Cobots
Cobots at Home on the Plant Floor
Cobots—mobile or stationary—can fit in easily, make your facility more productive and give your employees a new lease on life.

What’s missing here? If your RTE facility operates in this fashion, maybe consider a couple of cobots to do some of the dull, repetitious work—and give employees more creative work. Image courtesy of Wayne Labs
Short on labor. Short on floor space. Short on vertical space. These issues were being faced by Magic Valley Potatoes in Paul, Idaho as the company hoped to integrate a robotic palletizing system into its facility to handle 52.5-lb. boxes of potatoes with floating, unsecured lids. This job was beyond a comfortable lift for most workers on eight-hour shifts and an impossibility for a vacuum robotic gripper to lift the entire box from the unattached lid. With the space situation, traditional palletizing robots requiring safety fencing were out of the question, but a cobot might just fill the bill.
Dean Gibson, co-owner and controller of Magic Valley Potatoes didn’t think there was a practical robotic solution. After contacting WeAssistBots, a FANUC authorized system integrator (SI), Gibson was feeling better about a solution to his palletizing problem. The SI selected a FANUC CR-35iB cobot with the ability to lift up to 35 kg and a reach of 1.831 meters. To solve the gripping problem, WeAssistBots selected two OnRobot 2FGP20 electric finger grippers, each capable of handling 20 kg. They grasp the underside of each box and lift it to the desired position on the pallet. Problem solved. Watch the video to see the cobot working in the tight space.1

What’s Driving the Need for Cobots?
In this day of increased immigration, you’d wonder why there aren’t enough people to handle the work. Yet most robot and cobot suppliers and SIs involved in installing automation say that food companies are still experiencing a lack of available labor.
“Labor shortages are a major factor. Not only are food processors finding it difficult to attract labor, but they’re also struggling to retain workers,” says Dean Elkins, senior director, robotics & vision, Gray Solutions, a CSIA (Control System Integrators Association) certified member. This makes robots and cobots essential in filling those gaps. Cobots, while not as fast or as capable of handling heavy payloads like industrial robots, are still highly dexterous and suited to specific applications like ingredient handling, palletizing and inspection. For instance, cobots can be used to handle ingredients in bags or buckets, introduce food into microwaves or inspect products for weight and size.
But the labor problem goes beyond finding and keeping employees. “Many [food] companies have expressed difficulties in finding reliable employees,” says Chris Lorente, executive director at FANUC America. “This situation highlights the significant value that both industrial and collaborative robots can offer in food and beverage applications, no matter the size of the company.”
Finding enough reliable operators to run a production line every day is difficult, says Jack Pennuto, president, KUKA Robotics USA. Add to that the increase in FDA recalls due to food contaminations, issues during manufacturing and touch points where a person can make mistakes, and robotic automation looks more and more attractive.
And, then there are market demands. “Changes in consumer behavior are leading to a rise in new sales channels beyond traditional retail, such as direct to consumer (D2C) and e-commerce,” says Roy Fraser, ABB Robotics global portfolio manager. These, in turn, are driving the need for more flexible and efficient order fulfilment and distribution infrastructures.
Food manufacturers need to transform their systems to handle both pallets and packaging destined for retail shelves while also picking and packing highly varied items for shipping direct to individual consumers, adds Fraser. This requires an infrastructure that provides maximum flexibility to handle products in the widest range of combinations and in the shortest possible time.
Relatively new food companies like Amy’s Kitchen, Sunbasket and Chef Bombay are examples of new channels for food preparation, and jobs at these companies typically involve mostly manual labor. These three food companies happen to be customers of Chef Robotics, a cobot SI.
“Chef modules” use collaborative robot arms; the “modules” take up the same footprint as one human and can be easily slid on and off a production line, says Rajat Bhageria, founder and CEO of Chef Robotics. “They have pressure and force sensors built into every joint that halt their movement if they come into contact with a human. This allows Chef to partially automate a line, thereby helping meal companies overcome their labor shortage and increase production volume. Today, Chef has deployed cobots to leading frozen and prepared food manufacturers across the U.S. and Canada.”
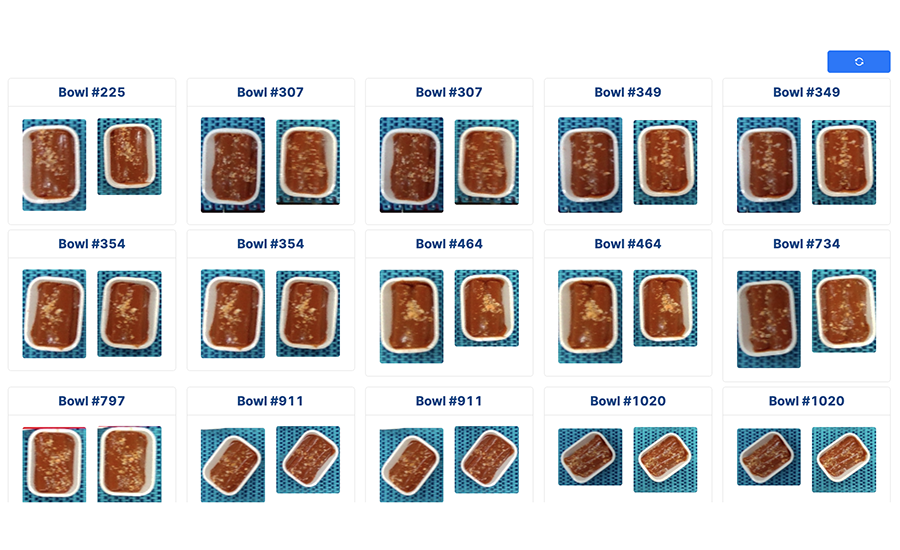
Safe Roles for Cobots and Robots
Since Universal Robots (UR) shipped the first commercially available collaborative robot in 2008, cobot adoption has been growing rapidly, representing around 10% of all robot installations by 2022, says Alexander Detsiura, global industry segment manager palletizing & packaging.
“Cobot solutions are favored in the food industry due to their compact footprint, lower cost and ability to work alongside human workers,” adds Detsiura. “They excel in high-mix, low-volume environments where traditional robots may be too rigid or expensive to justify.”
The trend toward producing smaller lots of greater mix means production workers are more frequently interfacing with robots for product and configuration changeovers to remove pallets, etc., says ABB’s Fraser. Traditional industrial robots equipped with safety-certified scanning equipment can be used in collaborative applications when higher throughput palletizing—beyond the capabilities of standard cobots—is required.

One example is ABB’s SafeMove collaborative safety software, which enables safe collaboration to be achieved without the space and cost associated with installing protective fencing or other physical barriers. Equipped with laser scanners, should the SafeMove system detect a worker within the operating area, it will automatically slow the robot or stop it completely.
“The primary advantage of cobots lies in their integration of force sensors, which detect impacts,” says Jeremy Goodrich, senior mechanical engineer at Concept Systems, a CSIA certified member. This capability enables them to operate safely in closer proximity to human operators under appropriate conditions. In collaborative settings, cobots typically operate at slower speeds compared to traditional industrial robots and must avoid any potential impact with an operator’s head. When such conditions cannot be met, area scanners or other presence-sensing devices can be employed to detect operators, allowing for the robot to slow down or enter a safe state.
Concept Systems has successfully utilized cobots to erect cases for operators in an application that lacked sufficient floor space for a traditional case erecting system, all while preserving necessary walkways and allowing for mobility during tooling changeovers, says Goodrich. In this case, the cobot’s advantage was its ability to enable operators to approach the system more closely than would be safe with a conventional industrial robot.
Palletizing and packaging are prime examples of applications where food processors have successfully implemented cobots, says Renato Osaki, product manager for collaborative robot, Omron Electronics LLC. Often, factories have limited space to automate these processes. In addition to automating repetitive tasks and providing a safer work environment, cobots offer a compact solution that occupies a smaller footprint and can be easily repositioned if the machine layout changes. Furthermore, cobots come equipped with an integrated vision system and an intuitive visualization platform, enabling operators to quickly set up multiple pallet configurations and handle various types of packaging, thereby reducing changeover times.
But, How Fast can a Cobot “Learn” a Job?
With the potential of line workers not showing up for work at the beginning of a shift, can a cobot step in and take over, for example, a “pick-and-place-in-a-carton” job at a moment’s notice? Realistically, how quickly can a cobot “learn” the worker’s job? What robot programming skills are required for a cobot? Should you fire an unreliable worker and keep the cobot?
“Equipped with intuitive interfaces, most cobots simplify the programming process, eliminating the need for advanced programming skills,” says Osaki. This accessibility enables not just engineers but also other operators to easily program and reprogram the robots. With basic training on the cobot system, operators are equipped to manage programming tasks, allowing for rapid modifications and adjustments as needed.
One notable feature of cobots is the “hand guide mode,” which simplifies task assignments. Operators can physically move the cobot’s arm to desired positions using buttons integrated into the arm, with the system automatically logging each position.
Reprogramming cobots for tasks such as switching products or adjusting to new packaging sizes can be done swiftly—typically in a few minutes to a couple of hours, depending on the task’s complexity and the operator’s proficiency with the system.
While cobots offer features that facilitate quick deployment, creating a program from scratch and teaching the cobot new tasks still requires a minimum development time and a basic level of programming skills. For advanced applications that require complex programming and integration with external systems, the expertise of an experienced engineer is essential, says Osaki.
“While it’s true that cobots are typically more cost-effective and easier to program than traditional robots, they often still require extensive integration with grippers and other hardware to create an entire application needed to complete the work task at hand,” says James Taylor, COO of OnRobot. “Also, in order to make it feasible for workers to make changes on the line to adapt to new products or packaging needs, food processors need a new approach and new technology that gives them in-house capability to make immediate line changeovers without additional integration costs and downtime. This has the additional benefit of giving full transparency on the total lifetime cost of ownership.”
Beyond basic packaging, cobots equipped with sensors and grippers can handle variable products, such as meat or baked goods, with high precision, says Taylor. “This adaptability—especially with tools that can work with any installed robot or cobot—is crucial for the future of food production where efficiency and responsiveness are key to staying competitive.”
How long does it take to set up a new cobot application? For a palletizing operation, Rocketfarm AS’ integrator companies usually spend one day to install a cobot palletizer and one day to train the staff. “Operators can then run the cobot and get help from plant engineering staff, if they need to do something completely new,” says Rocketfarm’s Martin Schøber, head of customer success.
“I believe looking at it from a ‘cobot vs. worker’ is the wrong perspective,” argues Schøber. “What we usually see is that the workforce is kept the same, but the automation helps the employees get more rewarding jobs and the plant to be able to produce more and more efficiently. The cobots are designed to work alongside people and quickly become a valued part of the workforce—because the teams can quickly see that the robot does the dirty, dull and dangerous tasks.”

Get a Grip!
“Vacuum/air grippers are the most common found in food handling today,” says ABB Robotics’ Fraser. These are excellent at dealing with variable products that are quite robust.
But, as we saw in the opening two paragraphs, standard vacuum grippers would not have worked in the potato carton application. According to OnRobot’s Taylor, the ease of deploying cobots is not without a discussion of grippers, the “hands of the robot.”
“The challenges faced by cobot grippers are largely the same as those faced by grippers placed on industrial robots, with the main difference being speed,” says Gray’s Elkins. “Because cobots operate more slowly, their throughput in handling products will be lower compared to faster industrial robots. However, the task complexity and precision needed for gripping remains consistent across both systems.”

Both cobots and traditional robots may be used in a single facility for different tasks, but there are advantages to having a consistent gripper that works with both industrial and collaborative robots, adds Taylor. Grippers that are easy to integrate with the robot/cobot arm, enabling fast changeovers, are preferred in these scenarios. The article, “Get a Grip: Robotic Grippers Help Automate the Food Industry,” goes into detail with these aspects.2
When it comes to soft, squishy or wet products, handling with a robot or a cobot can be more of a challenge and may require a different approach to the gripper, such as compliant finger or servo-controlled fingers, says Fraser.
The challenge is very similar for both types of robots, says UR’s Detsiura. The variability in food products such as size, shape, weight, texture, softness, fragility and surface conditions (food can be sticky, slippery, wet, etc.) represent a difficult situation for automatic systems as the design for a “one size fits all” is very difficult to achieve.
To add more complexity, design of gripping devices must be in balance with throughput, says Detsiura. Opening and closing, gripping and activating vacuum have to be fast enough to cope with robot motion, otherwise it will not make a lot of sense to automate a process.
“In palletizing I don’t think there’s a difference in the challenge [between using a cobot or robot],” says Rocketfarm’s Schøber. It’s about learning where the variability is and how to solve it. The solution could be adding some buffer in the software to take into consideration the variability in boxes or it could be to choose the right end-of-arm-tool. Schøber describes an example of using a specialized end-of-arm-tool to solve a specific challenge—rotating cartons to be in the correct position for stacking on pallets. Utilizing three miniPAL cobots, this fully customized-by-Columbia/Okura solution solved a production line labor shortage challenge. With a SKU scanner for sortation, a cobot gently rotates cases and works with two cobots palletizing the cases. See YouTube video.3
“For cobots, the standard is to utilize tools that are inherently safe or equipped with sensors to prevent harm, similar to the robot itself,” says Concept Systems’ Goodrich. For example, a vacuum tool can be made collaborative by simply removing sharp edges. A gripping jaw may require design modifications to limit maximum crushing force and eliminate pinch points. Items such as sharp tools or other inherently dangerous implements cannot be rendered safe merely by attaching them to a cobot; a risk assessment is necessary to determine the best strategies for hazard mitigation. Most equipment manufacturers have begun offering specific cobot tooling that meets these safety requirements, simplifying the selection process for cobot tools.
AI/ML Helps with Robotic/Cobotic Sight and Inspection
Highly variable products are now more manageable, thanks to the increasing availability of AI and machine learning-trained vision systems on the market, says Concept’s Goodrich. In applications involving complex products, both cobots and industrial robots can be effectively integrated with these vision systems. Cobots offer a distinct advantage by working closely with operators who can handle outlier products that the robots cannot manage.
AI and machine learning enhance the robot’s ability to handle variable products like bell peppers of different colors, says Gray’s Elkins. For example, robots using advanced vision systems can detect differences between red, yellow, and green peppers. AI-driven deep learning helps robots adjust their grippers to accommodate different shapes and sizes. These capabilities improve the cobot’s ability to adapt to variability in food products, although they require integrated vision systems and sometimes hyperspectral vision for more nuanced tasks.

Vision systems can be employed in both robotic vision and inspection systems, says Trent Meyers, vice president of E Tech Group Central, a CSIA certified member. “Depending on the degree of variability, a robotic solution may provide additional flexibility with end-of-arm tooling that cannot be achieved with some cobots.”
The benefit of machine learning or artificial intelligence is that machines become smarter with each use, says FANUC’s Lorente. “We can have these machines search for defects, color, size, shape, pick orientation, pick order when product is bulked together, and so on. These tools are made to improve the consistency in how we analyze and sort products.”
But is AI/ML-assisted vision better suited to cobotics or robotics? “Typically, this would be better handled by an industrial robot due to the speed that is required from the robot in certain applications,” adds Lorente. “I’ve recently seen an application using AI where the robot picked chicken from bulk. It would singulate the chicken on a parallel conveyor and then another portion of the line would leave the chicken as is or flip the chicken over so it could be uniform with the skin right side up inside the package.”
A Robot for All Seasons
While cobots are great as a possible entry point for automation, they should not be the “be all-end all” of robotic automation plans, says Kuka’s Pennuto. They need additional equipment and software to make them as flexible as posed in the questions, and will still require a safety assessment. With all that in mind, industrial robots can offer the same benefits while also being faster and more robust. As food processors go down their automation journey, they should work with qualified system integrators and put together an automation plan that incorporates cobots, industrial 6-axis arms, DELTAs, SCARAs, and any other robot that will help meet the application requirements and production goals.
References/Resources:
[1] “FANUC Cobot Allows Potato Producer to Overcome Labor Shortage,” Case Study, FANUC website.
[2] “Get a Grip: Robotic Grippers Help Automate the Food Industry,” OnRobot Website, 05-28-2020
[3] “Three cobot palletizing system,” Columbia/Okura, Video, YouTube
Looking for a reprint of this article?
From high-res PDFs to custom plaques, order your copy today!