are essential to developing high-quality and safe ingredients from cannabis and hemp.

Image Source: Courtesy of Vanguard Scientific
As the cannabis-infused food and beverage industry continues to grow, progressively expanding into mainstream America, variables related to finished product quality, safety, and consistency will rise to the forefront of industry concerns. And one of the primary variables impacting finished infused foods and beverages is ingredient quality.
In order to learn more about variables impacting extraction, distillation, and purification of cannabis ingredients like cannabidiol (CBD), tetrahydrocannabinol (THC), terpenes, and more, we reached out to: Chris Chappie, senior vice president, systems integration; Amy McDonald, director of quality operations; and Nick Herbst, vice president, engineering, all members of the scientific leadership team at Vanguard Scientific, Aurora, OR.
DOUGLAS J. PECKENPAUGH: What are currently the most-common approaches toward extracting cannabinoid ingredients from non-psychoactive hemp and/or THC-containing cannabis for use in infused foods and beverages?

CHRIS CHAPPIE: Ethanol is most frequently used for large-scale productions, with throughputs of up to 1,000 lbs. a day. Ethanol is largely considered the most cost-effective pathway to distilled oil production, particularly at scale. This is why ethanol is most often chosen for non-psychoactive hemp and/or THC-containing cannabis for use in infused foods and beverages as opposed to other methods—but it does have its weaknesses. Ethanol is not the best choice for terpene preservation due to the processes that remove the solvent. Terpene compounds are quite delicate in nature, and the overall aggressive nature of ethanol extraction tends to harm or destroy these compounds entirely during the process. But it is still a highly efficient solvent for extraction efficiency and distillation production. This distillate can then be infused into foods, or further processed for inclusion into water-based beverages.
CO2 and CO2/co-solvent are frequently used at lower-scale productions, such as craft outlets. CO2 is largely renowned for its ability to produce very pure and high-quality extracts due to the delicate nature and temperatures that it is able to maintain during the extraction process. This delicate nature is why it is so often chosen at the smaller and more niche-focused craft scales that focus on unique flavor and experience profiles as opposed to mass throughput.
Interestingly, we also see that CO2 and CO2/co-solvent comes back into use at the highest-scaled productions due to efficiencies that it is able to achieve at massive scale and lower operating costs when compared to ethanol at that same scale. CO2 is best at capturing and preserving terpene profiles of the original plant material, but is less efficient than ethanol in overall extraction percentages. The co-solvent add-ons introduced to major systems in the last few years have evened the extraction efficiencies between these technologies and sped up the overall extraction process using CO2. The terpenes and distillate from the CO2 process can then be infused into foods or further processed for inclusion into water-based beverages.
While hydrocarbon extraction is still popular with legacy markets for smokable THC products, they are not being used commercially for ingredient production and inclusion into beverages and foods at any level beyond small-batch productions.
DJP: What are some of the other top benefits/drawbacks of these technologies?
CHRIS CHAPPIE: Every approach has its own benefits and challenges.
Ethanol production benefits:
• Lower initial equipment costs compared with CO2
• High extraction efficiencies
• Scales up well for small to medium-sized operations
Ethanol production drawbacks:
• Higher cost to operate compared with CO2
• Higher level of safety compliance and building infrastructure required
• Scaling up to mass scale throughputs requires changes to building that are cost-prohibitive
CO2 and CO2/co-solvent benefits:
• Lower cost to operate when compared to ethanol
• Easier to install and license with regard to safety regulations at every scale
• Easiest and cleanest way to capture and preserve the terpene profile of the plants
CO2 and CO2/co-solvent drawbacks:
• Higher initial cost of equipment compared to ethanol
DJP: How can ingredient processors manage quality-control variables via those common approaches?
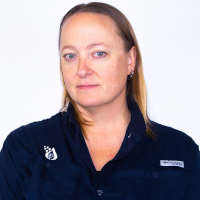
AMY MCDONALD: When it comes to extraction, a robust and measured quality management system (QMS) is the best way to maintain quality control. A QMS consists of all the necessary documentation and procedures required to manage each step of the extraction process—from grinding all the way through to distillation and product testing. Specifications for incoming goods and materials, as well as in-process specifications, will aid processors in controlling the reproducibility of final products.
As it pertains to equipment-specific quality control, a key component is the equipment itself. Utilization of automated, software-controlled equipment can help reduce employee-dependent variations in operation and, therefore, product consistency. Currently available equipment in the industry varies widely as it pertains to automation or manual operation. Regardless, a QMS with detailed documentation and equipment specific standard operating procedures (SOPs) is crucial to managing the quality-control variables associated with extraction. Equipment manufacturers who take cleaning, calibration, and maintenance activities into consideration when writing a manual will make the creation of the SOPs much more straightforward.
Again, the key to the best quality, reproducible product is the documentation of every step of the process. Everything coming into and leaving the building must be understood and controlled through specifications and employee training within a QMS.
DJP: What current cannabinoid extraction, distillation, and/or purification equipment do you currently have available?
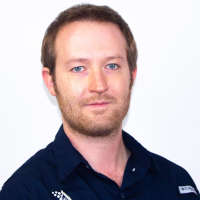
NICK HERBST: In early 2021, Vanguard Scientific released the MIDAS XII-CS model of our premiere CO2 extractor, the MIDAS XII.
The MIDAS XII was largely renowned for its small footprint and precise tunable parameters, making it the perfect extraction system for operators looking to create extracts with unique flavor profiles and experience formulations. The MIDAS XII comes standard with an on-board and fully integrated software system that allows operators to control and automate all parameters of the extraction cycle, while also allowing operators to save those parameters as recipes, to allow for consistent and repeatable extraction.
Now, with the introduction of the MIDAS XII-CS, operators are able to take advantage of all of the features of original MIDAS XII, including the small overall footprint, and controllable software parameters, while also increasing the throughput of the system by over 200 percent.
The CS takes advantage of the best capabilities of both CO2 and ethanol, thanks in no small part to the MIDAS platform’s unique dual-column design. By utilizing the gentler supercritical CO2 process to first extract delicate terpenes into one column, operators can protect these fragile compounds for reinsertion into final products, and then, with valuable terpenes safely isolated, the system introduces ethanol for rapid extraction of remaining oils and cannabinoids into the second column. Each extraction cycle requires just 900–2,700 ml of the same ethanol required for post-processing, meaning that beyond quantities normally on hand, no additional solvent inventory is required.
As a consulting company, Vanguard also offers personalized solutions tailored to the unique needs of our clients. To do this, we offer end-to-end extraction solutions that go beyond just a single extraction device. We offer full equipment suites designed to create specific end products and formulations so that our clients are ready for full-scale production from day one. To achieve this, we partner with many of the top brands of extracting and laboratory equipment, including: Buchi, BR Instruments, Prospiant (formerly Delta Separations), Maratek, Atlas Copco, Thermo Fisher Scientific, Cascade Science, Agilent, Shimadzu, and many more.
This article was originally posted on www.cannabisproductsinsider.com
Looking for a reprint of this article?
From high-res PDFs to custom plaques, order your copy today!