9th Annual Essential Guide to Manufacturing Software
Food
manufacturers want reliable, all inclusive software that does it all at an
affordable price.
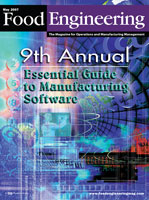
Some food processors make products with little or no process
automation yet need to manage inventories, supply chains and customers because
of complex product mix and distribution. Other processors require stringent
automated process control and also need to manage the business. Yet other
processors have special needs that must be customized to their operation.
Chances are, the software required to manage a process, packaging line or the
business is out there. The challenge is finding the software that best matches
your needs.
From no-cost, open source process control systems (www.proview.se), relatively inexpensive open source-based historians (www.sjsoft.com) and ERP programs (www.openmfg.com) to Windows-based process control, visualization and high-end ERP programs such as SAP’s R/3, there is a software system that can meet your budget and expectations. To get an idea of the many suppliers and their products, see the manufacturing software suppliers’ table, on pages 38-43.
For many food processors, changing lifestyles have helped them grow at a rapid pace. According to Rory Granros, Infor director of industry and product marketing for the process industries, “The shift in consumer consumption and lifestyle requires food processors to develop convenience products that can be consumed on the run or minimize the time to develop a meal.” More than 50% of consumables are expected to be purchased from non-traditional outlets within five years-a drastic change from the early ‘90s when 90% of consumables were purchased in supermarkets.
Harry’s Fresh Foods of Portland, OR is such an example. Purveyor of “always fresh-never frozen” soups, gravies, puddings and entrées, Harry’s has grown at an annual rate of 20%, says Jenny Fancher, Harry’s business system analyst. While Microsoft Excel was once adequate to handle the business, Harry’s quickly grew out of it and found itself in the market for an ERP system. While all its products are hand-made, more than a thousand recipes, distribution in the US (including Hawaii and Alaska) and Mexico, and Web-based sales made scheduling rather tricky for products with a shelf-life of 60 to 120 days. In addition, two filling machines with different rates created a bottleneck that slowed production. According to Fancher, IFS North America was chosen for its ERP software because it offered constraint-based scheduling for the two fillers as well as distribution, planning, master scheduling, financials and receiving modules. For this 200-250 employee operation’s first ERP implementation, IFS provided a reasonably-priced solution that also solved filler scheduling.
Cedarlane Natural Foods Inc., was also facing a growth problem. For nearly 25 years it produced high quality, all natural fresh and frozen foods. With the addition of the Dr. Sears Zone brand, it was time to move away from its manual business practices and old green screen invoicing system. Reconciling invoices with deliveries and retrieving data for reports and audits were especially time consuming. With budget in mind, Daniel Baroco, Cedarlane IT manager, looked at ERP products from six different vendors. “OpenMFG,” says Baroco, “was the only vendor that didn’t require thousands of dollars for implementation upfront. All we had to do was purchase the open source based-software and several licenses and see how we liked it.” When Baroco began shopping for a system, 64-bit Windows servers were not yet available, so he settled on a Linux server and Linux clients. He figures he saved $50,000 on servers and the Linux OS alone. Over a three-year period, Baraco has increased licenses from a pilot system with five seats to a total of 30 seats.
Cedarlane has used OpenMfg modules to streamline operations in accounting, inventory, manufacturing and distribution. Not only has the system brought together these functions, it has also changed company culture and created new procedures. “We didn’t have an inventory control group before,” says Baraco, “but now we can do everything in a more organized way.” The ERP system includes track and trace in its manufacturing costing module and uses a SQL database with an ODBC (open database connectivity) connector to be fully compatible with Windows-based systems. When Cedarlane required EDI, OpenMfg provided a flexible solution. Today the system generates about 5,000 EDI invoices per week.
Simplifying database technology and using ODBC to connect to its worldship shipping system, Chocolate Potpourri eliminated several disparate database systems and replaced it with SYSPRO’s e.net ERP solution. According to Chocolate Potpourri’s President Richard Gordon, the single SYSPRO integrated real-time database eliminated manual entry on several systems and reduced the amount of paperwork. In addition, the services-oriented architecture (SOA) allows the small company to compete on an equal footing with much larger competitors.
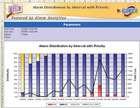
According to Brandon Henning, GE Fanuc Automation, food and beverage industry leader, processors should use track and trace to discover a process failure or omission before bad product gets out the door, not to hunt it all down after it’s entered the marketplace and ruined the brand name. Henning points to the recent peanut butter recall (now extended back to 2004), suggesting that the bad product was caused by an internal or process failure, not incoming raw materials. With proper visualization systems in place, insufficient process temperatures or pressures, improper cleaning and sanitizing or missed steps would have been spotted before bad product was distributed. “Avoiding the recall altogether is the real money saver,” says Henning. “Even a short recall for a couple of days is still a brand killer.”
When asked what software is particularly valuable in tracking key process variables, Gerald Beaudoin, automation coordinator at Leahy Orchards suggests data collection software on the shop floor. OEE (overall equipment effectiveness) and historians make a big difference in keeping the operation at peak performance. Beaudoin, however, doesn’t think it’s possible to have too many data points. “I don’t think there is a single point that we’ve put on where we haven’t had a big ‘a-ha’ moment, where [new] information jumps out. You put the point on with the intention of looking at temperature, but you find new relationships not seen before.”
OEE is a topic that’s popular these days. However, according to Claus Abildgren, Wonderware marketing program manager, OEE is best applied in conjunction with other tools, just as Beaudoin is doing. Abildgren says that OEE is one key and established metric to understand how well manufacturing is working and what the state of resources is. If the processor doesn’t have the discipline to look at OEE data and take action, warns Abildgren, then OEE alone won’t be sufficient to improve operations. Other tools such as statistical process control (SPC) and enterprise asset management (EAM) also can be applied. EAM improves asset performance by managing maintenance schedules to prevent a breakdown in the manufacturing cycle that can cause expensive delays.
Another tool that can reveal what’s happening with plant operations is enterprise manufacturing intelligence (EMI), perhaps an evolutionary step from plant information management systems (PIMS). EMI solutions combine real-time operational information, business intelligence and rich performance metrics. Enterprises that have implemented ERP, supply chain planning or advanced planning solutions will be able to use real-time data from an EMI program to provide real-time capacity information, allowing planning systems to be more accurate. Cargill Salt recently implemented an Informance EMI system to accelerate its manufacturing performance. Using this EMI, Cargill Salt quickly identified and prioritized production improvement opportunities to increase sprint capacity during peak production seasons. According to Jim Heard, assistant vice president of the Cargil Salt business unit, “We can now quickly identify opportunities for improving efficiency at our manufacturing facilities. This is helping us reduce operating costs and improve production.”
Most Windows-based applications today are being built upon .NET, as this has been the evolutionary outcome of earlier Microsoft developers’ packages. According to Allpax Director of Software Engineering Jonny Watkins, “Microsoft forces its users to upgrade at some point. The same happens with development platforms. If developers aren’t looking into .NET by now, they’re sticking their collective heads in the sand.”
According to Jay Deakins, president of Deacom Inc., because its Accounting & ERP system is written entirely in .NET, users can access the system from any remote location. .NET also allows various software applications to be readily connected. Another plus for .NET, says CSB-System International President and CEO Patrick Pilz, is .NET’s support for portable Windows devices such as Windows Mobile Smartphones and handheld computers within the plant.
Not everyone, however, is sold on .NET, especially those providers traditionally based on non-Microsoft platforms. Sterling Commerce, according to its Product Marketing Manager Peter Wharton, chose JSP (Java Server Pages) instead of .NET technology for a number of reasons, including its ability to scale to meet the transactional volumes required by its customers. For access to its solutions, the applications use authentication based on the J2EE Authentication and Authorization standard, where user rights and permissions are role-based to allow specific access to functionality needed by the user.
Bob Carver, VP of logistics software at HK Systems, doesn’t see any urgency to using .NET. He still supports a fair number of UNIX installations, and his company is not as tied to Windows at this time. Based primarily in Oracle technology, HK Systems is working with .NET, but migration is still five to seven years away.
Rather than pit one of these technologies against the other, processors should make sure that the suppliers they select are conversant in both platforms. And today, the tools are there to connect the Java camp to the Microsoft world. As Fraser points out, there are probably just as many J2EE proponents as there are .NET and each has its advantages and disadvantages. SAP is one of the providers that has done a lot of work in bringing the two together.
According to Johann Heydenrych, director of industry solutions at itelligence, processors that have good open application frameworks in place will be able to bring a multitude of applications together and drive push concepts via portals, ensure single sign-on and authentication and provide ease of use. He, too, commends SAP as having a leading position in this regard through its Netweaver platform.
While the concept of renting a major software application from an ASP has a long way to go with most processors, some applications (e.g., supply chain) may lend themselves better to the model. For sure, most processors still want to see their server within the confines of their facility and their clients hooked to it via internal networks. But in support of the ASP model, Wharton says, “The way the software is delivered is really what the game is all about. Being able to deliver in an on-demand environment is changing the way people think about supply chain software. As on-demand software is leased and hosted in another location, there is no software or hardware to buy and manage. Upgrades are delivered to every user at the same time, so every user has the latest capabilities.”
What do processors want from their software? Gold sums it up: “Manufacturers want reliable, all inclusive software-one that does it all or comes close.”
View the Software Guide
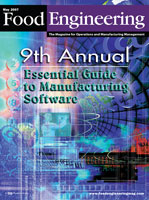

Today’s
HMI screens can feature simple controls plus provide information about the
process as well. Source: FMC FoodTech.
From no-cost, open source process control systems (www.proview.se), relatively inexpensive open source-based historians (www.sjsoft.com) and ERP programs (www.openmfg.com) to Windows-based process control, visualization and high-end ERP programs such as SAP’s R/3, there is a software system that can meet your budget and expectations. To get an idea of the many suppliers and their products, see the manufacturing software suppliers’ table, on pages 38-43.
For many food processors, changing lifestyles have helped them grow at a rapid pace. According to Rory Granros, Infor director of industry and product marketing for the process industries, “The shift in consumer consumption and lifestyle requires food processors to develop convenience products that can be consumed on the run or minimize the time to develop a meal.” More than 50% of consumables are expected to be purchased from non-traditional outlets within five years-a drastic change from the early ‘90s when 90% of consumables were purchased in supermarkets.
Harry’s Fresh Foods of Portland, OR is such an example. Purveyor of “always fresh-never frozen” soups, gravies, puddings and entrées, Harry’s has grown at an annual rate of 20%, says Jenny Fancher, Harry’s business system analyst. While Microsoft Excel was once adequate to handle the business, Harry’s quickly grew out of it and found itself in the market for an ERP system. While all its products are hand-made, more than a thousand recipes, distribution in the US (including Hawaii and Alaska) and Mexico, and Web-based sales made scheduling rather tricky for products with a shelf-life of 60 to 120 days. In addition, two filling machines with different rates created a bottleneck that slowed production. According to Fancher, IFS North America was chosen for its ERP software because it offered constraint-based scheduling for the two fillers as well as distribution, planning, master scheduling, financials and receiving modules. For this 200-250 employee operation’s first ERP implementation, IFS provided a reasonably-priced solution that also solved filler scheduling.
Cedarlane Natural Foods Inc., was also facing a growth problem. For nearly 25 years it produced high quality, all natural fresh and frozen foods. With the addition of the Dr. Sears Zone brand, it was time to move away from its manual business practices and old green screen invoicing system. Reconciling invoices with deliveries and retrieving data for reports and audits were especially time consuming. With budget in mind, Daniel Baroco, Cedarlane IT manager, looked at ERP products from six different vendors. “OpenMFG,” says Baroco, “was the only vendor that didn’t require thousands of dollars for implementation upfront. All we had to do was purchase the open source based-software and several licenses and see how we liked it.” When Baroco began shopping for a system, 64-bit Windows servers were not yet available, so he settled on a Linux server and Linux clients. He figures he saved $50,000 on servers and the Linux OS alone. Over a three-year period, Baraco has increased licenses from a pilot system with five seats to a total of 30 seats.
Cedarlane has used OpenMfg modules to streamline operations in accounting, inventory, manufacturing and distribution. Not only has the system brought together these functions, it has also changed company culture and created new procedures. “We didn’t have an inventory control group before,” says Baraco, “but now we can do everything in a more organized way.” The ERP system includes track and trace in its manufacturing costing module and uses a SQL database with an ODBC (open database connectivity) connector to be fully compatible with Windows-based systems. When Cedarlane required EDI, OpenMfg provided a flexible solution. Today the system generates about 5,000 EDI invoices per week.
Simplifying database technology and using ODBC to connect to its worldship shipping system, Chocolate Potpourri eliminated several disparate database systems and replaced it with SYSPRO’s e.net ERP solution. According to Chocolate Potpourri’s President Richard Gordon, the single SYSPRO integrated real-time database eliminated manual entry on several systems and reduced the amount of paperwork. In addition, the services-oriented architecture (SOA) allows the small company to compete on an equal footing with much larger competitors.
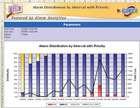
Today’s
.NET enabled software allows engineers to check alarm status from any remote
location. This screen shows alarm distribution by interval with priority.
Source: Iconics.
What's hot
Processors want to get the most output with the least amount of waste while being able to track and trace every product-from ingredients to distribution channels. But reducing waste and track and trace are not mutually exclusive. According to Rockwell Automation Business Development Manager Don Fraser, “Track and trace works for regulatory reasons, but track and trace is more about plant-wide waste and use of raw materials.” Plant operations knows what quantities of ingredients came in, and they know how much product was made. Track and trace can help operations determine where the plant is losing materials and which process may be at fault. Track and trace can also let supervisors know what programming changes the plant manager made with his laptop to the supervisory packaging line PLC at 1:00 a.m. when the process seemed to need a “little tuning,” but now is a little off kilter during the day shift.According to Brandon Henning, GE Fanuc Automation, food and beverage industry leader, processors should use track and trace to discover a process failure or omission before bad product gets out the door, not to hunt it all down after it’s entered the marketplace and ruined the brand name. Henning points to the recent peanut butter recall (now extended back to 2004), suggesting that the bad product was caused by an internal or process failure, not incoming raw materials. With proper visualization systems in place, insufficient process temperatures or pressures, improper cleaning and sanitizing or missed steps would have been spotted before bad product was distributed. “Avoiding the recall altogether is the real money saver,” says Henning. “Even a short recall for a couple of days is still a brand killer.”
When asked what software is particularly valuable in tracking key process variables, Gerald Beaudoin, automation coordinator at Leahy Orchards suggests data collection software on the shop floor. OEE (overall equipment effectiveness) and historians make a big difference in keeping the operation at peak performance. Beaudoin, however, doesn’t think it’s possible to have too many data points. “I don’t think there is a single point that we’ve put on where we haven’t had a big ‘a-ha’ moment, where [new] information jumps out. You put the point on with the intention of looking at temperature, but you find new relationships not seen before.”
OEE is a topic that’s popular these days. However, according to Claus Abildgren, Wonderware marketing program manager, OEE is best applied in conjunction with other tools, just as Beaudoin is doing. Abildgren says that OEE is one key and established metric to understand how well manufacturing is working and what the state of resources is. If the processor doesn’t have the discipline to look at OEE data and take action, warns Abildgren, then OEE alone won’t be sufficient to improve operations. Other tools such as statistical process control (SPC) and enterprise asset management (EAM) also can be applied. EAM improves asset performance by managing maintenance schedules to prevent a breakdown in the manufacturing cycle that can cause expensive delays.
Another tool that can reveal what’s happening with plant operations is enterprise manufacturing intelligence (EMI), perhaps an evolutionary step from plant information management systems (PIMS). EMI solutions combine real-time operational information, business intelligence and rich performance metrics. Enterprises that have implemented ERP, supply chain planning or advanced planning solutions will be able to use real-time data from an EMI program to provide real-time capacity information, allowing planning systems to be more accurate. Cargill Salt recently implemented an Informance EMI system to accelerate its manufacturing performance. Using this EMI, Cargill Salt quickly identified and prioritized production improvement opportunities to increase sprint capacity during peak production seasons. According to Jim Heard, assistant vice president of the Cargil Salt business unit, “We can now quickly identify opportunities for improving efficiency at our manufacturing facilities. This is helping us reduce operating costs and improve production.”
Connections
Today Web-based connectivity is a must, at least for processors, their supply chains and customer communications. Down the road, service-oriented architectures (SOA) and application service providers (ASPs) will provide more business connectivity through additional tools and relocation of software applications to external hosts. Two communication technologies to assist are J2EE (Java 2 Enterprise Edition) and Microsoft’s .NET. According to Chris Sault, Iconics business development manager, one Iconics customer has focused on using .NET-based communications to bring in plant performance data from several remote facilities to corporate headquarters.Most Windows-based applications today are being built upon .NET, as this has been the evolutionary outcome of earlier Microsoft developers’ packages. According to Allpax Director of Software Engineering Jonny Watkins, “Microsoft forces its users to upgrade at some point. The same happens with development platforms. If developers aren’t looking into .NET by now, they’re sticking their collective heads in the sand.”
According to Jay Deakins, president of Deacom Inc., because its Accounting & ERP system is written entirely in .NET, users can access the system from any remote location. .NET also allows various software applications to be readily connected. Another plus for .NET, says CSB-System International President and CEO Patrick Pilz, is .NET’s support for portable Windows devices such as Windows Mobile Smartphones and handheld computers within the plant.
Not everyone, however, is sold on .NET, especially those providers traditionally based on non-Microsoft platforms. Sterling Commerce, according to its Product Marketing Manager Peter Wharton, chose JSP (Java Server Pages) instead of .NET technology for a number of reasons, including its ability to scale to meet the transactional volumes required by its customers. For access to its solutions, the applications use authentication based on the J2EE Authentication and Authorization standard, where user rights and permissions are role-based to allow specific access to functionality needed by the user.
Bob Carver, VP of logistics software at HK Systems, doesn’t see any urgency to using .NET. He still supports a fair number of UNIX installations, and his company is not as tied to Windows at this time. Based primarily in Oracle technology, HK Systems is working with .NET, but migration is still five to seven years away.
Rather than pit one of these technologies against the other, processors should make sure that the suppliers they select are conversant in both platforms. And today, the tools are there to connect the Java camp to the Microsoft world. As Fraser points out, there are probably just as many J2EE proponents as there are .NET and each has its advantages and disadvantages. SAP is one of the providers that has done a lot of work in bringing the two together.
According to Johann Heydenrych, director of industry solutions at itelligence, processors that have good open application frameworks in place will be able to bring a multitude of applications together and drive push concepts via portals, ensure single sign-on and authentication and provide ease of use. He, too, commends SAP as having a leading position in this regard through its Netweaver platform.
While the concept of renting a major software application from an ASP has a long way to go with most processors, some applications (e.g., supply chain) may lend themselves better to the model. For sure, most processors still want to see their server within the confines of their facility and their clients hooked to it via internal networks. But in support of the ASP model, Wharton says, “The way the software is delivered is really what the game is all about. Being able to deliver in an on-demand environment is changing the way people think about supply chain software. As on-demand software is leased and hosted in another location, there is no software or hardware to buy and manage. Upgrades are delivered to every user at the same time, so every user has the latest capabilities.”
Warm, fuzzy feeling
While software vendors may become enamored with their high-tech solutions, processors are still looking for the basics from their suppliers. In fact, when vendors forget the basics, processors look for new, more sensitive vendors. Gary Gold, corporate vice president of Berner Foods is very pleased with his current software partners, CDC (Ross) and MVI, but is quick to list what made him drop previous suppliers. Gold likes to know that his suppliers are aware of Berner’s needs at all times and check in to make sure things are running smoothly. He doesn’t like to be nickel and dimed to death on after-hours support, new needs questions and problems that were overlooked in the beginning. Applications should work the way they were originally presented, and if they don’t, they should be fixed at the vendor’s expense, he says.What do processors want from their software? Gold sums it up: “Manufacturers want reliable, all inclusive software-one that does it all or comes close.”
View the Software Guide
Looking for a reprint of this article?
From high-res PDFs to custom plaques, order your copy today!