Editor's Note
Processors need a construction plan to stay in compliance with FSMA
Weighing new construction vs. renovation requires evaluation of compliance as well as production needs
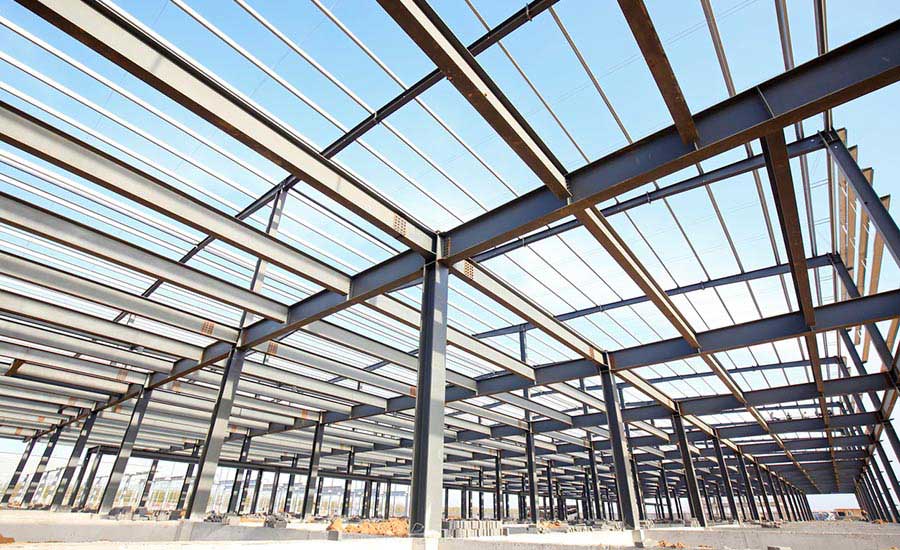
There are big changes afoot in manufacturing: Consumer trends seem to be changing at lightning speed, more entrepreneurs are entering the food and beverage market, and more stringent food safety regulations and requirements are coming down.
Since the recession, some companies might have been holding off on making major structural changes. However, with the deadline looming for small and midsized processors to be in compliance with FSMA’s preventative controls rule, changes to food safety operations might not be something that can wait any longer.
I’ve been talking with a number of food safety consultants, and they seem to think we might see a number of plants shuttered. I had a recent conversation with one consultant, who personally talked with an Obama administration staffer who had worked on writing the new rules, and he explained that in order to avoid a fine if FDA agents do find a problem, you must prove your intentions to rectify the mistake.
For instance, if there is a roof leak, and you rigged some tarp to catch any possible leaks, it’s not enough that you put up the tarp. The FDA will want to know why you haven’t fixed it yet and prove that you have attempted to. In this scenario, an acceptable answer might be that you already called the roof repair company, and its people couldn’t make it over until three days later.
In compiling this year’s plant construction survey, Food Engineering Senior Technical Editor Wayne Labs found a trend occurring in the food and beverage industry favoring expansions and upgrades of existing plants in lieu of building new facilities. However, many of these legacy plants were originally built during a time when companies didn’t give much thought to hygienic separation and allergen control of people and materials, so there’s always the question of when it is time to give up the ghost.
It is daunting to see the costs of a brand-new facility, most often reaching nine-digit figures. I’ll venture out and say that for most small to midsized companies, being able to pay this type of sum is not even close to a distant dream.
And that’s the rock and the hard place some processors find themselves between—either find the money to upgrade or be at risk of shutting down.
But is it all doom and gloom? Sometimes in reevaluating operations and procedures, a discovery is made that can increase efficiency and throughput.
At the recent FA&M Conference and Expo, many of the speakers talked about what they are doing to stay competitive. And many are employing new technology to better connect their plant and their workers. In fact, two speakers, Automation Keynote Phil Viruso, vice president of manufacturing for LiDestri Food and Drink, and Todd Parker, plant engineer for Lakeview Farms, discussed putting mobile devices in the hands of their workers to empower and engage them.
There are hard challenges facing the industry; however, the technological innovations being developed and adopted today could be not only the silver lining, but the future of food processing.
Looking for a reprint of this article?
From high-res PDFs to custom plaques, order your copy today!