Laser Cleaning
Lasers Clean Fast, Precisely and Sustainably Without Detergents or Abrasives
Given the focus on productivity and sustainability in the food and beverage industry, it is time to give laser cleaning a hard look.
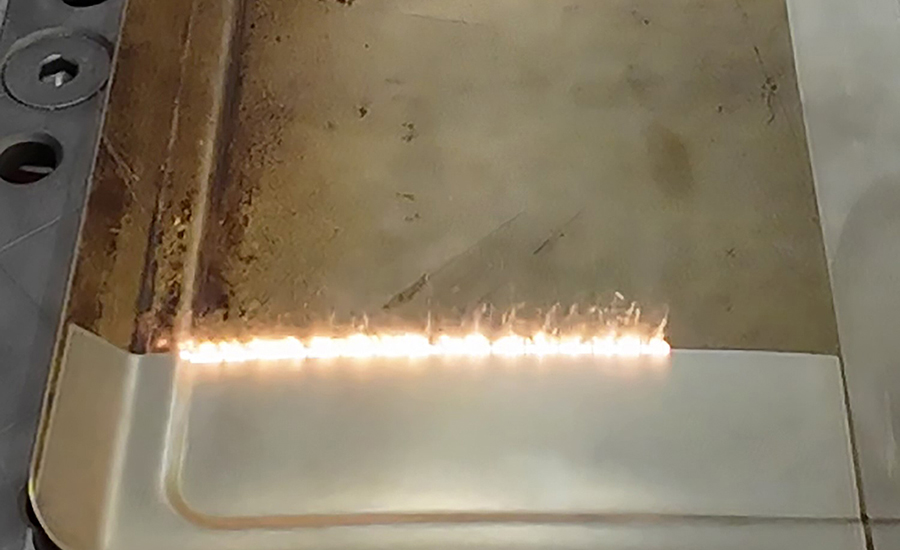
Video and all images courtesy of IPG Photonics
Laser cleaning solutions are poised to impact the food processing industry as efficient and sustainable alternatives to conventional cleaning processes. An obvious benefit of cleaning with a laser is that no consumables are required, unlike traditional cleaning methods which employ chemicals and/or abrasives. Laser energy may be directed with high precision for selective material removal, adding benefits when only portions of the workpiece require cleaning. A laser beam may be scanned at 10 m/sec, enabling extremely short process cycle times. These key benefits resulted in rapid laser cleaning adoption in many industries including automotive and aerospace. Given the focus on productivity and sustainability in the food and beverage industry, it is time to give laser cleaning a hard look.
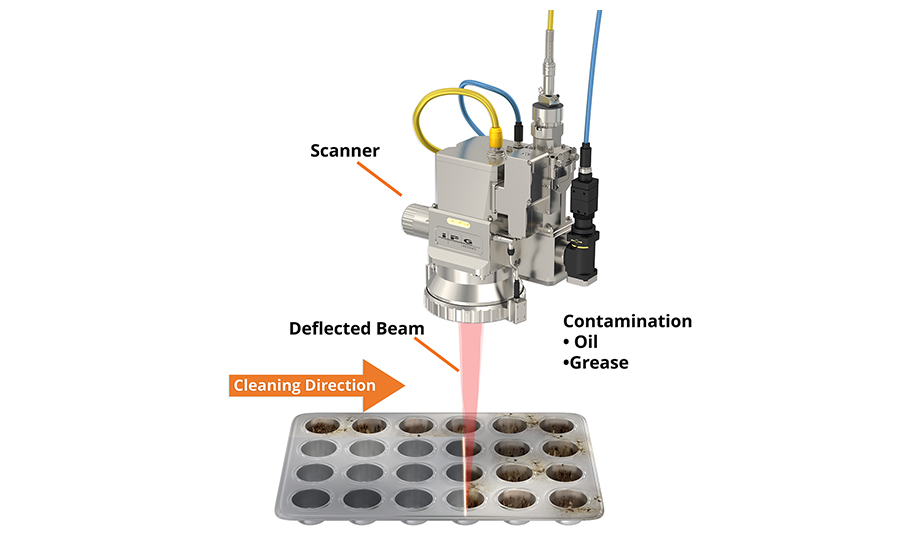
Cleaning is conducted using a nanosecond fiber laser which delivers billionth-of-a-second pulses of energy. The short duration of the pulse amplifies the laser’s impact, enabling surface material to be removed by a process called ablation. An important feature of laser ablation is that the cleaning effect is only partially thermal, so the underlying material is minimally heated—often to the benefit of total energy consumption. Because the cleaning is contactless, there is virtually no wear and tear, resulting in longer service life on parts cleaned by laser.
A sustainability benefit of laser cleaning is any material removed from the workpiece is conveniently vacuumed up and safely sequestered. No waste byproduct is created above and beyond what the laser removes. A U.S. Air Force (USAF) study noted the lack of toxic waste byproducts compared to traditional chemical or abrasive processes as a reason for the aerospace industry's rapid adoption of laser cleaning. The USAF estimates that for each 1 kg of contaminant removed, ~ 9 kg of waste is created by a wet chemical cleaning process, while 165 kg of water is consumed. Similarly, ~ 4 kg of solid waste byproduct results from grit blasting abrasive cleaning. Water conservation and waste reduction are important drivers in the food and beverage industry to move away from wet cleaning processes.

Lasers are deployed in other industries for cleaning tasks ranging from light degreasing to deep mill scale or rust removal, usually with astounding productivity gains. For lighter jobs like drying or degreasing, a metal surface the size of an 8.5-in. x 11-in. sheet of paper can be cleaned in an unimaginably short time of only 0.2 seconds. This adds up to a cleaned area of 1,200 square meters in one hour.
For tougher jobs, the laser can deliver higher energy in a single pulse to remove more material without negatively impacting productivity. A laser-cleaned surface is characterized by contact angles well below 10°, attesting to the excellent cleaning quality. The laser obliterates anything that resides on the surface it cleans, including bacteria and viruses. Customers in the food and beverage industry are strongly considering laser ablation for hygienic purposes as well.

To validate a fiber laser’s usefulness to the food and beverage industry, dirty baking sheets were subjected to a standard rust removal process. The laser stripped years of baked-on contaminants at ~50 cm2/sec, restoring the sheet’s shiny, store-bought surface. Contact angle measurements confirmed the baking sheets are clean enough to eat from.
The food industry stands to benefit from the ability of laser cleaning to be conducted in-line. It is not uncommon for a large-scale bakery operation to close every seventh day for cleaning and hygienic purposes. For example, conveyor belts and bands for baked goods could be laser cleaned after each oven pass, potentially lengthening their service life while avoiding costly downtime. Other fixtures like baking molds and pans could be cleaned within the production flow instead of accumulated and batch-cleaned. Lasers are well suited to cleaning parts which have recessed areas, provided there is a line of sight.
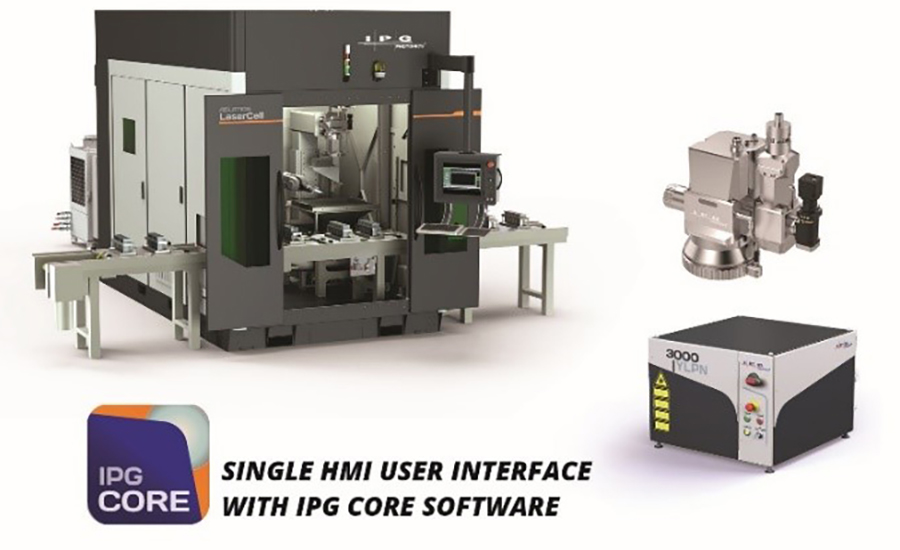
Laser cleaning is a successful, proven technology with a growing track record in diverse industries. Laser hardware is reliable, maintenance free, compact and energy efficient. The return on investment is attractive, and the sustainability arguments are obvious. The food and beverage industry will benefit by adopting laser cleaning solutions in their production processes to realize better hygiene, reduce waste, and contribute to a more sustainable future. Undoubtedly, the industry will soon seize these opportunities that have benefitted other industries.
Looking for a reprint of this article?
From high-res PDFs to custom plaques, order your copy today!