Engineering R&D
Novel compressed air drying system leaves out the desiccant
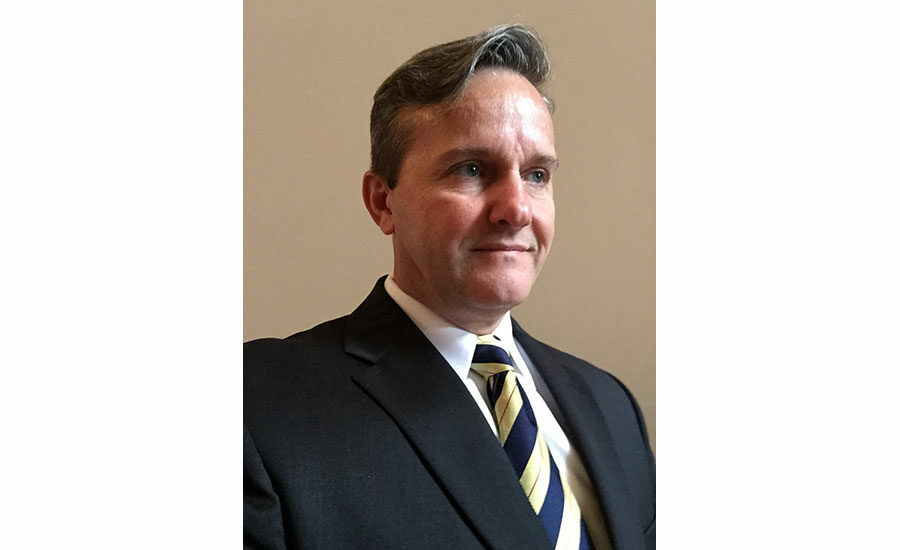
Kelly Campbell, global product manager for Ingersoll Rand.
Photos courtesy of Ingersoll Rand

Ingersoll Rand’s Subfreezing Dryer supports ISO Class 3 air with a PDP of -20°C (-4°F), and uses no desiccants.


Typically, in food applications where compressed air may come in direct contact with food, regenerative desiccant dryers are able to dry the air to ISO 8573 Class 1-2 requirements, or a pressure dew point (PDP) as low as -70°C (-94°F) for Class 1. However, for less stringent food applications, ISO Class 3 air with a PDP of -20°C (-4°F) may be sufficient.
For these latter applications, a new approach, a subfreezing dryer, was explored and executed by Ingersoll Rand. The new design, which the company calls the Subfreezing Dryer, currently handles flows up to 250 cfm with plans to expand to 1,100 cfm.
Previously, desiccant dryers provided the only means to achieve a -20°C PDP or better. In fact, Ingersoll’s own literature previously called out desiccant dryers for Class 3 applications: “Processes that require ultra-dry air (ISO Class 1, 2 or 3) will need an advanced solution using non-refrigerated dryer technology.” Now Class 3 can be achieved with subfreezing technology that eliminates the need for desiccant.
The company began developing the technology in 2015 at its Fogliano, Italy factory. If this dryer fits your application, you can expect to achieve a lower cost of ownership than traditional regenerative desiccant dryers with reduced energy and maintenance costs, according to Kelly Campbell, global product manager—refrigerant dryers at Ingersoll Rand Compression Technologies and Services.
I spoke with Campbell to see how this dryer may fit into food applications.
FE: What food/beverage applications would be suited to Class 3-rated air? Would certain applications be suited to Class 1 particulates, but Class 3 PDP dry air would be satisfactory?
Campbell: The Subfreezing Dryer technology is suitable for a wide variety of applications that require very dry compressed air like in the food and beverage industry. Sometimes it’s the application itself that dictates the ISO Classification for cleanliness (moisture, oil, particulates), for example, using compressed air to convey corn chips through a pipe across a plant. These applications usually require oil-free compressors along with a low dew point dryer. Other times it’s the environment that dictates the need for a low-pressure dew point. An example of this would be compressed air piping exposed to very low temperatures where any liquid moisture can freeze, causing a blockage. In these cases, oil-flooded compressors are usually suitable. The Subfreezing Dryer is fully compatible with all compressor types with a simple plug and play installation and thus suitable for both situations.
FE: How does the technology work?
Campbell: The easiest way to relate to this new Subfreezing technology is to think of it as a combination of a regenerative desiccant dryer, a heat-of-compression dryer and a refrigerated dryer. In other words, taking the best parts of these three dryer types and combining them. First and foremost, it is a regenerative dryer. This is what allows us to achieve the subfreezing -4 degrees Fahrenheit pressure dew point. The Subfreezing Dryer has two drying chambers. The first is drying the air, while the other regenerates and removes stored moisture. After some time, the airflow path switches, so the freshly regenerated chamber dries while the other regenerates.
Secondly, it is a heat-of-compression (HOC) dryer in that it uses the heat from the compressor as the energy source to regenerate without wasting any compressed air through purging compressed air. This is why the Subfreezing Dryer is highly efficient and consumes so little energy.
Last, the Subfreezing Dryer is a refrigerated dryer in that it uses refrigerant to dry instead of desiccant, and this is why the maintenance cost for the Subfreezing Dryer is so low, why it is fully compatible with all compressor types and why it is so compacted.
FE: What is the dryer’s footprint compared to other technologies?
Campbell: The Subfreezing Dryer has a significantly smaller footprint compared to other regenerative dryer technologies that require desiccant filled pressure vessels. The footprint can be up to 40% smaller depending on the model.
FE: Where do you locate it in the compressed air chain? Is it easy to install?
Campbell: Just like other types of dryers, the Subfreezing Dryer is located downstream of the compressor. It is a plug-and-play solution with no special insulation, modifications or adjustments required. You can simply pipe it into any compressor type and turn it on. It’s that easy.
FE: Why is this technology more efficient than regenerative desiccant?
Campbell: The Subfreezing Dryer is more efficient because it does not require heaters, blowers or purging of compressed air found in typical regenerative desiccant dryers.
FE: Are there any consumable materials or parts in the SF dryer?
Campbell: Because the Subfreezing Dryer uses refrigerant instead of desiccant, there are no routine consumables that need replacement.
FE: Is the unit totally sealed like a refrigerator?
Campbell: The Subfreezing Dryer uses R452A refrigerant that has a very low Global Warming Potential (GWP) in a hermetically sealed circuit that is very environmentally friendly.
FE: What are its advantages/disadvantages when compared to regenerative desiccant technology or other types? I understand that desiccant dryers actually purge air into the environment. What about SF technology?
Campbell: The advantages are energy savings, lower maintenance costs, lower noise levels and a smaller footprint. The one disadvantage is that the Subfreezing Dryer is limited to -4 degrees Fahrenheit pressure dew point, which is sufficient for most applications, but for those special applications that require -40- or -100-degrees Fahrenheit then a traditional regenerative dryer is the better solution.
FE: How does its cost compare to regenerative desiccant systems?
Campbell: The cost to operate the Subfreezing Dryer is significantly less in both energy and maintenance, and its initial purchase price is comparable to that of a regenerative desiccant dryer with an external heater.
FE: Do you see this technology working at even lower PDPs than -20°C PDP?
Campbell: The Subfreezing Dryer technology was specifically developed for ISO Class 3 (-20 degrees Celsius). At this time, Ingersoll Rand is focused on development within this Class.
FE: What kind of controls does it have? Does it integrate into an air system seamlessly?
Campbell: It uses an advanced microprocessor controller with a color display that continuously monitors the health of the dryer, makes adjustments as needed and alarms the user as needed of any issues.
FE: What about reliability?
Campbell: We incorporated reliability into every aspect of this dryer to ensure that the customer not only saves money on energy and maintenance but that they also have an incredible experience throughout the life of the dryer. For example, we have a robust smart drain built into the dryer to remove condensation from the air system that is operated by the dryer’s controller. When it senses clogging, a rapid cycling event initiates to clear the clog. If the clog cannot be self-corrected, then an alarm is displayed to warn the user.
For more information, visit www.IngersollRandCompressor.com
Looking for a reprint of this article?
From high-res PDFs to custom plaques, order your copy today!