TECH FLASH
Cool energy waste in your refrigeration systems!
Energy audits can spot potential waste and provide short-term fixes, but a refrigeration energy management system can keep temperatures and costs cool.
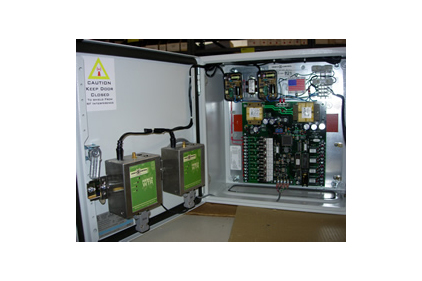
Most processing plants have energy losses in many areas. Obvious loss vectors include leaky water lines, hotter-than-necessary water, leaky air lines, steam traps, inefficient boilers and/or heat going up the stack; lighting, inefficient motors, equipment left running and doing nothing; and refrigeration inefficiencies. Not-so-obvious losses include climate control imbalances, leaky building insulation, uninsulated refrigeration lines, thermal leaks on ovens, motors overheating due to bad bearings, etc.
FE conducted an interview with Alex Daneman, president and CEO of Hench Control, a global manufacturer and service provider of modular energy management systems (EMSs) for industrial refrigeration systems. Daneman has more than 10 years of experience working and consulting with food and beverage processors. He has been involved in manufacturing and processing for over 30 years.
The basic principles of energy savings apply in all facets of industry, whether it’s in the food and beverage, hard goods and/or vertically integrated manufacturing.
For some food and beverage processors, the cost of running refrigeration systems is a big part of their budget. Fortunately, there are many ways to curb energy waste in refrigeration systems. FE asked Daneman about energy audits, refrigeration energy management systems and what kind of results processors can expect by installing an EMS to manage refrigeration systems.
FE: What should an energy audit include? Who should perform it? What should the auditor know about energy management systems and refrigeration systems?
Alex Daneman: An energy audit should include documented run times of all equipment; pressure values and ranges based on time of day and seasonality; temperature values and ranges based on product mix and turnover; and frequency and length of defrost cycles, to name a few. An analysis also should be conducted on potential limitations based on existing equipment and/or the refrigeration engineering of the plant. Without taking into account all these variables and more, it’s impossible to design and build a proper system to automatically operate and control a facility.
The audit should be performed by an individual who is knowledgeable of all aspects and components of the project and environment to ensure compatibility and effectiveness of the system. The audit must take into account the refrigeration equipment and design; operational process and requirements; electrical and mechanical compatibility; and hardware and software functionality and capabilities. Ignoring any of these areas could potentially damage or at least limit the success of the project.
The auditor must know where the opportunities are to quantify and take advantage of them, along with how to incorporate and implement a system to monitor, trend/record and control the refrigeration system while not disturbing or affecting the operational process of the facility. At Hench, our field technicians and in-house engineers work together in this capacity to specify the right system for each customer based on its objectives and expectations.
FE: What hardware can monitor energy losses? What is practical, cost effective?
Daneman: The simple and most cost-effective hardware to monitor energy losses would be temperature sensors, pressure gauges, pulse counter interfaces and current sensors. More complex devices like IR cameras and sonic leak detectors are also options, provided they supply the proper output, for example, a 4-20 mA signal. Our system uses a variety of these components to monitor, trend/record and control refrigeration systems based on energy-related metrics.
FE: Is there a place for wireless sensing devices?
Daneman: Wired is still most reliable because it is very resistant to outside interference, and it is easy to harden against mechanical damage, for instance, by placing the wires in conduit. Wireless is more cost effective because you don’t need to run wires at all, but by its very omni-directional nature, it can be affected far more easily by environmental [noise] sources. The decision really depends on the type of facility and its limitations. It is common for us to use a combination of both wired and wireless in our installation projects, taking advantage of the best of both worlds.
FE: Is it practical to use a sensing device with multiple parameters?
Daneman: One hardware device we provide to monitor more than one parameter is the wet-bulb relative humidity sensor. With this device, you get both temperature and relative humidity out of the same process.
FE: Can typical process control I/O systems be used to monitor/control energy management systems/equipment? What specialized devices can be used in an energy monitoring capacity?
Daneman: Regarding process control I/O systems used to monitor/control EMSs, our system demonstrates that relationship very well. Hench manufactures controllers that have both simple ladder logic as well as more complex firmware solutions that allow for operations such as load balancing, demand-driven efficiency, compressor capacity management, defrost cycling and horsepower trimming, as well as an automated reporting system that can trigger a deeper understanding of what is really going on in a facility. The Hench system is a combination of process control and energy management. That is, the platform our system is built on is bundled together.
The Hench hardware works in unison with the conjoined software to monitor, trend/record and control. We also provide weekly reports documenting the measured kWh of each motor so the user can have a detailed view of exactly what is taking place and where the energy is being used. It is this type of empirical data that allows intelligent, proper decision-making to take place.
FE: What software can be used to monitor energy usage in refrigeration systems? What control capabilities should it have? What kind of reports should it generate? What experience should the creators of an energy management package have with WAGES+R monitoring?
Daneman: We offer several software programs to aid in saving energy. They are known in the industry as “Load Shedding Tables” or “Demand Reduction Tables.” All these tables reduce energy usage by changing set points automatically, which allows the end-user to manage energy when the power use or energy price is high. Conversely, this also enables the lowering of temperature in cold rooms when the power use or energy price is low. The Load Shedding Table is the most commonly used—it changes the set points based on a control value. That control value can either be current kW [power usage], price per kW, demand charges, day and time or a combination of any or all.
We have the ability to utilize demand charges, real-time pricing and current kW simultaneously. For example, there is a peak demand table that is downloaded monthly, which has the peak demand charges for every hour of every day for the month. The real-time pricing tables are usually updated every five minutes. If the current kW usage is below the peak demand threshold, the system will control the refrigeration equipment based on the real-time pricing table. If the current kW usage is above the peak demand threshold, the controls will throttle back power to get the demand down.
FE: How can an energy monitoring system be integrated with plant-wide process control and ERP systems? Can a process control system be extended to implement energy management and control?
Daneman: The Hench system not only provides energy monitoring, but energy management with active control. The system accomplishes energy and process monitoring and control together—turnkey and bundled in one easy-to-use package. You don’t have to worry about integrating two separate systems and hope they are compatible with each other.
We’ve created a microprocessor-based system that reduces energy use in industrial refrigeration plants by employing an energy best-practice approach to controlling the refrigeration plant that goes beyond the conventional step-logic controller, adopting instead a more intuitive approach to system design based on thermodynamics. The end result is an intelligent energy management system that provides the required cooling demand for minimal energy consumption [and hence cost], while reducing operational and maintenance costs.
Our energy management system strategies are a compilation of 20-plus years of work and evolve each day based on real applications. While the main focus is reducing energy usage, the EMS is also an advanced operational control tool allowing users to maintain the highest levels of refrigeration plant control in a user-friendly package. The Windows-based software allows operators to make necessary changes by simply pointing and clicking. The only information that has to be entered is the equipment type and the control set points. The calculations for control are generated from these set points. This eliminates time-consuming and expensive site programming and ensures rapid, easy startups.
FE: What are some advantages of an EMS tailored to refrigeration systems?
Daneman: Hench EMSs provide several competitive advantages:
- Between 15 percent and 30 percent energy savings
- Reduction in greenhouse gas emissions by millions of pounds of CO2 per year/per facility
- Ease of use through a sophisticated graphics user interface and Internet-based system that can be used to control multiple locations from a single site
- Elimination of time-consuming site programming for rapid and easy startup installations
- Reduced reliance on manual intervention within the refrigeration operation to manage energy use
- Reduced training for refrigeration operators
- Alarm and texting system for advanced safety and product reliance
- Web-based viewing and manipulation from any remote or mobile device
- Monitoring for backup and maximizing energy savings.
Our systems use many techniques to improve a plant’s efficiency. With the real-time monitoring of dozens of parameters, the systems save energy by operating the most efficient combination of compressors as the load changes; keeping the suction pressure as high as possible and the compressors operating near the top of their capacity; improving the efficiency of the evaporator defrost process; keeping the discharge pressure as low as possible; trimming horse power; and controlling energy demand charges and demand pricing.
FE: How do you measure the effectiveness of an energy management system? What parameters show that improvements made are kept in place (maintained)?
Daneman: One way to measure the effectiveness of an energy management system is to log the plant operations data prior to installation of the EMS and then document and compare the values of the key performance indicators. At Hench, we do this through our initial energy study projections, along with our weekly reports that document the savings and savings opportunities, based on our findings and recommendations. This is an extremely valuable tool for management to gain insight into how well its system and plant are running. Plus, it is a proactive and ongoing process, not a one-time tune-up, ensuring this high level of efficiency is maintained indefinitely.
FE: What kind of ROIs should be expected?
Daneman: The ROI on our systems typically range from one to three years on average. This includes the cost for the hardware, software, installation and ongoing monitoring support compared to the energy savings realized by the system. On our weekly reports, we show the savings breakdown from a weekly view to a monthly view to a year-to-date view and rolling 12-months so the customer can view the full spectrum of data—and most important—will know that after the system is installed, the ROI is real.
FE: Is a permanent energy management system more useful than doing an audit and fixing the problems the audit finds?
Daneman: A permanent EMS is absolutely more useful and effective than a one-time audit/tune-up because it’s ongoing. The EMS, in conjunction with our proactive monitoring program, is the best combination and solution. What we have observed is that once a new installation [or upgrade] is completed, performance slowly deteriorates over time due to various factors. This is no different than if you were to buy a brand-new car and never take it in for an oil change, replace the brakes, etc. The key things on the performance side are to ensure everything is performing at its peak level, and the energy savings are being maximized—the monitoring program takes care of these.
Keeping a plant operating on its optimal settings is a never-ending task. Because so many different factors need to be taken into consideration such as the weather, product mix and demand, fine-tuning is an ongoing exercise, and that is the key to maximizing the energy savings.
The bottom line is that monitoring is great; doing something about the findings contiguously is better!
FE: Are there any energy-savings stories that you’d like to share?
Daneman: One of our customers owns more than 400 brands including 13 that each achieve annual sales in excess of €1 billion [about $1.28 billion]. Its ammonia-based refrigeration production facility in Kansas installed a Hench system and participated in the monitoring program from the onset.
The actions and results of this project were:
- Increased compressor efficiency to between 85 percent and 95 percent for both stages on average, depending on the load
- Reduced condenser’s average discharge pressure from 150 psi to between 120 and 135 psi
- Enabled fan cycling
- Reduced evaporators’ defrosts duration by terminating them based on hot gas temperature instead of time
- Reduced evaporators’ defrosts to less than seven times a week and/or one defrost per day
- King air units became managed by the Hench system utilizing the temperature sensor, temperature set point, temperature dead band and a weekend/weekday mode instead of just an on/off operation
- Had the Hench system and monitoring program not been in place at this facility, it would have paid $138,660 on top of its existing utility bill during the first 12 months after the system was installed
- Kilowatts saved during the first 12 months equaled 1,854,000
- The return on investment for this project, including cash outlay and monthly monitoring fees, occurred after month 20
- Now that the initial cash outlay has been recouped, the customer realizes a seven-plus times ratio of savings versus cost for the monthly monitoring fees.
For more information, Alex Daneman, Hench Control, Inc., 510-741-8100, alex@henchcontrol.com; www.henchcontrol.com
Looking for a reprint of this article?
From high-res PDFs to custom plaques, order your copy today!