Editor's Note
Survey shows that budget concerns hold back innovation, productivity
Companies are not showing much change in capital, operations spending
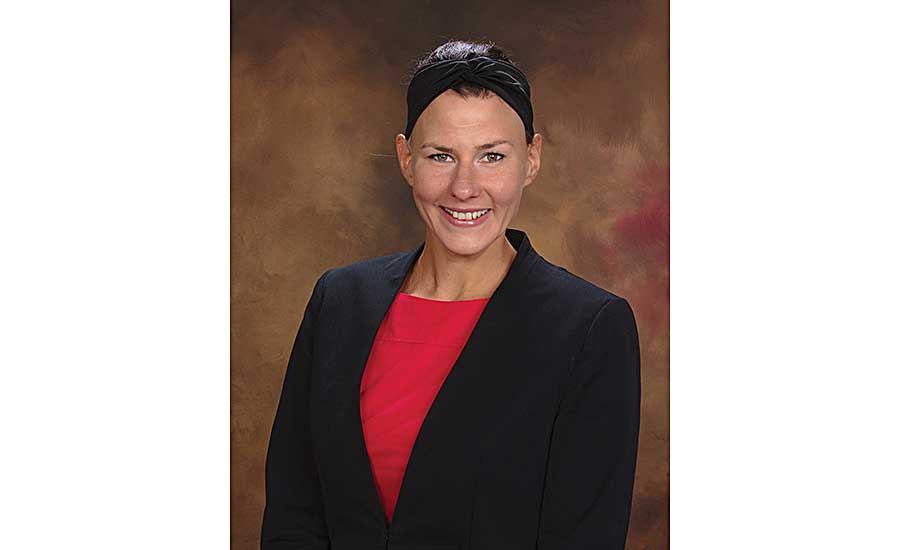
This issue features our annual State of Food Manufacturing survey. No surprise that automation, once again, took the number one spot in the Top 10 future trends list.
Of course, it’s not just our industry. A recent episode from The Wall Street Journal’s new podcast, The Future of Everything, discussed the quantitative models that are running a third of all trading in the US today. The “quants,” as they are called, use algorithms to predict what human traders will do and beat them to it before action is taken.
It’s a whole new world out there.
All this really hit me a few months back. I realized that for the past 10 years, while many of us have been dealing with the fallout from the recession and have been consumed with business, life and personal finance worries, we have entered into a new era.
As I probably have mentioned before, I studied anthropology in undergraduate school. A large part of that curriculum was studying different archaeological periods of man, such as the Stone Age, the Bronze Age and the Iron Age. This system is largely based on what tools were being manufactured and used.
These ages lasted hundreds, and sometimes thousands, of years before the tools switched, but in a short time period, everything seems to change. That feels like what has just happened: We went to bed in an analogue era and woke up in a digital one.
There is a caveat that could be slowing progress. It was identified by our survey respondents as the number seven trend that will likely affect manufacturing for the next few years, and that’s budget constraints. Food Engineering’s survey has charted the budget allocations for new equipment purchases in the past decade, and there really hasn’t been that much change in how much companies are allowed to spend to upgrade their operations.
Budget constraint concerns also crept into several discussions during the past Food Automation & Manufacturing Conference. Jim Tonjes, former vice president of engineering for General Mills, gave a sanitary plant design talk (also referenced in this issue’s “Creating a sanitary food factory” article), in which he presented the elements that should be considered and incorporated when evaluating the sanitation needs of a food plant.
In the Q&A period, someone asked how Tonjes justified to upper management the premium costs associated with the high-end facilities buildup that he described. Tonjes said when General Mills had to hold product due to a potential safety problem, the costs started at $5 million and went up from there. So, management was willing to spend more money to eliminate any possible food safety risks.
The larger point here is that if plants are being required to do more with less consistently every year, there will be a point of diminishing returns coming soon.
However, if more money is spent on the equipment and services necessary to modernize food and beverage production—bringing it from the analogue to the digital age—that will allow companies to drive the innovation the industry needs.
Looking for a reprint of this article?
From high-res PDFs to custom plaques, order your copy today!