Maintenance Strategies
PMMI: Use of Remote Services Continues to Expand
But food processors still prefer in-person support in some situations.
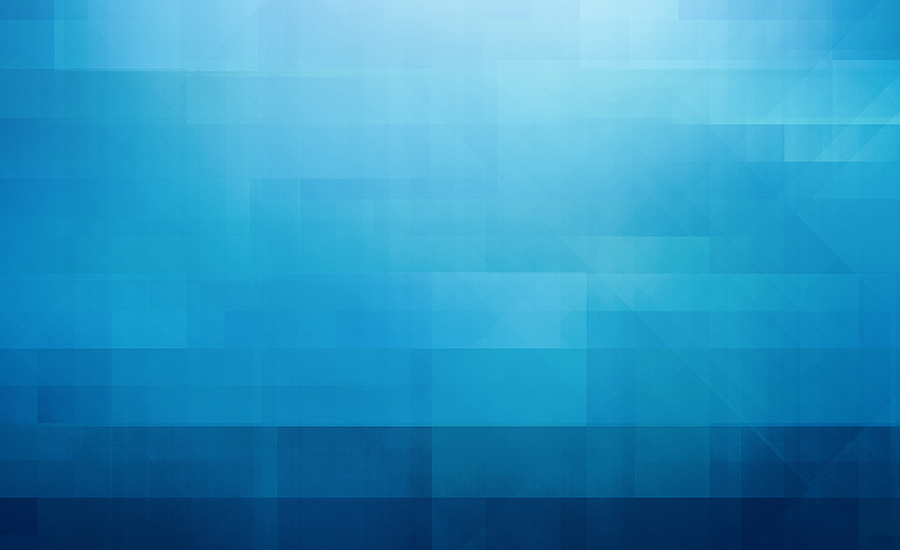
Image courtesy of Getty Images / Mammuth
A growing number of consumer packaged goods companies have adopted or plan to adopt remote services to minimize and prevent downtime, optimize operations and mitigate the impact of skills gaps in the workforce, according to Trends in Remote Services and Monitoring, a report published in January 2024 by PMMI, The Association for Packaging and Processing Technologies.
Remote services encompass remote support, remote training, remote monitoring, predictive maintenance, virtual factory acceptance tests and online commissioning. For food processors, remote support is the most-used remote service. This involves remote troubleshooting, diagnostics, and repair and often can eliminate the need for an in-person visit from an OEM technician along with related time and travel costs. The report notes that most software-based issues are already being addressed via remote support, and many mechanical failures can also be corrected remotely.
The next-most popular remote services are training, monitoring and predictive maintenance. Predictive maintenance works with remote monitoring, using digital monitoring tools to analyze and predict asset behavior so repairs can be performed proactively. This reduces downtime and product loss, the primary drivers pushing the implementation of predictive maintenance, according to another PMMI report, Challenges and Opportunities for Packaging and Processing Operations. Other benefits of adopting a predictive maintenance scheme include longer machine life and reduced parts requirements because replacements are installed as needed rather than on an arbitrary schedule.

Moving to the bottom of the remote services list, virtual factory acceptance tests and remote commissioning have experienced the slowest implementation. That’s because some food processors believe equipment can be best evaluated when staff members are physically present. Thus, although remote services—particularly for support, troubleshooting, monitoring and training—will continue to gain ground, the report concludes a hybrid remote/in-person model will remain because the advantages of an in-person presence sometimes still outweigh the time and cost savings associated with remote interactions. This is especially true for custom or complex machines.
The Trends in Remote Services and Monitoring report also delves into the factors driving investment and barriers to the use of the technologies.
[A] hybrid remote/in-person model will remain because the advantages of an in-person presence sometimes still outweigh the time and cost savings associated with remote interactions.
Why Adopt Remote Services?
The COVID-19 pandemic forced many food processors to use remote support. With travel and access to their plants curtailed for months, even the most skeptical firms discovered remote services can achieve results equal to or better than in-person interaction in many situations. Food processors learned remote services can:
- Reduce costly downtime,
- Optimize machine/operation performance, and
- Deliver a quicker response when a problem arises.
As a result, after pandemic-related restrictions on in-person visits were phased out, food processors have continued to request remote services and invest in the technology.
Food processors also realized remote services can help mitigate skill shortages. With the ongoing lack of qualified operators and technicians exacerbated by the pandemic-related retirement of many of the most experienced team members on processing and packaging lines, food processors must find a way to compensate. Remote support can help by shifting some responsibilities from in-house to OEM personnel. Remote training can support onboarding and upskilling efforts, with instructor-led online sessions viewed as the most cost-effective format.
However, it should be noted that a significant number of food processors believe that placing a live instructor next to the machine remains the most effective training option. So, training is likely to remain a hybrid remote/in-person model. Nevertheless, despite some resistance from older workers, the hybrid model could shift toward the remote side with the evolution of augmented reality (AR) and the potential the interactive experience offers to bridge the gap between remote and in-person training.
Barriers to Going Remote
Despite the benefits of remote services, adoption faces some hurdles. Barriers to implementation include:
- The cost of the service, especially when retrofitting machines,
- Limited in-house IT skills to maintain and update systems,
- The likelihood of having to deal with multiple interfaces across plants and machines, and
- Cybersecurity risks.
Although cybersecurity concerns remain high, food processors have become less reticent about granting remote access as they have learned how to strengthen their IT networks and shifted to more secure access methods. The report predicts the use of externally managed secure and converged networks will grow at the expense of cell modem access and direct virtual private networks.
Remote services capabilities and other food processing and packaging innovations will be on display at PACK EXPO International (Nov. 3–6, 2024, McCormick Place, Chicago). Ranking as the biggest packaging and processing event on the planet in 2024, the show will present 2,500 exhibitors spread across more than 1.2 million net sq. ft. of floor space and foster idea-sharing among more than 40 vertical industries. Highlights include free educational sessions, myriad networking opportunities and solutions to address automation, production efficiency, sustainability, flexibility, and e-commerce needs, as well as other hot topics and trends. For more information, visit packexpointernational.com.
Looking for a reprint of this article?
From high-res PDFs to custom plaques, order your copy today!