20th Annual Packaging Trends Survey: Product Safety Remains Paramount
In Food Engineering's 20th Annual Packaging Trends Survey, the realities of life in 2005 are reflected in the fact that food and package safety is the top priority among food manufacturers, both in new package development and along packaging lines. While food safety has always been paramount, new 21st century threats such as bioterrorism and product tampering loom over the industry. As a result, food safety and the need for absolute packaging integrity have taken on an immediate importance.
To obtain a broad sense of packaging strategies for the year, a new question was added to this year's survey, asking food and beverage companies which statements reflect their planned packaging equipment and material activities for this year. In an indication of a healthier economic climate, 42 percent of those polled said they plan to increase capital expenditure projects this year, compared to 21 percent last year. Thirty-seven percent said they plan to implement new lines, 32 percent indicated they would reduce capital expenditure projects, and 18 percent said they plan to outsource projects to co-packers.
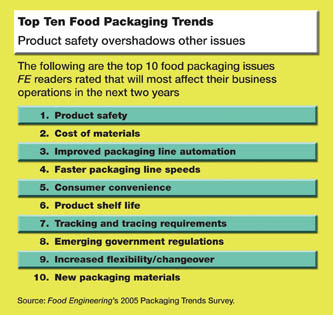
The report estimates the US contract packaging marketplace at between $17.5 and $21.5 billion, with 15 to 20 percent annual growth. Market research firm Frost & Sullivan reports contract packagers currently hold a 12 percent market share in the North American packaging market.
This need to satisfy requests for more tailored packaging has resulted in increased packaging equipment spending, as the number of FE respondents indicating they plan to spend $1 million or more on packaging equipment, doubled from last year (31 percent of respondents compared to 16 percent of respondents who said they planned on spending the same amount last year). The same positive trend is seen in packaging materials spending, as 33 percent of respondents said they plan on spending $5 million or more on packaging materials in 2005, compared to only 22 percent last year who said they would spend the same.
These findings echo the numbers in this year's Packaging Machinery Manufacturers Institute (PMMI) US Purchasing Plans Study, which predicts a seven percent growth in packaging machinery sales in the US to reach an estimated $5.91 billion. This predicted increase follows three consecutive years of growth after the economic downturn seen in 2001. According to PMMI's report, end-users' decisions to raise capital expenditure budgets in 2005 are being influenced by improved capacity utilization, increased consumer sales, higher corporate profits and favorable gross domestic product (GDP) numbers. Among the key trends PMMI's survey cites as drivers of increased packaging machinery sales are: the need to expand capacity of existing products, more product and stock keeping unit (SKU) additions, the need for more automated packaging machines to reduce labor costs and the continuing influence of super stores and major retail chains on packaging requirements.
Food product/package safety now a priority above all else
When asked to rate which issues in food packaging will most affect business operations within the next two years, product safety once again tops the list. The cost of packaging materials, improved packaging line automation, faster packaging line speeds and consumer convenience rounded out the top five.A whopping 90 percent of respondents ranked food safety as a "very important" factor in new package development, while 78 percent ranked product protection and preservation as a very important factor. Cost was the third-ranked characteristic considered in new package development.

Why is food and package safety such a high priority at the moment? "The food industry faces many more challenges today in terms of safety in food packaging than it has in previous years," comments Jeff DeLiberty, marketing manager for Silgan Containers. "Consumers are much more aware of potential risks to the food supply, not only from issues like Mad Cow disease or improperly cleaned produce, but also from tampering. This heightened awareness will continue to play a significant role in consumers' everyday shopping habits."
The Can Manufacturers Institute, which promotes the use of metal containers, a packaging method that boasts 100 percent protection from contaminants outside the container, commissioned a recent opinion research telephone survey of 1,000 Americans to determine their perceptions of food safety. The survey revealed that the potential presence of bacteria in food concerns 83 percent of Americans, while potential food product tampering worries 78 percent. The survey also found that more than three-fourths of Americans pay close attention to how a food's packaging protects them and their family from the consequences of spoilage, bacteria and/or tampering.
To thwart product tampering, potential bioterrorism threats or extortion attempts against food manufacturers, food packaging may need to move beyond traditional methods of protection such as tamper-evident bands, foil seals and tamper-evident closures. The use of color-changing dyes that indicate product tampering or damage is now being developed by Australia's Commonwealth Scientific and Industrial Research Organization (CSIRO). Dr. Andrew Scully, a scientist at Food Science Australia, recently remarked at a food industry conference that the intelligent packaging method, still in its early stages, is "based on irreversible color-changing dyes so once the package is damaged or punctured in some fashion ... it would trigger a change of color that would indicate the quality of the product has been compromised in some fashion."
CSIRO is currently studying how to use color, either as an explosion of ink on the product's wrapper or the dye's reaction to the sudden influx of moisture from the outside, to signal tampering.
RFID still in its early stages
FE's Packaging Trends Survey included some questions regarding radio frequency identification (RFID) tag trials. While the January 2005 deadline related to RFID tagging mandated by Wal-Mart has passed, the technology has yet to be widely applied in an automated fashion. Nearly three-quarters of those surveyed (72 percent) said their company has not yet conducted trials involving RFID tags on pallets, cases or other packaging materials. Of the 28 percent who said their company has conducted RFID trials, the main issue encountered was tag cost and/or availability, followed by readability rates and the proper recording at the customer's receiving point.
Among the verbatim responses, FE readers cited cost, software issues and updating computer systems to accommodate RFID technologies as obstacles. A number of respondents said their company was in the midst of testing and evaluating the technology. One respondent said they are "looking for improved RFID longevity," while another said his company will apply RFID technologies "when Wal-Mart decides we have to do this."
Push for more flexibility
The need for food manufacturers to achieve greater flexibility in packaging to meet retailers' demands for increases in varieties of products, product sizes and package configurations has, in turn, led to a need for more automation and customization along packaging lines. When survey respondents were asked what specific improvements they would like to add to their company's packaging line, increased automation and flexibility were listed several times. "Automated case bag packing and palletizing," "automated quality inspection" and "increased automation and decreased changeover time," were three of the verbatim responses. A trained workforce that can properly operate these automated packaging lines is also needed. "Workforce properly trained to maintain new automation and technology" was an area in need of improvement at one respondent's company.Another respondent said the "variety of products plus the need for a variety [of] types of packs" is an area of improvement needed along the packaging line, while another said his company "ships on a customer-by-customer customized basis, [so the] inventory of packing material and cost [are] always important."
Among the new packaging materials or technologies that have been implemented within the past year, automation along the packaging line was again mentioned in many responses. Modified atmosphere packaging, retort plastic containers and "sleeker packaging and closeability" were listed, among other packaging techniques implemented at food manufacturers' sites.
About this survey
The purpose of Food Engineering's Packaging Trends Survey is to evaluate industry professionals' attitudes and opinions of current and future food packaging trends. This year, 1,000 questionnaires were mailed to readers with packaging-related responsibilities; an additional 2,500 subscribers were surveyed via phone interviews. Including mail and phone surveys, there were 250 total usable returns. The majority of respondents hold positions in operations/production management, general administration/management and engineering. A breakdown of the response group's food product involvement included 28 percent meat/poultry/seafood, 25 percent dairy, 22 percent beverages, 20 percent bakery and 18 percent grain-based products. (Multiple responses allowed.)Looking for a reprint of this article?
From high-res PDFs to custom plaques, order your copy today!