Remote Monitoring
Remote Monitoring Industry Trends Reveal Road to AI
How do food manufacturers move plant data cost-effectively to analytical tools and eventually to AI solutions?

Image courtesy of Getty Images / Sesame
The Trends in Remote Services and Monitoring report released in January 2024 by PMMI shows that "54% of food and beverage end users have increased their investment in remote services and monitoring since the end of COVID-19.” This isn’t surprising since remote monitoring and data acquisition have been successful for the last five years in other industries where there are distributed control strategies, like the oil and gas and water/wastewater segments.
So, can decentralized control strategies reach food and beverage manufacturers and enable more remote monitoring and data acquisition? Many analysts and suppliers believe so, but there may be a knowledge gap on retrofitting older devices with more communication abilities.
According to the 2024 PMMI remote monitoring survey, some end users are often unaware that original equipment manufacturers (OEMs) can help retrofit their existing machinery to facilitate a remote connection: “70.0% of OEMs state that they offer remote support services for both new and existing machinery, compared with 42.6% of end users utilizing remote support for new machinery only.”
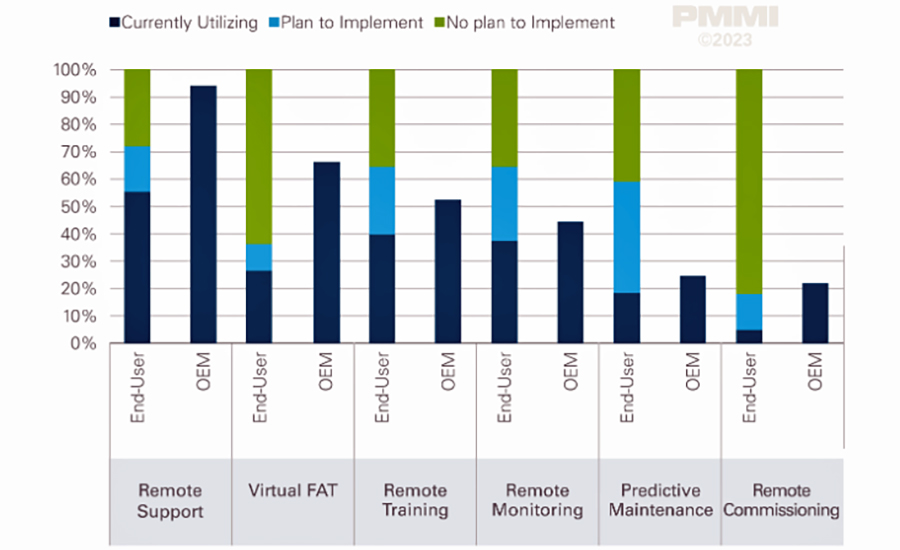
One end user from the report responded, “Our vendors aren’t informing us about retrofitting the lines to do a remote setup. Again, I’m sure there’s a cost involved with that, but I think that’s something that we may not be informed about, so maybe our vendors need to better inform us on it.”
This knowledge gap is unsurprising because industrial networking and control technology solutions are evolving rapidly, and food and beverage plant managers are juggling many balls. One such concern is the explosion of stock-keeping units (SKUs) and how to integrate machinery and industrial networking topologies to manage new formulations or packaging line extensions while not overspending on “smart” updates.
One approach is to collect data at the machine level without running wire from a wall-mounted control panel—also known as the home run wire. Industrial Ethernet wiring costs are expenses most plant managers would like to avoid. “The old way of doing things in an industrial environment, like food plants, is to have all of your control systems coming from a cabinet and running individual wires to motors and drives (on a line),” says Lucas Knapp, VP of products and market development at HARTING Americas. “Now it is all about distributed systems and modularity. This increases flexibility to re-configure the production space as needed, and reduces installation and maintenance costs.”
At HARTING Industrial Ethernet Week held in February, HARTING, Rockwell Automation and SICK experts discussed how single-pair Ethernet is a cabling solution that reduces costs and offers a decentralized approach for assets on a production line, such as motors or variable frequency drives (VFDs). Single-pair Ethernet enables the transmission of data using only one twisted pair. The solution demands less wire than a traditional twisted-pair Ethernet and shorter runs due to proximity to the motors. Currently, single-pair wire can transmit data rates ranging from 10Mb/s to 1Gb/s.
With hundreds of motors and variable frequency drives on a conveyor, Bill Martin, a business unit manager for supply of power components at Rockwell Automation, suggests networking a cluster of motors and VFDs. “We found that by networking devices, we can save a lot of control wiring with both the wire itself and the installation time,” says Martin. “We're working on a single-pair Ethernet solution right now where we can save 85% of installation wiring time.”
“If we can bring two worlds together in two cables (wires)—data transmission and power—that's beneficial for industries,” says Frank Moritz, technical industry manager at SICK AG.
This decentralized wiring setup allows plant and line managers to eliminate control wiring—reduced costs—while grabbing maintenance data from motors and drives. “Now, we can get more information from these devices instead of having a programmable logic controller (PLC) output card telling a motor to turn on,” says Martin. “We can just issue a command to say: turn on the motor.”
With SKU explosion, this decentralization approach is a prime example of how food manufacturers can keep costs lower, leverage industrial Ethernet, and move operations toward a "smarter" plant, which can eventually leverage AI platforms.
AI, Machine Learning and ‘Data Volcanoes’
A recent maintenance 2023 survey report from ABB shows that an hour of downtime for a food and beverage plant costs an astounding $84,680.56. So, a move to digital manufacturing technologies is a no-brainer, but data analytics is still a major challenge for plant managers and operators due to the amount of information produced from networked machines.
“The Internet of Things (IoT) has become ‘data volcanoes,’ and there’s so much data coming out of all of these devices,” says Knapp. “What we've experienced with our partners is condition monitoring and data understanding along the production path, instead of putting all the data into a dashboard.”
Knapp adds that the food industry has been slower to adopt predictive maintenance. The 2023 ABB survey shows that 45% of end users use time-based preventive maintenance, 21% employ a run-to-fail strategy, and only 33% have adopted condition-based predictive maintenance.
“So where we see this going is artificial intelligence (AI),” says Knapp. “AI is a buzzword, but a machine learning model can read the data and tell you what you need to do, and offer proactive maintenance steps.”
In a recent FOOD ENGINEERING AI clean-in-place case study, Markus Guerster, CEO of MontBlancAI, agreed. “Our company is unique through applying intelligence on top of a dashboard, not just having a static dashboard that shows you a couple of lines,” says Guerster. “It's not just the data that is stored somewhere, but we really go a step further, where we turn the data that exists into insights, into actionable insights.”
Remote Services in Food Manufacturing
While food manufacturers wrestle with workforce issues, management and plant operators are pushing for more experience through remote services from OEMs. PMMI’s 2024 Trends in Remote Services and Monitoring includes a respondent from a large food CPG saying, “It’s been very difficult to find qualified operators and technicians, and we have a lot of open positions, and [we have] lost a lot of skill since Covid.”
“We know our customers are struggling to find the labor they need to maintain and repair their equipment,” says Jack Grote, lifecycle leader at Grote Company. “Based on our many years in the business, we feel uniquely qualified to help our customers prevent and address any issues that may arise.”

The Grote Company family of brands, which includes PFI and Vanmark, announced a lifecycle management initiative in 2023. The initiative's purpose is to help end users stay focused on “predictive maintenance, real-time monitoring and remote health assessments.” The company employs in-house technicians to troubleshoot, service and offer food processing insights, such as operational theory and standard operating procedures, and the company even works on other equipment in the plant.
The company offers various services, including in-plant visits and smartphone and tablet troubleshooting. “We connect to their systems and sometimes have to help customers get comfortable with the idea that some information is leaving their facility,” says Grote. “It’s safe but they sometimes have cybersecurity concerns, so our job is to explain and reassure them.”
The Grote Company is part of a trend that shows “75% of OEMs surveyed in the PMMI 2024 report are increasing investment in research and development (R&D) related to remote services and monitoring.” The report mentions that 55.1% of end users qualify for remote service as remote support. And the report concludes that “those OEMs best equipped to provide a high level of remote support will be the preferred choice of end users.”
In our January edition, FE spotlighted the FIT program from the Food Processing Suppliers Association. Established in 2019, this program educates young students about food processing and packaging technician careers via hands-on technician training and learning.
“We have employed a continuous quality improvement mode for every aspect of the program, including hands-on training via donated food processing equipment to education trainers hosting field trips at manufacturing facilities,” says David Seckman, president and CEO of FPSA. “Clearly, there is a great need for trained technicians in the food industry.”
The program's upside is its focus on a younger workforce, also known as “digital natives.” Digital natives are more accustomed to an all-digital world, which easily translates to remote technology. So, while there are challenges for food manufacturers, support is improving, and technology developments like AI and lowered-cost investments should make life easier for plant managers.
Looking for a reprint of this article?
From high-res PDFs to custom plaques, order your copy today!