Bridging the IT/Engineering Gap
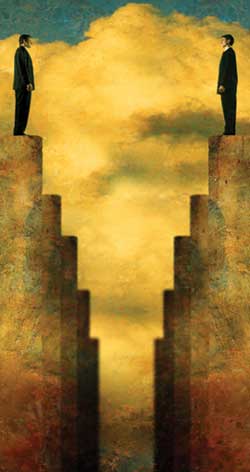
Sometimes the relationship between information technology and engineering is like oil and water. Each side might bring its own agenda to a project, oblivious to the needs and concerns of the other. Automation projects, which should make life easier for both, end up satisfying neither.
The days of turf wars are drawing to an end, however. An armistice has been declared, and it’s signed by advocates of supply chain integration. Food and beverage processors need to get closer to their customers and suppliers, and those relationships hinge on accurate data derived from the production floors. If businesses expect to have collaborative relationships with their customers, they first must have collaborative relationships within their own organizations, beginning with IT and engineering/operations.
“Food plants need to comply to the supply-chain demands being put on organizations so that they can deliver product to customers on time and get back detailed information to plan production as efficiently as possible,” notes Henrik Bilgren, vice president and cofounder of Intentia Americas, the Schaumburg, Ill.-based arm of a Swedish provider of enterprise resource planning software. “Manufacturers need supply-chain visibility if they are to survive.”
The attention and energy directed toward improved supply chain collaboration with customers and more accurate key performance indicators (KPIs) for management is wasted if plant operations can’t accurately and efficiently collect the data that underpins it. Kerrygold, a UK dairy ingredient supplier that implemented Intentia’s Movex collaborative enterprise suite, did so to ease pressures its retail customers faced in a changing market. To deliver on its promise, the system relied on the data moving up from the plant floor. “The system is only as good as the information that goes into it,” notes Carl Ravenhall, Kerrygold’s operations director. “So we ran a major education program to stress the need for accurate data entry at every stage.”
In essence, the operations side is being told to kiss and make up with IT. Absent the cultural change this might entail, the survival of the organization is in doubt, some suggest. Business as usual is not an option.
“If you’re going to have a successful collaboration, you need good leadership that is secure in its position and is interested in getting the job done instead of fiefdom building,” says Jeff Cawley, vice president of Northwest Analytical Inc. (NWA) in Portland, Ore. “The group dynamic is very important, and a lot of that depends on how management rewards people and whether there is a vision of where the company wants to go and the time it takes to get there. Do you have an environment that rewards collaboration or promotes competition for resources?”
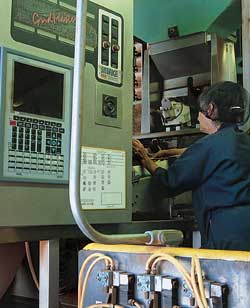
People-first approach
IT-engineering collaboration had two legs up at Blue Diamond Growers when the California almond processor embarked on an automated statistical process control (SPC) project: it was a next-step evolution of automation efforts that began 10 years earlier, and the senior programmer had extensive PLC and database programming experience on the plant floor before migrating to the IT department. The system became operational three years ago.Both Senior Programmer Kurt Huebner and Senior Industrial Engineer Bob Hitomi arrived at the Sacramento, Calif.-based cooperative in 1985, moving up the organizational ladder since. Statistical control efforts began soon after, first as a vendor certification requirement and then as an analytical tool in the QC lab. Handwritten notations from line workers eventually became part of the QA data. Moving to an automated system that integrated the plants’ Wonderware industrial SQL server and the Quality Analyst SPC package from NWA was a logical, albeit ambitious, extension of the earlier projects.
“Because Kurt came out of the plant, we had a very close relationship early on,” reflects Hitomi. “We’ve extended that bridge quite a bit, though, not only to IT but everyone else in the organization. And because of Kurt’s familiarity with the issues of production, they started working on project aspects that users actually needed.”
Project leaders were extremely sensitive to line operators’ needs. The system of data entry and control-chart generation was designed for minimal intrusiveness and disruption. The HMI screen emulated the notepads workers previously used to record variables. “To make everything work together seamlessly took quite a lot of programming,” notes Huebner. The payoff has been development of a database with 13 million test records and counting.
The accuracy of the data allows Blue Diamond management to view KPIs based on actual batch yields on the plant floor. For line workers, variations in their yield compared to lines running comparable products can prompt an investigation into the cause. Dwell times and temperature settings in blanchers and ovens can be based on historical results from comparable raw materials.
“There’s no way an operator is going to remember how a given product ran on his line six months or a year ago,” Hitomi points out. “Even on frequently run products, they can see if yields are changing and make any necessary adjustments.”
A fundamental issue every organization confronts is whether technology or people drive the project. When needs change or technology fails to deliver as expected, the Blue Diamond team has consistently adapted the system to the people. Creation of a data network took two false starts before a structure that could handle the plants’ multi-user and data-volume needs was implemented. Similarly, an attempt to arm line workers with PDAs or tablet PCs was scrubbed because the hardware’s convenience was offset by the cumbersome data entry and control-chart viewing it would require.
“We had an idea of where we wanted to go before the project started,” Huebner says, “but needs changed, the technical way of doing certain things changed over time.” Rather than stay the original course, project managers made the technology serve personnel needs, not the other way around.
While the project represented a technological achievement, the human side of the implementation ensured that accurate data is captured and recorded. “The old rules about implementing very identifiable, doable projects are sometimes overlooked, but that is absolutely imperative,” points out NWA’s Cawley. “If you don’t, you’re ignoring the whole sociology of the plant.”
The same holds true of enterprise systems. “A slaughterhouse has very different scheduling demands than a dairy or a brewery, and an ERP system must take into account the specifics of the plant involved,” says Intentia’s Bilgren. “If it doesn’t, you end up with just another complex tool that isn’t used.”
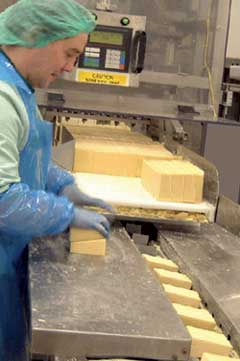
The virtue of patience
With the investment community’s focus on quarterly profits, publicly held food companies face a difficult hurdle in planning, executing and receiving a return on investment from collaborative manufacturing projects like Blue Diamond’s. “I applaud public companies that can commit to three-year projects, and that’s what we’re talking about,” says NWA’s Cawley. “If they think they’re going to accomplish it in three months, they’re kidding themselves.” Privately held companies enjoy an advantage, in this regard. In food manufacturing, that describes the majority of the companies, including firms like Barber Foods.Improved yield is the goal for a manufacturing execution system being implemented at Barber Foods, a value-added poultry processor in Portland, Maine, that serves foodservice, retail and club-store accounts. Variances in yield and labor costs for a given order were unknown, so those cost differentials had to be allocated across the board. Whether the plant made or lost money on a customer’s order wasn’t known until weeks later, if ever.
After helping implement a global shop-floor management system at General Electric, Bob Lowe joined Barber a year ago as vice president of MIS. Ownership wanted to replace an existing ERP system to improve visibility to the shop floor, but Lowe recommended implementing MES first. “I suggested delaying putting in a new ERP before putting in a shop floor system first so we could address the issues of yield variance and integration of our labor accounting system first,” he recalls.
Fortunately, the head of manufacturing, who came to Barber from Kraft Foods, also recognized the need for greater visibility to the process. “He was going to put in a system requiring a lot of manual-input metrics, and when I proposed an MES system instead, he was very supportive,” says Lowe. The company selected the Factelligence package from Cimnet Inc., then retained Interwave Technology Inc. to resolve the interface issues in collecting data from the floor.
The firm’s former director of manufacturing was appointed project leader, a critical factor in the implementation’s success. “In my experience, operational involvement is the factor that distinguishes projects that succeed from those that don’t,” says Lowe. “Operations had to lead, not IT. We also limited the scope of the project, rather than implementing all the modules at once. Keeping the scope down was critical.”
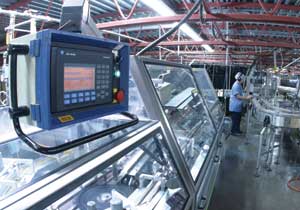
With manufacturing heading up the project, the difficulties of data entry in a cold-room environment were addressed. Bar-code scanners are used wherever possible, and point-and-click data entry replaces key entry in other instances. Line workers are constantly being redeployed, and a simple method for logging those changes was essential. “Based on the standards in their ERP system, they now know before the end of the shift if they made money or lost money,” Cudemo says.
About 80 percent of Barber’s customer transactions are executed through EDI. The MES system being implemented and the ERP upgrade that will follow should improve the data flow between Barber and its customers.
“Better labor utilization alone will give us a one-year payback,” calculates Lowe. Yield improvements will be an even greater benefit, however. Products like cordon bleu include cheese and ham, costly ingredients that have a huge impact on profitability. “ Now we have a way to track waste and address any problems we’re having,” he says.
The importance of capturing reliable data on the plant floor was dramatized at Leahy Orchards, Canada’s leading processor of applesauce, when the company installed PlantMetrics software at its Montreal area facility. PlantMetrics is a tool for monitoring operational equipment efficiency (OEE), and the first problem encountered on the road to increased efficiency was a counting problem in work cells.
Final production numbers were inaccurate because part counts on the portion line did not match from one cell to another. Systems engineer Gerald Beaudoin discovered the counting mechanism on one work cell was recording higher numbers of finished product than was true because it was including unfinished pieces that were scrapped. The next work cell wasn’t counting the scrap pieces, so both production and scrap reports were off. Remedying the mechanism failure helped Leahy take steps to cut scrap in half, a $500 a day savings.
“The software allowed us to identify the root cause of inefficiencies on the line that otherwise would have gone unnoticed,” says Beaudoin. “Just looking at the numbers in some cases didn’t show us the problem, but looking at the line did.”
Although PlantMetrics is an out-of-the-box solution from Rockwell Automation’s RSBizWare package, collaboration with IT still is important, according to Rockwell’s Don Lazare. “The engineers want the OEE information, but the data that the software pulls out also go to IT, which then pushes out reports on cycle time, batch counts, piece counts and other information that the rest of the company wants to track,” Lazare says. “IT also typically maintains Web content. In the case of Leahy’s, the information now is more accurate and as fresh as it possibly can be.”
Improved visibility to the manufacturing process is the goal up and down the organization, from plant-floor systems for OEE and SPC to management tools such as MES and ERP. “You can’t improve what you can’t see,” notes Interwave’s Cudemo, repeating an old maxim that is no less true today. The business environment is changing, and the manufacturing and IT teams have to hang together or hang alone.
Looking for a reprint of this article?
From high-res PDFs to custom plaques, order your copy today!