Sustainability
Major water savings has California grape packaging supplier ahead of sustainability goals
Company reduced water usage by 40 percent and increased profits in eight weeks
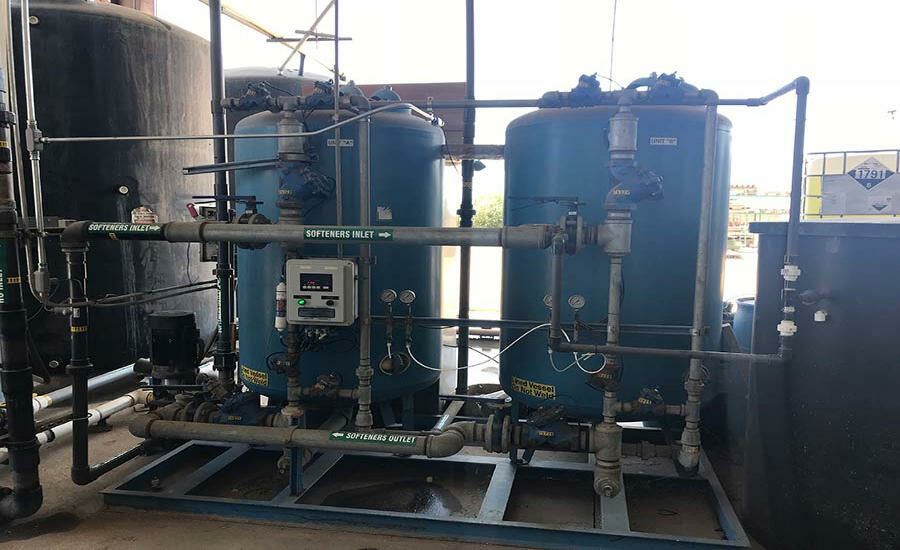
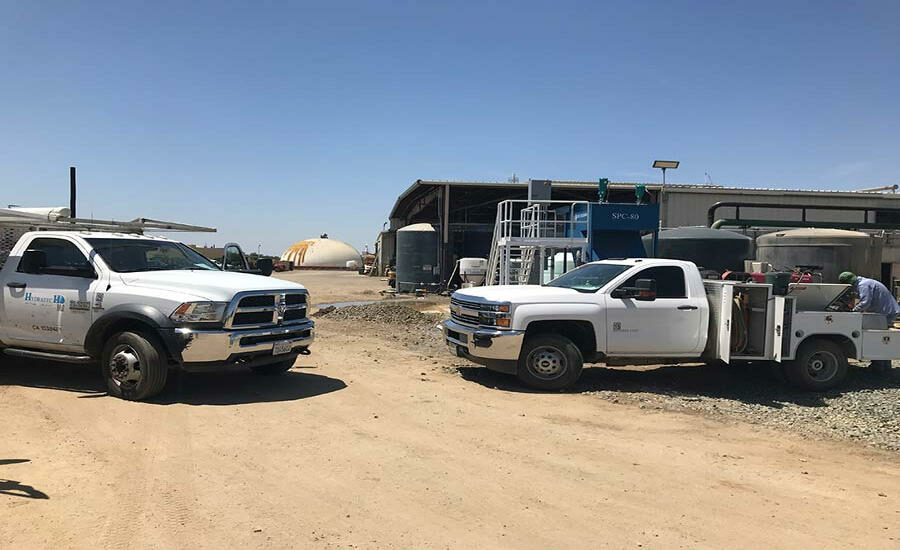

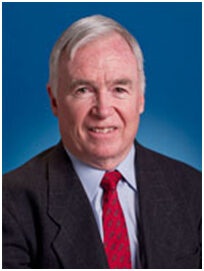




Styrotek was founded by a group of San Joaquin grape growers in 1973 to develop an effective table grape transport packaging system. The goal was a packaging system which would preserve and extend the shelf-life of the fruit, while also creating a sustainable packaging material that would be light in weight, reduce transport costs, and be recyclable.
The EPS (expanded polystyrene) foam packaging company is based in Delano, Calif. and designs and manufactures packaging for the grape industry. In just eight weeks, Styrotek was able to reduce its water usage from 20 million gallons per year to 12 million. With new equipment, the package manufacturer recycles a major portion of water back into the process, and has a significant jump on its California Sustainability 2020 Plan, already below the “half-acre per year” footprint set for the company. (For more on EPS and its properties, see "Expanded Polystyrene (EPS): Ultimate Guide on Foam Insulation Material" on the Omnexus website.)
CEO Dick Lindenmuth joined the company with a pledge to help make sustainable transformations in the EPS process. The company was losing money, and its process was inefficient. Lindenmuth pulled together a Sustainability Team including Styrotek employees who were intimately familiar with operations and others who worked as a team to develop a systematic approach to reduce water usage for the manufacture of EPS Grape Boxes in California.
Within eight weeks, the team produced positive results including a plan to avoid a shutdown, reduce water usage and resolve water issues no one had ever seen. The team didn’t have the resources on hand to put the plan in action, but went out and procured them. At the same time, the grape harvest would be starting in eight weeks with a limited crew. The company was able to restart manufacturing before the grape harvest, and increased profits and had a positive cash flow.
The changes ordered by sustainability team produced some amazing results:
- Eliminated significant water waste and reduced total water usage within eight weeks from 20 million gallons to 12 million gallons per year
- Acquired a new reverse-osmosis (RO) unit to treat water during the manufacturing process
- Installed new water well, and will recycle water with zero waste matter
- Below the California Sustainability 2020 plan set for the company
- Increased production, increased quality, reduced overhead and reduced product cost
- Restarted manufacturing before the grape harvest
- Returned the company to profits and positive cash flow
FE spoke with Lindenmuth to find out how his company accomplished these tasks with such amazing results.
FE: Before grape growers used EPS packaging, what did they use? What were its downfalls?
Lindenmuth: Wooden crates and boxes were used. Then, cardboard and eventually EPS. Some produce companies, including one of the largest grocery retailer chains in the world, were concerned about recycling and forced the use of re-useable plastic containers. This proved expensive and did not work. Today, all exports use foam. Those shipments that go through cold chain storage for increased shelf life use foam and most other shipments are in cardboard. Out of 110 million table-grape shipments 40 million are EPS foam and the others are cardboard
FE: Fill us in on the EPS process, and where water is used.
Lindenmuth: EPS, Expandable Polystyrene, is a process where polystyrene in resin form is sent to the producers who then use steam/water to expand the beads and put them into silos from which the actual molding machines are served. The expanded polystyrene is put into the mold inside a machine and then steam is used to make the expanded resin flexible and it is formed into grape boxes. When the mold opens (using steam to open the mold) finished grape boxes are dropped onto a belt where eventually lids and boxes are assembled into finished product for shipment
FE: Is EPS material recyclable at various points in the supply chain? If you have scraps in the process, can you recycle it back into the manufacturing process?
Lindenmuth: EPS can be recycled back into the manufacturing process by grinding and mixing it with new expanded resins in the silos that feed the molding machines to make the final product. Usually about five to seven percent of “regrind” would be the maximum used for this purpose. The rejected material can also be “densified” heated and reduced to a roughly two pound block for shipment to recyclers that manufacture picture frames, door frames, bicycle helmets, surf boards and other products. This is a normal process and at the moment recyclers pay roughly $.30 per pound. There is also a process that has recently been introduced from Germany whereby a company purchases the recycled material or is given the material to recycle and they use a chemical process to return the polystyrene to its original state. They then ship this material to manufacturers who manufacture the resin and then ship the resin to the EPS manufactures so that it can be used to make finished products (basically a full-cycle recycling process)
FE: What’s the story on water usage in the EPS process? Where and how is water used?
Lindenmuth: Water is basically heated by large boilers and developed into steam to expand the resin and to also make the resin flexible to be molded into finished products. Most molding machines also use the excess steam to open and close the molds.
FE: What was done with the wastewater before your sustainability team evaluated your process? Did you have a wastewater treatment facility on site?
Lindenmuth: Waste water was originally put into evaporation ponds and also a pond that would be used by emergency teams in the event of a factory fire. That “fire pond” required hoses and pumps for immediate emergency access. Today we are using various filtration systems, including reverse osmosis as well as a clarification process which removes suspended materials from the water after it has gone through the manufacturing process so that we are able to recycle a significant amount of the water and return it to the manufacturing process. It is not a wastewater treatment plant, but is very similar to municipal reservoirs that provide drinking water for residents.
FE: What recommendations did the team make in terms of equipment, the process itself, and/or the facility?
Lindenmuth: California is an area where droughts have been more frequent and a significant amount of the world's supply of fruits and vegetables originates. We are, therefore, among the pioneers of developing better ways to use and recycle water. Without examples already in place to choose from, we are using tried and true technologies, but also experimenting with new and better methods. Perhaps other areas will come and view what we have (and continue) accomplished and use them in other areas of need.
FE: You mentioned addition of RO equipment. Was there any other equipment installed?
Lindenmuth: Yes. Other filtering systems, Sand filters for example, cooling towers (which we may convert to chillers), a clarifier which removes the suspended particles from the water after it has gone through the manufacturing process.
FE: What equipment was chosen to fix the process? Who makes it? Who installed it?
Lindenmuth: We work with a team of experts, SEACO, Water Solutions Engineering, and equipment manufacturers (WaterMark is one) with some outside consultants such as Jim Brakebill, who is an expert in the EPS manufacturing process. A good team is absolutely required.
FE: What facility makeovers/renovations were needed?
Lindenmuth: Piping and filtration stations everywhere!
FE: Is there any automation involved in the process? Where?
Lindenmuth: Each of the various processes are automated from pumping the water from the well and/or canal to filters that feed tanks that eventually pump the water into the boilers and other areas of manufacturing to the individual machines and then back through the recycling systems and fire pond.
FE: What process/facility changes made a specific improvement on cash flow?
Lindenmuth: We use less water, less energy (gas and electric). The water is cleaner, which results in higher quality finished products at a lower weight, higher density, higher volume and the end result of lower costs.
FE: California has some of the toughest environmental laws. How did you manage conformity to them?
Lindenmuth: We have always conformed with environmental laws. They may be tougher in California; however, we have been in business here since 1973 and as those rules developed and evolved over the years we have made investments in equipment and process that ensure our adherence to good practices and result in good quality products.
FE: Are there any takeaways that you have for our readers, food and beverage manufacturers?
Lindenmuth: Europe has been particularly tough over the years on EPS foam. Recently they came out with a statement that EPS does some things better than other packaging products and that they now want to focus more on good recycling practices. Food and beverage manufacturers and grocery chains, please communicate as a group to see what others are doing in the area of recycling.
About Richard Lindenmuth
Richard (Dick) Lindenmuth is president and CEO of Styrotek, a California-based company that designs and manufactures EPS packaging for table grapes as well as other food businesses and the pharmaceutical industry. He navigated Styrotek’s successful turnaround.
Lindenmuth is recognized for his execution skills in high-growth and distressed environments. He has been a corporate performance advisor and CEO in companies ranging from high-technology and services to heavy- and basic-industries. He has more than 30 years domestic and international management experience working in Korea and 10 years in the Middle East.
Lindenmuth is author of The Outside the Box Executive. He is chairman of the advisory board of InterimExecs, a group of C-level executives specializing in growing and transforming companies.
Lindenmuth earned his MBA at the Wharton School and is a veteran of the U.S. Navy.
Looking for a reprint of this article?
From high-res PDFs to custom plaques, order your copy today!