Food Safety
Flooring: Do it right the first time
Perhaps the biggest failure for companies building new plants or modifying them is the choice of flooring.
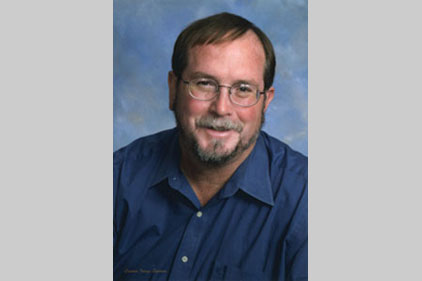
Building a new facility or modifying an existing structure is always a challenge, largely due to the cost involved. There is often a push to cut expenses, even though those cuts may hurt in the long run. Perhaps the biggest failure for companies building or modifying a plant is in the choice of flooring. If the floor is not correct for the application, constant problems will occur.
For instance, I once worked with a meat processor that decided to diversify its business. Built by a European firm, the processor’s plant had acid-resistant brick floors, and there was never a problem. But then, the processor built a new juice and confection plant and installed thin tile floors. Within weeks, water got under the tile and lifted it up. Then, the acids from the juice and cleaning compounds attacked the concrete, causing pitting and exposing the aggregate, which compromised the processor’s ability to make repairs. The floors had to be replaced each year, adding cost and lost production time.
The lesson learned is this: Take your time selecting flooring material, the contractor and how the floor will be installed. Consider how drains will be installed, the drain capacity and drain type. Also, consider how many drains are required and the level of sufficient fall for proper drainage. Floors must slope toward the drains with a fall of approximately 1/4 inch per foot.
When determining what kind of floor to install, look at loading, products that will be handled and processed, the potential for damage, temperatures to which the floors will be exposed and the ground on which you’re building. Consider how much of the day the floor will be exposed to water. Will it be wet all day or only for a short period? It is also imperative to plan ahead. Will new products or new ingredients be used in the future? What new chemicals will the floor be exposed to? And what about equipment? You may be using pallet jacks today, but are forklifts in your future?
Many different flooring materials are available, and they are continuing to evolve. Therefore, it’s imperative that you work with contractors who will explain the different options and their limitations and those who know how to take into account the stresses the floors will be exposed to.
In addition, floor color should be considered. Many processors now opt for floors that are light gray in color since they reflect light and brighten the work area. A processing area with white walls, a light gray floor and good natural or artificial light creates a fairly comfortable workplace.
Safety also must be considered. Will the floors be exposed to water, oil or grease? Will these materials make the floors slick? Flooring materials formulated with grit can make them less slippery without compromising cleanability. Manufacturers also are now incorporating antimicrobial compounds into flooring materials.
Plan ahead and make the right flooring decisions from the outset. The upfront costs might be a bit higher, but it is very likely your money will be recouped over time when you factor in the cost of maintenance and repairs.
Reference:
Katsuyama, A.M., “Principles of Food Process Sanitation 2nd Edition,” pp. 171 – 241.
Looking for a reprint of this article?
From high-res PDFs to custom plaques, order your copy today!