Seasoning Company Expands Spices of Life
Expansion, however, meant bagging some of its old ways.

Established in 1945 to serve Baltimore’s fish and seafood markets, J.O. Spice Co. Inc. is a family-owned and operated business that has expanded rapidly. The company now has some 50 standard products, plus a few hundred specialty products, says Don Ports, president and grandson of founders, J.O. and Dorothy Strigle. While seafood seasonings and batters still are the biggest sellers, the company has added seasonings for meats, poultry and vegetables. All are distributed throughout the eastern and southern US with about 60% sold through restaurants and retail stores.
To meet the increasing demand, J.O. installed new packaging and mixing equipment and reorganized its production operations, effectively quadrupling capacity. “Our business has been growing by about 25% a year for the past five years,” says Ports, “and we were having trouble keeping up with the demand.”
Prior to the changeover in mid-2006, the company used three paddle mixers to combine ingredients for its seasonings. The mixed batches were emptied into 1,500-lb bulk bags. When a bag was full, it was raised aloft by a hoist and discharged manually into 50- and 75- lb boxes or 125-lb drums.
Now the bags are loaded into a Flexicon bulk-bag discharger and fed to two semi-automated packaging lines. To match the throughput of this system, J.O. added a 150 cu.-ft.-capacity paddle mixer. Two of the old paddle mixers still are used for retail products.
A typical batch consists of 10 to 12 ingredients (including liquid additions), depending on the product. The ingredients, mostly spices and salt, are received in 50-lb. bags or boxes, which are moved by forklift onto a mezzanine and manually loaded into the mixer below.
The mixer, powered by a 50-hp motor, can process batches of 7,000 to 12,000 lbs, depending on the density of the product. This compares with a combined total of about 2,000 lbs for the three paddle mixers previously used, says Ports. The material is discharged into bulk bags and moved by forklift to the bulk-bag discharger.
The bulk-bag discharger can handle bags up to 3,200 lbs, but J.O. continues to use 1,500 lb bags for ease of movement. The discharger frame has a cantilevered I-beam and a 2 ton-capacity hoist and trolley for lifting a bag into place.
Material is discharged from the bag into a 20 cu.-ft. hopper via an iris valve, which is opened and closed by a hand-operated wheel. The discharger is equipped with Flow-Flexer bag activators that raise and lower opposing edges of the bag at timed intervals, loosening compacted material and promoting material flow into the discharge spout. J.O. uses the activators for “stubborn products that don’t flow well,” says Ports. The hopper has dual, flanged outlets that mate to two vibratory feeder troughs for the packaging operation. Each trough feeds product directly into a 50- or 75-lb box or a 125-lb drum.
The redesigned production and packaging system is not only more efficient, but also easier to operate than the method formerly used, says Ports. In addition, the higher capacity has enabled the company to take on new business. “We had been doing some contract packaging of other products, such as cake mixes, and we have been able to expand that,” he says. Based on the increased business, Ports expects to recover his new equipment investment within four years.
For more information:
David Boger, Flexicon Corp., 610-814-2400, sales@flexicon.com
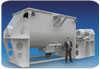
Charles Ross and Son Co.; 800-243-7677; www.mixers.com

Hapman; 800-427-6260; www.ideasthatmove.info
Schenck AccuRate; 800-394-2941; www.accuratefeeders.com .

Thermo Scientific Ramsey; 800-445-3503; www.thermo.com/bulk-handling

Modern Process Equipment; 773-254-3929; www.mpechicago.com

Hardy Instruments; 800-821-5831; www.hardyinstruments.com

Tri-Mer Corp.; 989-723-7838; www.tri-mer.com

Eriez; 888-300-3743; www.eriez.com

Flexicon Corp.; 888-353-9426; www.flexicon.com
Littleford Day Inc.; 800-365-8555; www.littleford.com
NBE; 616-399-2220; www.nbe-inc.com

Gough Econ; 800-264-6844; www.goughecon.com
Sweco; 800-807-9326; www.sweco.com
Kason Corp.; 973-467-8140; www.kason.com
NBE; 616-399-2220; www.nbe-inc.com
Mettler-Toledo Safeline; 800-447-4439; www.mt.com/safelineus
Spiroflow; 704-291-9595; www.spiroflowsystems.com
WeighPack Systems Inc.; 888-934-4472; www.weighpack.com
Hosokawa Micron Powder Systems; 800-526-4491; www.hmicronpowder.com

This bulk bag discharger empties a 1,500 lb bag of product into a hopper that feeds two packaging lines. Source: Flexicon.
Established in 1945 to serve Baltimore’s fish and seafood markets, J.O. Spice Co. Inc. is a family-owned and operated business that has expanded rapidly. The company now has some 50 standard products, plus a few hundred specialty products, says Don Ports, president and grandson of founders, J.O. and Dorothy Strigle. While seafood seasonings and batters still are the biggest sellers, the company has added seasonings for meats, poultry and vegetables. All are distributed throughout the eastern and southern US with about 60% sold through restaurants and retail stores.
To meet the increasing demand, J.O. installed new packaging and mixing equipment and reorganized its production operations, effectively quadrupling capacity. “Our business has been growing by about 25% a year for the past five years,” says Ports, “and we were having trouble keeping up with the demand.”
Prior to the changeover in mid-2006, the company used three paddle mixers to combine ingredients for its seasonings. The mixed batches were emptied into 1,500-lb bulk bags. When a bag was full, it was raised aloft by a hoist and discharged manually into 50- and 75- lb boxes or 125-lb drums.
Now the bags are loaded into a Flexicon bulk-bag discharger and fed to two semi-automated packaging lines. To match the throughput of this system, J.O. added a 150 cu.-ft.-capacity paddle mixer. Two of the old paddle mixers still are used for retail products.
A typical batch consists of 10 to 12 ingredients (including liquid additions), depending on the product. The ingredients, mostly spices and salt, are received in 50-lb. bags or boxes, which are moved by forklift onto a mezzanine and manually loaded into the mixer below.
The mixer, powered by a 50-hp motor, can process batches of 7,000 to 12,000 lbs, depending on the density of the product. This compares with a combined total of about 2,000 lbs for the three paddle mixers previously used, says Ports. The material is discharged into bulk bags and moved by forklift to the bulk-bag discharger.
The bulk-bag discharger can handle bags up to 3,200 lbs, but J.O. continues to use 1,500 lb bags for ease of movement. The discharger frame has a cantilevered I-beam and a 2 ton-capacity hoist and trolley for lifting a bag into place.
Material is discharged from the bag into a 20 cu.-ft. hopper via an iris valve, which is opened and closed by a hand-operated wheel. The discharger is equipped with Flow-Flexer bag activators that raise and lower opposing edges of the bag at timed intervals, loosening compacted material and promoting material flow into the discharge spout. J.O. uses the activators for “stubborn products that don’t flow well,” says Ports. The hopper has dual, flanged outlets that mate to two vibratory feeder troughs for the packaging operation. Each trough feeds product directly into a 50- or 75-lb box or a 125-lb drum.
The redesigned production and packaging system is not only more efficient, but also easier to operate than the method formerly used, says Ports. In addition, the higher capacity has enabled the company to take on new business. “We had been doing some contract packaging of other products, such as cake mixes, and we have been able to expand that,” he says. Based on the increased business, Ports expects to recover his new equipment investment within four years.
For more information:
David Boger, Flexicon Corp., 610-814-2400, sales@flexicon.com
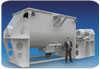
RIBBON BLENDER
This Ross 515 cu.-ft. ribbon blender, which is constructed in stainless steel, features a 200-h.p. drive and includes a jacket for heating or cooling the product. Typically used for dry product blending and drying applications, the blender is also designed for internal pressure operation. Blenders are available in sizes from ½ to 515 cu.-ft. capacity and feature vacuum construction, special discharge valves, custom covers, sanitary finishes and more.Charles Ross and Son Co.; 800-243-7677; www.mixers.com

SANITARY BULK BAG UNLOADERS
Hapman’s bulk bag unloaders work in sanitary washdown conditions and are available with stainless steel components. For batch weighing applications, productivity enhancement options include hoist and trolley loading, pneumatic bag agitation pads and a bag iris cut-off, allowing partial FIBCs to be used in the process. A modular frame fabrication design eases installation issues. Other available options include dust control systems and an alternative forklift loading system.Hapman; 800-427-6260; www.ideasthatmove.info
FLEXIBLE BULK BAG DISCHARGING SYSTEM
Schenk’s SacMaster bulk bag discharge system includes features such as bag tensioning, hoist or forklift loading, adjustable height and the company’s Posi-Flow agitation system. The system works in applications for discharging flour, sugar, cocoa powder and a wide range of other bulk materials. In addition, the system is available with optional load cells for loss-of-weight batching applications.Schenck AccuRate; 800-394-2941; www.accuratefeeders.com .

LOW-CAPACITY WEIGH-BELT FEEDERS
The Thermo Scientific Ramsey Model 90.151 low capacity weigh-belt feeder offers accurate weigh-feeding of light materials at low feed rates. The unit provides a consistent flow of materials, offers increased sensitivity for more accurate weighing of the lightest materials and permits quick and easy cleaning and maintenance. The system accommodates flow rates as low as 120 lbs per hour up to 50,000 lbs per hour and belt loadings of 2 lbs per ft. to 20 lbs per ft. It features a dual load-cell scale and stainless steel construction.Thermo Scientific Ramsey; 800-445-3503; www.thermo.com/bulk-handling

ROLLER-STYLE GRANULIZER
Modern Process Equipment Corp.’s roller-style Chunk and Bit Gran-U-Lizer reduces food products to the ideal size for inclusion in ice cream, yogurt and other mix products. The special roll corrugations reduce the size of granola, cookies, biscuits and other dry products in a single pass with minimal production of fines (dust). Designed for several changeover operations, the machine can be disassembled, cleaned and reassembled in less than 10 minutes. Its construction eliminates pockets and crevices that can accumulate product and provides tool-free access to all grinding areas. Typical capacities range from 200 – 4,000 lbs/hr., depending on the grind size setting.Modern Process Equipment; 773-254-3929; www.mpechicago.com

RATE CONTROLLER
Hardy Instruments’ HI 4060 is a compact, single-feeder, closed-loop rate controller for use in auger, belt and vibratory-based feeders, which can convert them from volumetric to gravimetric. After supplying excitation to the load sensors and digitizing the weight signal, the rate controller provides an analog output to control the feeder speed, and it adjusts this output based on the required rate at which the feeder is losing weight. The device features an embedded web server, automatic feeder refill and various alarms.Hardy Instruments; 800-821-5831; www.hardyinstruments.com

Dust collector
Designed for use by cheese, sugar, breaded product, cereal, seasoning and beer processors, the Whirl/Wet Dust Collectors operate in the 99% efficiency range for soluble and insoluble particulates 5 microns and above. Energy generated inside the unit will not allow the system to clog under any operating conditions, therefore, the agglomeration and sticky residues that plug baghouse units are not an issue. The systems have no internal moving parts, and are self-cleaning and highly energy efficient. Water use is low: following the initial charge at installation, only minor water additions are needed to compensate for evaporation and drag-out. Whirl/Wet dust collectors offer three ways to handle collected material, which is generally compressed into a filter cake. Systems are constructed of stainless steel or polypropylene and have capacities from 425 cfm to 52,500 cfm.Tri-Mer Corp.; 989-723-7838; www.tri-mer.com

Drum separator with feed protection
Eriez’s Model HFP drum in housing with feed protection provides increased efficiency of separation by regulating material flow to the face of the drum. It also prevents material from plunging directly into the drum shell, reducing the possibility of physical damage caused by impinging heavy material or heavy tramp iron. The drum features controlled feed as well as discharge capabilities and three inspection panels that allow the user to view the critical areas of operation inside the housing while the unit is in operation. The unit features flanged input and output openings to ease connection to duct work.Eriez; 888-300-3743; www.eriez.com

Bulk bag filler
Flexicon’s basic bulk bag filler performs low-capacity filling operations and can be upgraded with a material delivery system integrated with the user’s process equipment or bulk storage vessels. The bag filler is equipped with fill head height adjustment via fork lift truck to accommodate all popular bag sizes, an inflatable cuff to seal the bag inlet spout and a feed chute vent port for dust-free air displacement during filling. Performance can be enhanced by adding an inflator to expand the bag prior to filling and a programmable scale system with flow control valve for automated filling by weight.Flexicon Corp.; 888-353-9426; www.flexicon.com
Bakery mixer
Littleford Day’s intermediate intensity mixer assures a rapid and complete mix dispersion of powders and shortening in minimal cycle times. This action is developed by the turning of plow-shaped mixing tools at a speed sufficient to cause the materials to become a pulsating, mechanically fluidized bed. The basic plow action is supplemented by high-speed, high-shear chopping devices that are mounted between adjacent plows. Designed with air purge seals that prevent heat buildup and contamination of the product, the mixer works well with ingredients such as sugar, which causes heating problems with standard seals. These mixers can complete mix operations in 15-50% of the time usually required by ribbon mixers and a finisher.Littleford Day Inc.; 800-365-8555; www.littleford.com
Bag filling station
NBE’s automated bulk bag filling system increases productivity while maximizing the output of dense, stable filled bags. This system is able to fill 15 to 20 bags per hour with one operator and a fork truck driver. The station’s weigh system and automated PLC controls further reduce costs by providing consistent bag-to-bag filled weight accuracy.NBE; 616-399-2220; www.nbe-inc.com

VIBRATORY FEEDERS/CONVEYORS
Gough Econ Inc. manufactures a wide range of mechanical conveying systems. Conveyors can be custom built for specific applications and are also available in a standard range of sizes. Econ-O-Lift bucket conveyors work in gentle applications requiring damage-free product transfer, and small vibratory feeders are available to work with specialized mini-loop bucket conveyors. Swinglink textured bucket elevators move sugar, salt and similar materials vertically while the buckets remain in an upward facing position during loading and throughout the circuit. When in a horizontal position, the buckets are overlapped to prevent spillage.Gough Econ; 800-264-6844; www.goughecon.com
ONE PIECE-SCREEN
Sweco’s Fusion Screen features one-piece construction; no adhesive, epoxy or silicone is used in the manufacturing process. The one-piece construction minimizes the potential for contamination. Other benefits include precise, repeatable tensioning and engineered uniform integral strain relief. The screen consists of a gasket, strain relief and screen frame as one molded part.Sweco; 800-807-9326; www.sweco.com
CLASSIFIER ELIMINATES METAL CONTACT
Kason’s Vibroscreen gap-free classifier offers non-metallic material contact surfaces and quick-cleaning features to eliminate contamination of ultra-pure products. The 60-in. diameter classifier is configured with three screening decks for removing oversize particles and de-dusting the material, while separating on-size material into two size fractions. Interior surfaces of the screen are clad with PTFE, and screens are constructed of nylon, eliminating metal contact as required for the most metal contamination-sensitive bulk materials.Kason Corp.; 973-467-8140; www.kason.com
BULK BAG CONDITIONING TECHNOLOGY
NBE integrated its deblocking ram bulk bag conditioning technology into its bulk bag discharging equipment to break up and deliver severely agglomerated material into vertical form, fill and seal equipment. The deblocking rams reduce the material from a single 2,000-lb lump to sizes that will pass through the bag’s discharge spout without the operator having to manipulate the bag. The crumbler lump breaker further reduces lumps to a conveyable particle size using tooth agitators rotating through stationary breaker bars.NBE; 616-399-2220; www.nbe-inc.com
DRUM DUMPER
Material Transfer’s 180° rotation lift-and-dump drum dumper accepts 55-gallon drums of non-free, flowing powders and discharges the contents into a hopper at 122 inches above floor level. The unit features a lift-and-seal system for dust-tight operation, a control-link rotation system for 180High-volume metal detector
Mettler-Toledo’s Safeline Gravity FlowHD metal detector detects ferrous, non-ferrous and difficult-to-detect stainless steel contaminants in high volume, free flowing powders and granular products. Constructed of stainless steel, the detector has smooth flowing lines and can quickly be dismantled without tools to facilitate cleaning and inspecting. A cowbell style Seal-Tite diverter minimizes system height and prevents leakage, reducing product giveaway. The system’s integrated digital processing electronics and high-speed diverter valve minimizes product loss. The control center can remain with the unit or be mounted in a convenient location, where operating parameters are set and reviewed and access codes can be used to prevent unauthorized adjustment.Mettler-Toledo Safeline; 800-447-4439; www.mt.com/safelineus
BULK BAG DISCHARGER
The Spiroflow Type 3 bulk bag discharger accurately dispenses bulk ingredients and/or minor additives from 20-lb to 3,500-lb batches by using electronic load cells directly below the top bag holding frame. This ensures that the bag and load cells are safely off the floor and out of the way of facility hazards such as forklifts. An integral transfer conveyor, for example, a flexible screw conveyor (FSC) can be suspended from the holding frame for a self-contained discharge and loss-in-weight dispensing system.Spiroflow; 704-291-9595; www.spiroflowsystems.com
GRAM SCALE
WeighPack Systems’ Verita gram scale provides accurate weights of powders and other dry products in 0.1 gram increments with an accuracy of 0.33 gram. The scale achieves its accuracy by mounting the weigh bucket and load cells on a stand separate from the hopper and pans. The separation means vibrations from the hopper and pans do not interfere with the weigh bucket, allowing for more accurate measurements.WeighPack Systems Inc.; 888-934-4472; www.weighpack.com
PULVERIZERS WITH ULTRA-FINE CAPABILITIES
Hosokawa Micron Powder Systems’ Universal Mikro Pulverizer (UMP) provides finished materials from coarse granulation to ultra-fine particle sizes. The UMP features fabricated housing with a hinged door and tri-clamp closure mechanism. Interchangeable grinding mechanisms give the user unlimited ability to change particle size and distribution. The unit can be fitted with a knife-type rotor to provide granular products. An impact hammer and screen assembly can be substituted to make finer materials down to 50 microns. The pin discs and a new bearing housing design can run at a top speed of 28,000 rpm to produce powders to 25 microns. The unit is available in 1-, 5-, and 15-hp sizes.Hosokawa Micron Powder Systems; 800-526-4491; www.hmicronpowder.com
Looking for a reprint of this article?
From high-res PDFs to custom plaques, order your copy today!