Make Maintenance Part of Your Digital Transformation Strategy
Today’s CMMS software not only keeps track of maintenance, but mobile versions with video show operators how to keep machines running.

Photo courtesy of Getty Images / Amorn-Suriyan
Here are two past personal maintenance experiences that hopefully are foreign to your MRO activities today:
High-school part-time job (second shift) running butter packaging machines in a local creamery — Depending on wrapper tensile strength, minute edge damage or uneven coating, the machine would jam and had to be stopped manually after mangled output. Sometimes the butter packaging box feeder would also jam. Finding an internal machine jam was a refined guess based on previous occurrences. Back then, there were no maintenance instructions, videos or diagrams—or clipboard notes from previous operators—other than “machine down” for one hour at 10:00 am. Since I was working off normal hours, there was no one to call.
Navy-Air Reserves, avionics tech — Radar system on patrol aircraft “inop” according to pilots. There was only one clue—a note found at the flight engineer’s position: “If radar fails to start, go below and kick the HV Variac.” Upon further checking, the motor-driven Variac had been on backorder for several months and there were none on base. Maintenance records showed lubrication was performed, but didn’t fix the problem—thus, the workorder remained open.
That was Then and This is Now
Today, most packaging machines and processing equipment are constructed with maintenance in mind. As Frank Latino, Festo product manager electric automation, suggests, OEMs often deliver equipment with an integrated computer maintenance management system (CMMS) built in, and processors can opt for maintenance service using the software—a real headstart for building maintenance into your digital transformation strategy.
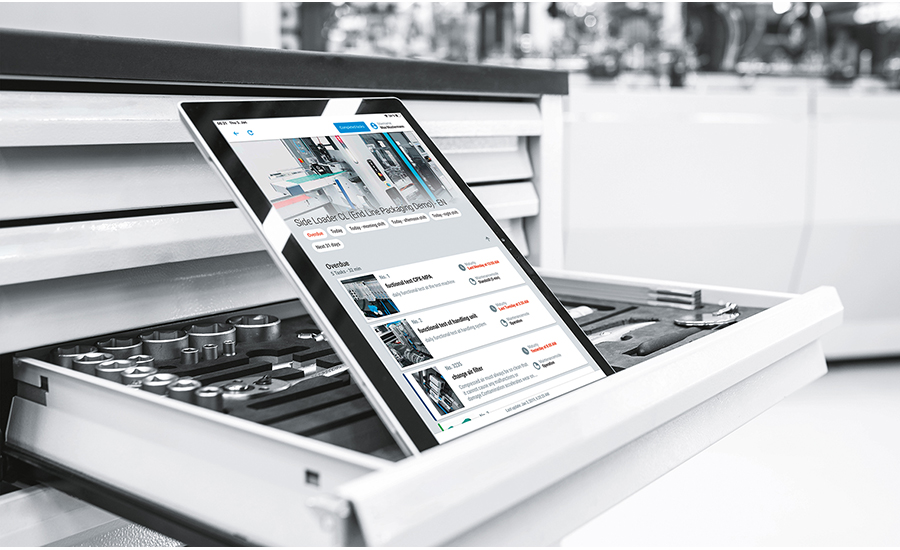
Wrapper jam? Your new packaging machine displays where the jam is on its terminal and your tablet, and shows footage on how to access it and remove the mess—even an operator can easily fix the problem. The machine records the problem and fix for the maintenance record.
The necessary sensors are built in, says Latino. “It depends on the equipment, but in many cases the sensory devices are already included in the equipment. Let’s take a pneumatic actuator for example. Often cylinder switches for extend and retract are used by the control system. A pressure sensor may also be included. This can be enough for monitoring that actuator for failure. The Festo AX Motion Insights for Pneumatics software will do this. The monitoring system will need an edge controller to run a ML/AI algorithm. To limit latency time, the edge controller will rapidly collect data from the PLC, perform analytics and send the results to where the user can consume it.”
Where the user can consume the data. Could be next to the machine on a tablet, could be elsewhere in the plant or even at home, thanks to mobile CMMS applications. Mobile CMMS applications provide the benefits I didn’t have in my two experiences above.
Mobile CMMS benefits, according to Candice Potter, enterprise account executive with eMaint, include, among others:
- Keeping maintenance teams informed
- Reducing data entry time
- Providing quick access to important documents
- Supporting a paperless environment
- Allowing completion of procedures on the go
- Tracking labor and material costs
- Eliminating costly delays
- Offering visibility to historical repairs and work orders
The eMaint mobile app also includes a robust failure analysis feature. Before completing a work order, technicians can perform a failure analysis directly within the app. It is configured to include all necessary fields and preset selections to ensure data standardization.
This feature helps pinpoint the root cause of a failure, identify patterns and recommend corrective actions, thereby improving the overall maintenance process and reducing future machine downtime, says Potter.
Built-in Tools for Predictive Maintenance
As noted, many machines include internal sensors to monitor trends in parts’ wear and tear. CMMS software connects to condition monitoring and directly to assets if desired—giving MRO teams vital asset data and the power to automate work orders based on real-time machine condition. “Fluke Reliability also offers options for condition monitoring using external wireless or online sensors and route-based data collection devices,” says Erin Sidwell, key account manager for food & beverage at eMaint.
Cybertrol Engineering is a certified member of the Control System Integrators Association (CSIA) and is also a Rockwell Automation PartnerNetwork Gold System Integrator. As such, it offers 24/7 support to manufacturers to maximize uptime. According to Lindsay Distel, marketing specialist, the integrator deploys Rockwell Automation’s advanced diagnostic and monitoring systems, such as FactoryTalk Analytics, which provides real-time insights into machine performance and health.
“Rockwell Automation’s PLEX smart manufacturing platform, particularly PLEX APM (Asset Performance Management), offers a comprehensive suite of devices and software tools tailored to assist food manufacturers and maintenance technicians in predicting equipment failures before they occur,” says Distel. These tools often include vibration, temperature and pressure sensors—and other IoT devices strategically placed throughout the production line to monitor equipment health in real time.

“A well-designed system will include documentation on how to perform preventative maintenance on it,” says Ryan Nafziger, engineer at Concept Systems, Inc., a CSIA certified member. “The first step to identifying equipment that is about to fail is to perform routine maintenance tasks to identify any physical warning signs that a piece of equipment is beginning to fail. Documentation should also include the number of operating hours between specific maintenance tasks. On a well-designed system, the HMI should indicate the number of total operating hours to allow maintenance technicians to identify the appropriate preventative maintenance task.”
E Tech Group, a CSIA certified member, employs several software techniques for predictive maintenance to ensure optimal machine performance and minimize downtime. Here are a few key strategies, says Derrick Colyer, senior business development manager:
- Motor runtime tracking: Monitor motor runtime and compare it to recommended maintenance schedules. This helps predict when routine maintenance should occur. This data is tracked in the PLC and displayed on the HMI for easy visibility.
- Output parameter trending: Any equipment with output parameters can be trended to monitor performance. For example, a conveyor running at a specific speed may typically have a consistent amperage draw. By trending the amperage draw, increases can indicate impending failure, such as the need to replace worn bearings.
- PID parameter monitoring: For operations involving filling or pumping, specific PID parameters can be set. By trending control variables while maintaining these parameters, issues with control devices can be detected. For instance, if the flow consistently takes longer to meet the setpoint, it may indicate a problem with the control system.
“These predictive maintenance techniques enable us to identify potential issues early, allowing for timely maintenance and reducing the risk of unexpected failures,” says Colyer.
While having all this data helps identify problems, Colyer suggests that digital twins of specific problem machines can be developed to improve troubleshooting significantly. These models can visually represent multiple conveyors, machines, or robots, showing their operational status with color codes (e.g., red for stopped, green for running, yellow for active warning).
“You can replay the model to see what each component was doing at the time of the problem, providing a clear visual context,” says Colyer. This tool can drastically reduce the time needed for root cause analysis from days to mere minutes.

While lots of data can be great for some users, others would just like a simple indication of what to expect with an asset. “Embedded PeakVue plus technology for vibration analysis with automated and/or periodic monitoring technologies—such as the Emerson AMS 2140, AMS Wireless Vibration Monitor, AMS Asset Monitor and AMS Machine Works—cut through the complexity of machinery health analysis by providing a simple, reliable indication of equipment health via a single trend,” says Drew Mackley, Emerson AMS Reliability sales enablement director, reliability solutions. PeakVue Plus detects impacts on critical components, like bearings and gears, and informs technicians if those impacts are a result of common issues, such as lubrication or bearing failure.
Integrating Built-In Tools with an Enterprise-wide CMMS
A good CMMS taps into machines and automation systems, giving maintenance and reliability teams access to siloed production monitoring data, says eMaint’s Potter. This provides valuable insights into asset health: temperature, water flow, pipe pressure and powerful KPIs like usage or up/downtime. In addition, work orders will auto-generate when maintenance is needed, ensuring that maintenance is performed on the right asset at the right time to prevent failures.
Not all plants have a dedicated enterprise CMMS. “Many times, enterprise resource planning (ERP) systems used by food manufacturers include some form of CMMS,” says Jerico Sanchez Hulstrand, Cybertrol engineering account manager. “However, as these are not the primary function of the ERP, they often lack functionality that the maintenance team requires. Using a dedicated CMMS built for maintenance teams is the recommended solution. Maintenance workers can get access to all the tools they need to do their job efficiently in one place, from managing and automatically scheduling work orders, keeping track of tasks, spare parts inventory, plant asset history and more. These can be integrated with an existing ERP system to more easily keep track of purchasing and accounting across various locations.”

“Integrating maintenance tools embedded in individual machines or production lines with an enterprise-wide maintenance management system, such as Rockwell Automation’s Fiix CMMS, involves a strategic approach to IT/OT convergence,” says Cybertrol’s Distel. For a food manufacturer, this integration can be achieved by leveraging Fiix’s advanced connectivity and interoperability features. Fiix facilitates the seamless transfer of data from machine-level maintenance tools to the enterprise CMMS using edge computing devices and standardized communication protocols. These technologies ensure that data from operational technology (OT) systems is collected, processed and transmitted to the information technology (IT) systems, providing a unified view of maintenance activities across the organization. Fiix’s inventory management capabilities allow for the synchronization of parts data between the machine-level tools and the ERP.
A couple of key points on integrating machines with plant-wide CMMS are important, says Concept’s Nafziger. The best way to integrate maintenance tools into a maintenance management system and to manage spare parts is to standardize on HMI layouts and part lists. Standardizing on hardware model numbers across all machines in a facility will allow for spare parts to be stocked across an enterprise in a way that allows maintenance to be performed quickly. A good place to start is identifying standard PLC, HMI and safety equipment models (relays, light curtains, Estops, etc), since these three components exist in almost all machines.
The integration approach depends on how the existing system is initially set up and how it interacts with other systems and machines, says E Tech’s Colyer. The system can be designed to include manual inputs, digital integration, or defined communications for integration, such as APIs or data feeds. An experienced integrator will know how to make these systems work together seamlessly.
Tools for On-Location Maintenance
Technology is constantly evolving, and advancements in digital solutions are transforming maintenance practices, says Colyer. “For example, augmented reality now allows us to digitally store exploded views of equipment, enabling users to dynamically select and view detailed information as needed.”
Today, we have all the data we need. “Pervasive sensing equipment (vibration, pressure, flow, temperature, etc.) can be integrated with a CMMS system, which can initiate seamless and interconnected work orders to create a closed loop workflow,” says Mackley.

And the tools are where you need them. For example, Rockwell Automation’s Fiix CMMS is a cloud-based platform that enables technicians to access real-time data, maintenance histories and digital manuals from any location using mobile devices, says Cybertrol’s Distel.
A mobile CMMS enlists multiple software services to assess plant-wide operations ranging from meter readings to barcode scans, says eMaint’s Sidwell. By and large, it offers a comprehensive overview of workflow arrangements that are accessible from the dashboard for a smooth navigation experience.
What’s better is having all the CMMS functions available offline, where technicians can create new work orders, revise existing documents and have those sync back to the network from the app, says Sidwell. The same applies to tracking and reporting tools when technicians need to look up asset histories.
Maintenance Technicians Want to do Their Job—Not Be Data Specialists
What goes on behind the scenes, supporting those mobile screens is important. Building a knowledge base of troubleshooting solutions is essential. However, if inputting data or finding information is cumbersome, the tool will not be effective, says Colyer. Ensuring the solution is digital and searchable will facilitate adoption. It’s crucial to integrate this solution into your standard procedures and enforce its proper use according to your company’s vision. Providing proper training and listening to feedback from users can help eliminate roadblocks during the design phase of a digital maintenance troubleshooting knowledge base.
Fortunately, today’s CMMSs cut the time and paperwork to describe a problem found and how it was fixed. Using a CMMS with an integrated mobile app allows technicians to use a phone or tablet to enter notes, log the use of tools and spare parts and record how much time they spent on a job, says Hulstrand. This allows technicians to quickly record the work right when it is completed without having to go back to a separate in-office system or complete a separate report.
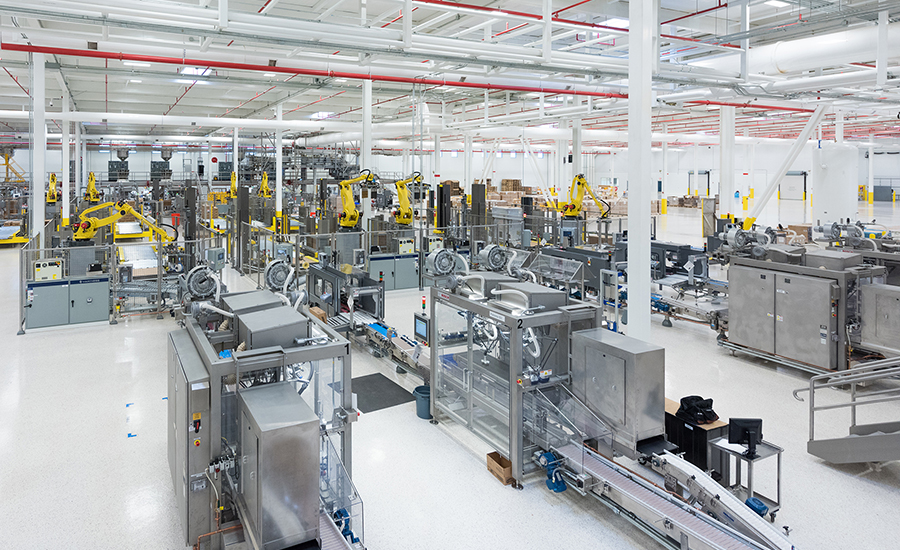
A defined list of values that users can select from a drop-down list on a form helps technicians quickly record details of the work performed without having to type in open text fields. This further speeds up the documentation process and ensures consistency in the recorded information, says Potter.
Technicians can scan barcodes to view asset or spare part details and history while walking around the facility. Additionally, all personnel, regardless of whether they are users, can scan a QR code on problematic assets to submit a work request, making the process more efficient. Technicians can also quickly add photos or videos to the work order or for each step in a procedure to document work performed. This visual documentation provides a clear and immediate understanding of the repair, making it easier for other technicians and management to review and comprehend the work done.
“Our digital solutions are dynamic and mobile-ready, incorporating familiar features like voice-to-text found in typical phone text messaging,” says Colyer. This allows users to quickly capture notes without typing everything out. Adopting a digital solution is generally easier than a manual process, especially when users see that their “reports” will make a difference and reduce future workloads.
AMS Optics manages standard operating procedures, repair procedures, schematics, manuals, how-to-guides, troubleshooting documentation and more—all available digitally and with the ability to be associated with specific assets, says Emerson’s Mackley. Users also have access to augmented reality, so when equipment needs attention technicians can use their smartphone camera and be interactively assisted at the site of the repair with supporting documentation and expert help. Technicians can even collaborate with an Emerson expert on a live video call while they’re at a control valve, motor, or other machine—for example.
Finally, for those who speak English as a second language, most CMMSs are available in several languages and have the ability to switch to the preferred language on log-in. Some systems will allow technicians to switch languages whenever they desire. Displays and use of color have been fine-tuned in today’s systems to make sense for operators. For OEMs and machine builders, the word of advice from SIs is to build in support for languages and easy-to-use displays at the initial planning stages so rework is not necessary.
Further Reading:
“Predictive maintenance, Internet of Things can lead to big maintenance savings,” FE, July, 2017
“New tools offer options for preventive maintenance,” FE, July, 2018
“Have a Strategy in Place…Or Put Out Fires, Maybe Literally,” FE November, 2023
Looking for a reprint of this article?
From high-res PDFs to custom plaques, order your copy today!