Big and Small Brewers Launch Automation Upgrades
Regional craft breweries and independents are investing in automation and plant upgrades to increase production, upgrade maintenance and move toward bigger volumes.

Sapporo Stone’s plans are to increase volume production by twofold with its existing automation and controls equipment and reach its goal of 700,000 barrels per year. Image courtesy of Sapporo Stone
The number of operating craft breweries continued to climb in 2023, reaching an all-time high of 9,761, and many of these brands are getting bigger. In late 2023, Tilray Brands, a small cannabis and craft beer company, announced it would acquire eight breweries from global beer producer Anheuser-Busch InBev.
While Tilray Brands may be an outlier, regional craft beer brands and microbreweries must respond to new product introductions like seltzers, no-alcohol and low-alcohol drinks. Regional craft breweries have been investing capital in equipment, software and digital automation technologies to increase production volume, deliver more efficient maintenance and meet modern sanitary demands.
Craft and Traditional Breweries Have Similar Goals
Even with the increase in acquisitions, regional craft breweries and global beer producers are facing two intractable trends: the need for more flexibility with processing systems for product development—like the previously mentioned seltzers, low-alcohol and no-alcohol products—and the gigantic move from bottles to cans.
Co-founder Josh Pfriem at pFriem Brewery, a legendary regional craft beer producer in Oregon, says in a recent beer industry article that competition is intense on retail store shelves due to the arrival of no-alcohol and seltzer products. “To offer more diversity of brands, grocery stores have cut into that: ‘You can use cans or you can use bottles.’ That has forced producers to assess what is selling better,” says Pfriem. “Looking at all the trends across the board, the consumer is heavily leaning toward cans.”
With these industry drivers, regional craft brewer Lakefront Brewery transitioned from bottles to cans and unified its control system at its Milwaukee plant. The brewery enlisted KHS USA’s Innofill Can C filler that can fill and seal between 10,000 and 60,000 cans per hour and accommodate a 13-ft. x 7-ft. space available at the Lakefront facility.
“Our space is quite limited,” says David Karrer, director of brewing operations at Lakefront Brewery. “That was a driving factor in our technology decision. We required a solution with a compact footprint.”
The switch to cans for Lakefront Brewery and the adoption of a high-volume, compact filler coincided with KHS moving to a Rockwell Automation control platform to add visibility into maintenance routines and rely more on production line data at the human machine interface (HMI) for operator checks. Lakefront’s previous control system and HMI platform provided input and outputs for filling levels, but the logic generated output that was not visible to operators. The bottom line was that maintenance and production line checks were time consuming.
“We wanted to eliminate the non-Rockwell Automation products and improve system visibility, usability and troubleshooting,” says Brian Anderkay, electrical engineering manager at KHS USA. “To incorporate the fill computer logic into the main controller, KHS rewrote the program from the ground up.”

Lakefront Brewery’s updated system features a Rockwell Automation platform, including an Allen-Bradley GuardLogix safety controller, Kinetix 5700 servo drives and PowerFlex 525 AC drives. The system also runs on an EtherNet/IP network and is monitored by FactoryTalk View HMI software on an Allen‑Bradley PanelView graphic terminal.
The new system at Lakefront Brewery includes a 21-valve system running at a rate of 230 to 235 cans per minute, which now matches upstream processing speed. And the new filling equipment uses vent tubes to achieve specific fill levels, while the canning technology can measure product volume using flowmeters.
“As a result, we can individually dial in every single valve to improve consistency,” says Tom Giese, plant engineer at Lakefront Brewery. The plant modernization and consolidation to one platform will also help Lakefront Brewery with maintenance. “Luckily, we haven’t had to troubleshoot yet,” adds Giese. “But I can see that troubleshooting and maintenance will be much easier since everything uses one software and control platform.”
Scaling Beer by Acquisition
Redundancy and legacy equipment can create operational complexities when acquisitions occur, but Japanese beer producer Sapporo avoided these issues when it acquired Southern California’s Stone Brewing in 2022. Sapporo bought Stone Brewing, an independent brewer headquartered in Escondido, Calif., after the regional craft beer maker added two new brewhouse processing systems in Escondido, and Richmond, Va. Both brew systems featured upgrades in its control platform and added a batch processing recipe module from Sepasoft, a manufacturing execution system (MES) developer from El Dorado Hills, Calif.
Stone Brewing added the batch processing module built on Inductive Automation’s ISA-88 Ignition software platform, which offered more flexibility in recipe management and product development. ”We looked at our system holistically and felt that there was no way to replace one component,” says Nicole Williams, Senior Dir. of Brewing Operations, Sapporo Stone Brewing, at the 2022 Ignition Community Conference. “We couldn’t just upgrade the PLCs, SCADA system or servers. It had to get to a truly modern system.”
The overhaul of these two brewhouses included Rockwell Automation Programmable Logic Controllers (PLCS), the Ignition HMI Perspective module, historian, batch and MES modules.
To enable operators’ flexibility in recipe changes, system integrator Wunderlich-Malec Engineering added the new control platform, rewrote the code and replaced the existing HMIs. The updated HMIs now allow operators to make changes to recipes and batches instead of relying on control engineers.
The control logic and HMIs are connected via Sepasoft’s Batch Procedure module, based on the International Society of Automation’s (ISA) 88 standard. “These built-in components, like the batch monitor, batch control and recipe editors, are built in (to the module),” says Fred Zaboli, principal engineer at Wunderlich-Malec Engineering. “There’s no need to write code or scripting to get to that point.”
“We love that the batch module has unlimited clients and truly drives our ability to improve,” says Williams. “Plus, it offers supervisors and brewers more time to work on recipes and gives engineers more time to make the requested improvements.”
The upgrade also included moving to an HTML-based HMI. Now, operators are able to view screens in grayscale with modern graphics, use zoom features and see the entire batch in real-time. “When operators are running a batch phase, there are numerous set points,” says Zaboli. “Those set points are tied to a specific recipe, but operators may decide to change the temperature higher or lower, and now they can do it live from the HMI.” Operators can also add custom messages for later use with this ISA-100-based HMI platform.
In addition to system flexibility, the brewer needed to address workforce issues with this change. “One of the big things about this new system is lowering training costs, and it’s so easy for new engineers to pick up (the system),” says Williams. “This ultimately lowers our external support costs since we don’t need (to call) an integrator for every little improvement.”
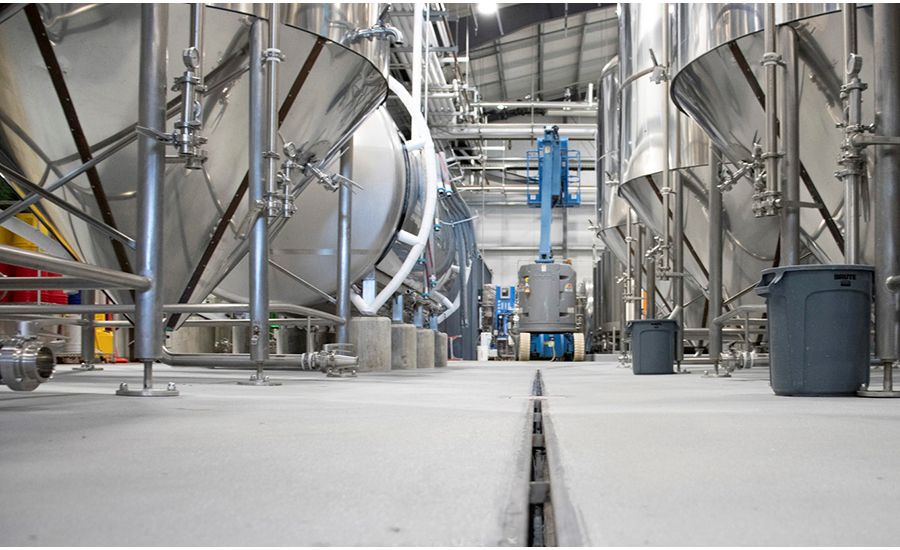
The result for Sapporo Stone was an acquisition that provided a foundation for product development and allowed the company to scale quickly. Last year, Sean Monahan, chief operating officer at Sapporo Stone Brewing, told kpbs.org that “when Sapporo was looking for a partner, they were looking for someone that could expand and brew Sapporo, but also a brand that they could help further develop.”
Fast-forward to May 2024, when the brewer announced the completion of phase one of its expansion project at the Escondido brewery, which added additional tanks and packaging lines to increase capacity and efficiency. The expansion aims to process and package the Sapporo product line in the U.S. and ultimately reach a goal of 700,000 barrels per year.
A Sanitation Focus
While increasing output and finding efficiencies are essential for the food and beverage segment, so is sanitation. Farmers Brewing Company, an independent craft brewer based in Princeton, Calif., recently upgraded its original facility with an eye on growth. After the upgrade, the independent brewer can brew and package 50,000 barrels per year in the northern California market.
Farmers Brewing added FoodSafe’s 6000 and 10,000 Series slot drain systems and avoided production stops and bottlenecks by moving away from its previous trench drain system. This investment was a critical development for an independent brewer, where resources are limited and production efficiency can be optimized with a properly designed drain system.
“With the old facility, we had a short, 10-ft. trench drain, and every time you would take those grates out, you would have all the stuff caught there,” says Bill Weller, owner and founder of Farmers Brewing Company. “With no grates, operators can drive over a slot-drain with a forklift and you don’t even know they are there.”
The slot drain system at Farmers Brewing is made of stainless steel and can manage up to 33 gal. per min./ft. Additional features include a Flush Flo cleaning system and multiple catch basins with magnetic strainer baskets. The strainer baskets allow the maintenance teams to remove debris that enters the basket and quickly eliminate waste from the slot drain.
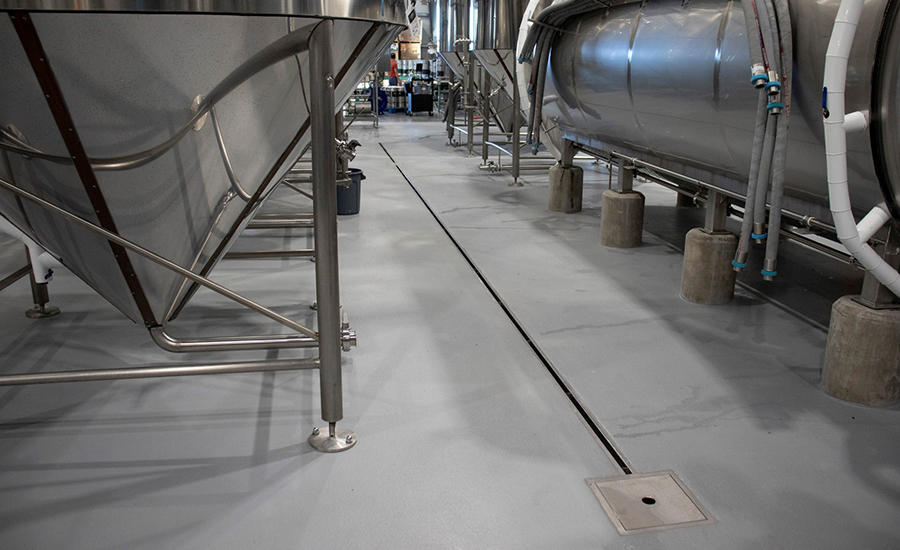
“The magnetically locked secondary strainer forces maintenance to follow cleaning routines and dump waste into garbage cans, not drains,” saiys Viking Kristjansson, VP of sales engineering at FoodSafe Drains, in a recent FOOD ENGINEERING article. “The stainless steel surface with radius edges doesn’t allow bacterial growth and permits easy disposal.”
FoodSafe Drains has been manufacturing stainless steel drain systems for more than ten years and offers customers a comprehensive approach to drain systems, which include concrete floors, drain types, underground drainage and floor coatings.
The 6000 series is intended for shallow, low-volume applications, while the 10,000 is a high-capacity, heavy-duty drain for stringent regulations. Plus, the high-capacity slot drain is load-rated for heavy-duty traffic. The Flush Flo system is connected to a water line and injects water into the slot drains by manually opening valves or on a timed basis.
“I like the added feature where we plumbed water into the high side," says Weller, “so we can rinse, turn on the water and wash everything down.”
Looking for a reprint of this article?
From high-res PDFs to custom plaques, order your copy today!