Plant Maintenance
Best practices in plant maintenance and safety improve operational efficiency
ProFood Tech offers insights and solutions to minimize risk, prevent worker injuries and reduce costs
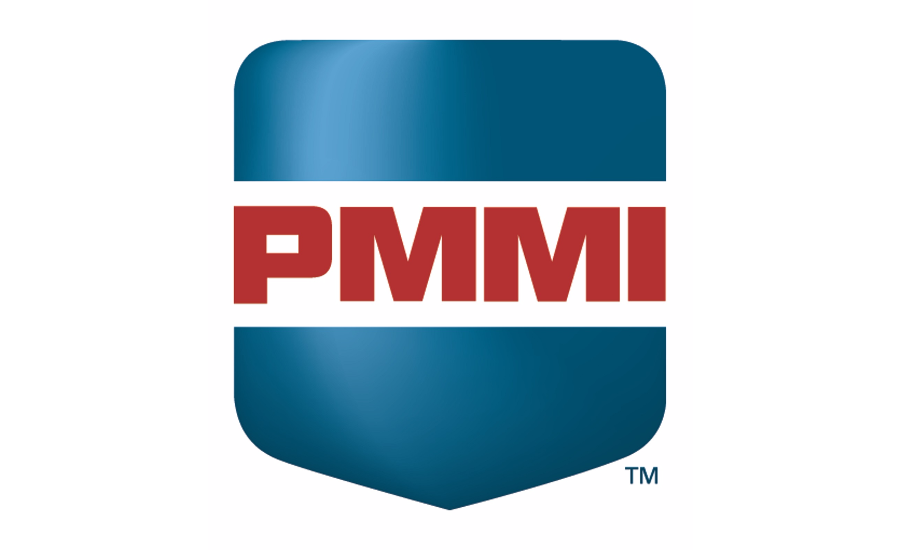
Plant safety is critical to productivity. Proper plant maintenance plays a significant role in reducing unscheduled downtime and improving safety. Maintenance schedules for plant equipment exist for a reason. Machinery and equipment that is not properly maintained can be very dangerous. Even equipment with fail-safes can malfunction if you do not perform regular maintenance checks.
By following required procedures, equipment can be kept operating at peak performance. When service is not completed as needed and correctly, machinery can overheat due to lack of lubrication, or suddenly jam due to a broken belt or drive gear.
If filtration equipment is used, the filters must be periodically inspected and replaced. Blocked filters can lead to undesirable exposure for workers or the environment. Blades and bits must be sharp to provide clean and safe cutting. When this equipment dulls, it is more likely to snag than cut through the material. Good maintenance practices go a long way towards increasing safety and ultimately improving operations.
To minimize the risk, make sure your equipment meets current safety standards. The ANSI/PMMI B155.1-2016 Safety Requirements for Packaging and Processing Machinery standard (available for purchase through the ANSI webstore at http://webstore.ansi.org/) was recently updated by PMMI, The Association for Packaging and Processing Technologies. This standard is designed to improve the safety of packaging and processing machinery and eliminate injuries to personnel working on these systems by establishing requirements for the design, construction, reconstruction, modification, installation, set–up, operation and maintenance of processing and packaging machinery systems.
This standard guides processing and packaging machinery suppliers and users through a risk assessment process designed to ensure that reasonably foreseeable hazards are identified and corresponding risks are reduced to an acceptable level.
But doing a risk assessment once is not enough. Have your equipment inspected on a regular basis by a professional, whether in-house or contracted. And don't rely solely on those formal, timed bound inspections; make sure your employees know how to perform a quick inspection before and after using each piece of machinery. Check with your technicians and your suppliers’ service technicians to see if they noticed any potential safety issues.
The people who come in regular contact with your equipment should know what a machine looks like, how it smells and how it sounds when operating properly. They should know how to spot warning signs immediately, such as exposed wires, burning or electrical smells, abnormal wobbles, grinding or scraping noises, or any other irregular sounds. If a machine is deemed potentially unsafe, it should be shut down immediately for repairs.
Here are a few smart practices to help with plant safety:
- Respect machine guards: Machine builders put guards in place to reduce the risk of hazards. By removing or modifying them, you are increasing the risk of an accident.
- Use Personal Protective Equipment (PPE): Not all hazards can be designed out of industrial equipment. PPE is a critical component to a plant safety plan.
- Proper training: Your facility is only as safe as the people working in it. If you need to develop internal capabilities in this area, check out the PMMI U Certified Trainer program (pmmi.org/certified). PMMI has a well-respected train-the-trainer program customized for manufacturers.
- Follow maintenance schedules: Well-cared for equipment that meets current safety standards can help significantly to protect people and product.
Accidents are expensive in many ways. By following basic safety guidelines and implementing proper maintenance procedures, you can reduce injuries and improve plant productivity. To learn more about innovative solutions to keep your plant safe and productive, visit ProFood Tech (April 4-6, 2017, McCormick Place, Chicago). Featuring over 400 of the world’s top suppliers, ProFood Tech is focused exclusively on all food and beverage sectors, including baking and snack, beverage, frozen/prepared foods, dairy and meat/poultry/seafood. This event will offer a full range of food and beverage processing solutions from both large companies that serve several market segments and smaller niche companies that focus on more specific needs.
Registration for ProFood Tech is open at www.profoodtech.com.
For more information, visit: PMMI.org and PACKEXPO.com and PMMIMediaGroup.com.
Looking for a reprint of this article?
From high-res PDFs to custom plaques, order your copy today!