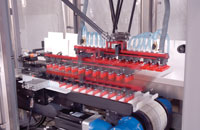
Robotics for secondary packaging have removed a bottleneck at many food plants and helped optimize upstream equipment performance. Source: Bradman Lake Group.
The IBP project was a stab by company executives to get ahead of looming labor shortages. They commissioned Foster-Miller to identify and execute automation projects that could eliminate the nastiest, most repetitive jobs. One solution was a four-axis bucket system that oriented and packed up to eight loins a minute in 100-lb. cases.
The system eventually was deployed to eight plants, but the drive to automate soon lost steam. Now, however, each US Immigration and Customs Enforcement raid on a meat plant reinvigorates the rationale for automation-a fact not lost on robotics suppliers, many of which anticipate a sharp increase in applications in meat, poultry and other industry segments.
For those who have not kept up with the technology, pleasant surprises await. Standardized solutions are not yet the norm, but the amount of custom engineering required is down significantly. Reliability at accelerated operating speeds is better than ever. And project costs are less likely to retard additional investment.
Suppliers of robotic arms have been the traditional market drivers, and they continue to fabricate entire welding and painting systems for automobile manufacturers. Those suppliers are improving their components to make them practical in extreme cold and in washdown environments, but for the most part, they defer to systems integrators and packaging machinery OEMs to drive innovation in food applications. Little distinguishes the arms themselves. “Our operating speeds are the same, our reliability is the same, our prices are the same,” acknowledges one robotics engineer, adding, “the C word (commodity) has come up.”
The evolution of Colborne Inc.’s bun-basket loading (BBL) system illustrates how value is being added in food-packaging robotics. Designed as an alternative to pattern formers and manual placement of bread and buns into baskets, BBL originally used SCARA robotic arms, sweeping product into the basket. Five years ago, BBL was coupled with a pack pattern optimization software developed by Colborne’s Foodbotics division. The program takes advantage of bread’s natural compressibility to calculate loading patterns based on up to 7% product compression. That led to end effectors that use vacuum cups and compression plates to get 25-50% more fresh product into a tray. As development continued, Foodbotics eventually standardized on articulated arms from Fanuc Robotics America Inc. to speed integration and lower costs for wholesale bakeries.
“We go end to end, unstacking the baskets, inspecting and rejecting defective baskets and automatically stacking the filled baskets,” says Rich Hoskins, president of Lake Forest, IL-based Colborne. “Most of the automation system now is standard, with that last 10% custom to the bakery’s basket.”
The first BBL was installed in 2003 at Pepperidge Farm’s Bloomfield, CT facility and is now used in 18 commercial bakeries. Removing people from the loading equation is only part of the return on a bakery’s investment: A recent analysis determined one firm wedged more than 400 additional trays on each 53-ft. trailer, improving distribution efficiency by 30%.

Applications Engineer Steve Holtschult (right) and a Foodbotics programmer apply pack pattern optimization software to a bread-handling project. The program generates alternatives that can boost tray capacities up to 50%.
Robotics enablers
High-speed pick-and-place delta robots have been offered by ABB Robotics Inc. for a decade, but food applications were limited until a washdown version was introduced, says Richard Tallian, market development manager for the Auburn Hills, MI firm. Washdown compatibility was only one roadblock to use, however. “We can only supply the basic tools,” Tallian states. “The integrators make the rubber meet the road.”One example is Charlotte, NC-based Bradman Lake Group, which standardized on ABB’s Flexpicker in 2002, according to president Nick Bishop. “There is a heavy emphasis on using standard components in a customized solution,” says Bishop, and arms lend themselves to standardization. The value-add in his view is the end-of-arm tooling and the package ingress and egress engineering the company provides.
Until recent years, many of Bradman Lake’s food clients saw their highly automated primary-packaging operations devolve into labor-intensive casepacking and cartoning. The introduction of flexpickers, increasingly coupled with vision systems, is removing a former bottleneck and allowing plants to crank up the speeds on primary wrapping and filling machines. “The introduction of robotic techniques has led to a revolution in thinking about what is possible,” Bishop insists, “and rendered electro-mechanical techniques and mechanical systems obsolete.”
Demand from retailers for pallets with mixed loads is a one-step-backward challenge for manufacturers and distributors alike. Two-step-forward solutions are appearing in the form of end-of-line robotic palletizing systems. One provider is Aidco International, a Cincinnati palletizing specialist. The firm engineered a system using suction grippers and a reciprocating table to layer mixed assortments of milk for a dairy. “They had built a conventional machine, and it was a headache,” recalls Salh F. Khan, Aidco’s president. “They knew the solution had to be a robot.” The dairy’s square containers allow the palletizer to form two layers before a tearsheet has to be inserted. The completed pallet is then stretch-wrapped.
The software that interfaces with the order system to determine how many units of whole, 2% and fat-free milk to put on the pallet and the “smart gripper technology” are the system’s points of distinction. “A robot arm is a commodity,” agrees Khan. “The end-of-arm tool and the user-friendly HMI and software is where the value lies.” Aidco’s dairy palletizer now runs in three locations.
In fairness, commodity may be too harsh a word for the most iconic component in robotics. True, competitors quickly duplicate the advances each supplier achieves, but robotic-arm suppliers continue to introduce refinements that make possible new applications in food and beverage.
A recent example is the HE series from Staübli Robotics USA, Duncan, SC. Engineered to withstand high-pressure washdown and other moist environments, the arms are fabricated from stainless steel and aluminum impregnated with corrosion-resistant alloys. Special seals to resist moisture are used, and positive pressure inside the arm keeps water vapor out.
Two versions of the arm provide a payload range of 11-44 lbs. with six axes of movement. Besides the washdown version, the firm has introduced the Stericlean robot for vapor hydrogen peroxide (VHP) environments. A powerful antimicrobial dry vapor, VHP is used extensively in medical aseptic processing, though the FDA has yet to approve its use on food-contact surfaces. On the other hand, Tetra Pak is working on an aseptic filling system with VHP specialist Steris Corp., opening the possibility of Stericlean applications in food production.
In the meantime, HE robots provide “a nice, sleek, smooth profile for food applications, with no contamination points and no external cables,” says David Arceneaux, Staübli Robotics’ business development and marketing manager. Early feedback from systems integrators is positive, he adds.

SCARA robots pick and stack cookies for packaging. Similar automation was among the earliest robotic applications in food, though pick speeds have increased substantially. Source: Bosch Rexroth Corp.
Automation on ice
Extreme cold is a challenge for robots, and while equipment suppliers maintain their machines are up to -20When off-the-shelf won't do
Standardized components help drive down robotics’ costs, but before components can be standardized, specialty applications have to be developed. Enter Applied Robotics Inc.The Glenville, NY end-of-arm-tooling specialist was founded in 1983 as an integrator. In time, it focused on engineering specialty grippers for unconventional applications. “Standard vacuum technology can handle secondary packaging tasks, and we don’t do that,” says Clay Cooper, engineering manager. “But when you’re dealing with dynamic forces like putting raw meat into a primary pack, that’s where we come in.”
Two years ago, the company developed an electro-mechanical bag gripper to palletize 100-lb. bags of cement. “There are very few tools designed to handle more than 30 lbs. of weight,” Cooper says, and cement dust demanded specialty seals and thrusters on the end-effector shaft to prevent particles from being drawn into the mechanism. After 12,000 hours of run time, “it looked and acted like a new tool,” he says.
Benefits of the engineering investment are trickling down to Applied Robotics’ food clients, including Pepsico. The heavy-duty bag gripper is palletizing 50-lb. bags of a corrosive powder concentrate that is shipped to Gatorade facilities to create the sports drink.