Cover Story
Cold Storage Construction and COVID-19
How the pandemic is transforming new-build and renovation projects in 2020.

Editor's note: This article was originally published in the September 2020 issue of Refrigerated & Frozen Foods.
Looking back on what we’ll call 2020 B.C. (Before Coronavirus), the pipeline for cold storage construction was already robust and healthy. According to research by commercial real estate firm CBRE, overall industrial construction—which encompasses cold storage, along with warehouses, distribution centers, manufacturing facilities, self-storage, office and flex space—was at 298 million square feet (MSF) before COVID-19, bolstered by the ongoing rise of e-commerce.
In March, when the pandemic pushed demand for cold foods and other goods in retail and direct-to-consumer channels to astronomic levels, overall industrial construction bumped up to 309.7 MSF, with 36% of that space pre-leased, and an all-time low vacancy rate at 4.7%. Net absorption of occupied warehouse and distribution space in particular—where cold storage resides—was at 70 million additional square feet by the end of Q2.
Increased demand for space has also raised rents to record levels. The average asking rent for industrial space in Q2 was at $7.96 per square foot, which is 6.3% higher than last year. Warehouse and distribution rents, which includes cold storage, rose 5.6% year-over-year to an average of $6.68 per square foot.
There was a slight dip in overall industrial square footage in April (down to 298 MSF due to projects put on hold because of quarantine) but once construction sites opened again, that number went up to 313 MSF.
While the figures above provide a bird’s-eye view of how COVID-19 has impacted large-scale industrial and cold storage construction this year, we need the ground-level perspective from those working on active projects to see the full picture. We spoke with several top design-build and construction firms about how the pandemic has affected their business, what areas within their projects are being modified for coronavirus, and how they envision cold storage construction evolving in 2021 and beyond.
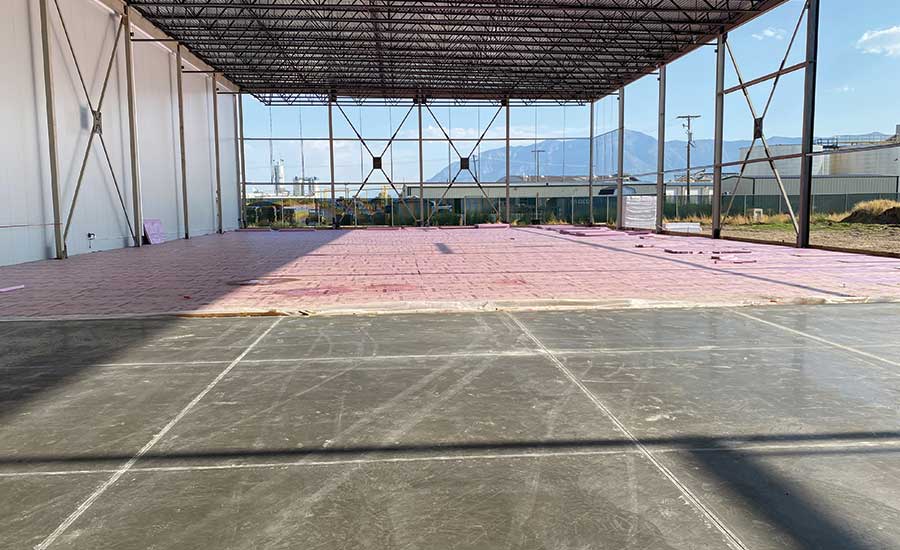
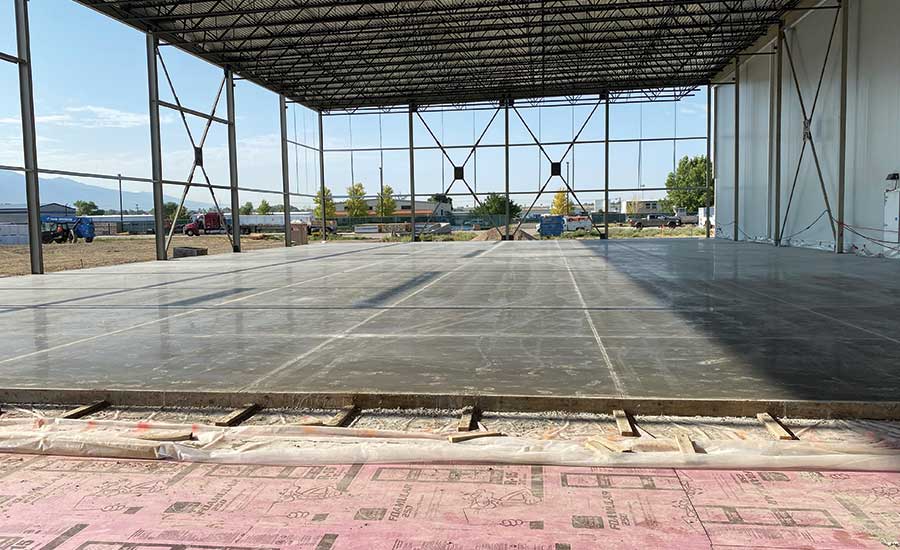
Recent work on a cold storage warehouse for GSL Brine Shrimp in Ogden, Utah, by Big-D Construction.
Worksite Changes
Construction teams have to set up their own field logistics in and around a worksite for a job to be finished efficiently and on time. Before COVID-19, that was relatively routine, but this year, extra safety precautions are being taken which can require more steps for crews to follow on a day-to-day basis, and also takes additional time to execute.
“We have had to spend time every day on projects to train and educate our onsite leadership teams and field personnel about the newest information regarding COVID-19 and CDC guidelines, and any new best practices being implemented by our organization and our project teams,” says Forrest McNabb, president of Big-D Construction in Ogden, Utah. “It requires continual training and accountability in order to keep our projects safe, clean and all of the workers out of harm’s way. We’ve created washing and sanitizing stations throughout our project sites, and have taken some meetings out of project trailers to the interior of the building or outside to allow proper social distancing.”
Dan Crist, VP of operations at Charlotte-based A M King, adds that they’ve “implemented new safety signage on all projects. Our renovations include separate, dedicated entrances and egress access and strict sanitation guidelines within the areas of construction. Working within existing facilities must include plans to segregate construction crews from facility employees. Renovation and expansion projects have proven to be more complicated than greenfield projects as we must consider the impacts of COVID-19 not only with the construction team but also the client’s employees.”
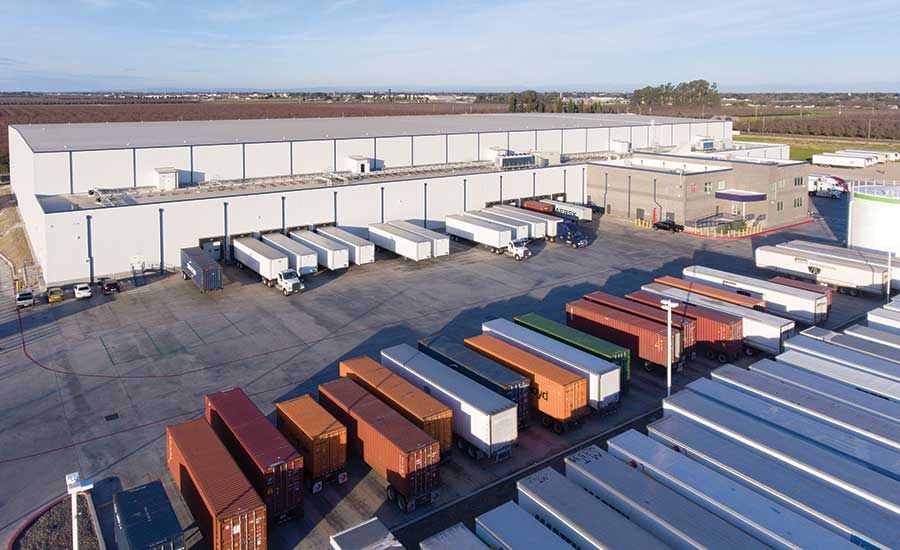
Cold storage facility in Turlock, California, built by Fisher Construction Group
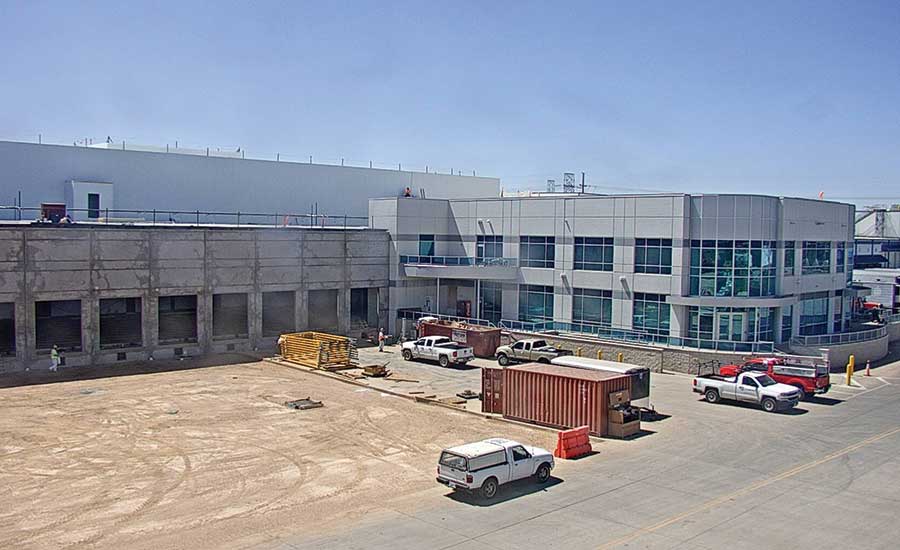
200,000-square-foot freezer expansion of a warehouse in Syracuse, Utah, by Big-D Construction.
Multi-layered changes to worksite safety are also happening on projects by the Tippmann Group, based in Fort Wayne, Indiana. “We’ve completely changed how subcontractors and visitors check-in to our job site, and we’re performing daily health screenings and temperature checks for all who enter the job site. Our trailers are now restricted to only Tippmann Construction employees, and our weekly scheduling and safety meetings are all done virtually. We’ve also updated our safety materials and videos to include CDC guidelines as they relate to COVID-19 safety, and we’ve added additional onsite trailers to keep contractors and our customers physically separated to restrict direct interaction,” explains Steve Tippmann, EVP at Tippmann Group.
Tyson Foods’ case-ready beef and pork processing/packaging/cold storage/distribution center in Eagle Mountain, Utah, built by Big-D Construction on a greenfield site.
Project Modifications
Most cold storage construction projects in 2020—whether it’s a new-build or renovation—are now viewed through the lens of COVID-19, with modifications for employee safety and social distancing in high-traffic areas.
“There’s greater focus on employee welfare areas to help keep warehouse workers safe. This includes more hygienic HVAC measures, employee flow into and out of areas, breakroom layouts to better accommodate social distancing and additional locations for wash stations,” Crist says.
Areas where drivers check in and out are also being transformed due to the pandemic. “For drivers, we had been moving to larger welcome center designs already, but with COVID-19, we developed ways to minimize physical interaction, and moved to a texting and electronic BOL interchange format that works almost universally for all drivers,” says Tippmann. “For employee interaction, we had to rethink and redesign areas where people used to congregate and would have a lot of interaction with their co-workers. This includes locker rooms, break rooms and conference rooms, among others.” Tippmann adds that employee check-in areas have also changed to make room for daily health screenings.
Workers from Big-D Construction building a temperature-controlled facility for alternative-dairy company Oatly in Ogden, Utah
Other design changes this year include an emphasis on contactless environments. “There has been an increase in remodel enhancements to providing touch-free operational items like light fixtures and doors. All of these projects provide even higher sanitation excellence every day regardless of the pandemic,” notes McNabb.
All of the firms we talked to say the changes detailed above for cold storage are here to stay for the foreseeable future, and some of the modifications, like additional flexible space and contactless environments, were already trending before the pandemic, but are now accelerated. Temperature-controlled environments that combine social distancing with technology and automation will increase as well, particularly in cold foods processing facilities where staff traditionally work side-by-side, and in high-volume warehouses where inventory is coming and going at a rapid rate.
“We’ll see an extension of processing lines to provide spacing between workers. COVID-19 will likely lead to a much greater focus on automation to allow for fewer workers in the facilities,” Crist says.
Panic buying of retail foods in March and April taught cold storage operators that “it’s more important than ever to have enough product to meet demand in case of shortages,” says David Scotti, owner and president of Inspired Technology Systems. “Opportunistic investors would see this as a reason to expand to bigger frozen storage facilities and capabilities. Ensuring that this increase in supply does not require increasing personnel is very relevant. Doubling your facilities should not require doubling your personnel. Newer automated processes should be used to guide the picker to what pallet or inventory to ship out first, while the order taker is given the option to override the system’s suggestion based off a customer request.”
Cold storage expansion project for Lineage Logistics in Stevens Point, Wisconsin, built by Tippmann Group.
Construction Locations
According to CBRE, the top-five industrial construction markets at the end of 2019 with the highest demand for new space are near major logistics hubs. Kansas City had the lowest vacancy rate for 2019 construction completions at 7.3%, with Miami (12.4%), Baltimore (13%), Greenville, South Carolina (18.7%), and New Jersey (22%) next. Dallas/Fort Worth was the best-performing core market last year with almost 75% of its 25 million square feet in new completions already leased.
Warehouse construction near major logistics hubs is especially important in 2020, since speedy last-mile delivery has become a priority and expectation due to the collision of COVID-19 and e-commerce/direct-to-consumer shopping. The additional space required in major markets means building in nearby submarkets to handle demand and improve logistics. At the end of 2019, for example, the top-five submarkets were located in north Fort Worth, northeast and south Atlanta, Ontario, California, and southeast Houston.
“Our design and construction teams working in last-mile food distribution have been very busy,” says Ginny Bode, marketing director at Fisher Construction Group in Burlington, Washington. “For temperature-controlled environments, the demand is high and we continue to be cautiously optimistic for 2021.”
Fisher’s VP of Architecture and Engineering, Troy McOmber, adds that “uncertainty in the marketplace causes owners to hedge when they contemplate their needs 12 to 16 months in the future—the time it takes to bring a facility online. The COVID-19 crisis complicates that further because of the uncertainty of a vaccine or reverting back to stay-at-home orders. Remarkably, we’ve seen only a slight softening in the food processing market while cold storage remains robust, as is the case with most logistics-based businesses.”
View from above of Fisher Construction Group’s 241,751-square-foot cold storage project in Turlock, California.
That cautious optimism Fisher has for 2021 is in line with what we heard from other firms, as they all continue to navigate around COVID-19 concerns and keep projects on schedule. For now, virtual groundbreakings and digital submissions of blueprints for approval, for example, will continue, but the actual project work of building and renovating cold storage and cold foods processing facilities shows little sign of slowing down.
“We’ve experienced increased opportunities in 2020, specifically in the food distribution and cold storage sector. Many of our clients have expedited projects to keep up with consumer demands, while some have paused projects to evaluate how to properly plan and retool facilities to address COVID-19,” says Crist, while Tippmann concludes that 2020 has been “a very busy year for us. COVID-19 has led to increased activity in the food industry, especially on the warehousing side, as vendors began to realize they may not have been properly stocked up on product. It has also led to more activity on the construction side, with both expansions and new opportunities as food companies are increasing production in order to meet heightened demand and growth.”
One of two rooftop refrigeration units installed at Fisher Construction Group’s cold storage project in Turlock, California.
Looking further ahead, McNabb says the uncertainty of COVID-19 is an ongoing concern when forecasting for 2021 and 2022, while historically, years ending with an election, like 2020, “typically provide a bit of a blip on the construction radar overall.” Still, he says Big-D Construction is adapting well to the unforeseen acceleration in all aspects of their business.
“We’re all navigating unchartered territory. It’s the first time in my career that short-term planning went from a one-to-three-year analysis to a day-by-day, week-by-week review of impacts or potential impacts due to the pandemic.”
(For more about cold storage construction and COVID-19, be sure to register for the AFFI's Supply Chain Solutions Summit, a one-day virtual conference on 9/23, featuring a session with representatives from Big-D Construction, Tippmann Group, and Fisher Construction Group, moderated by R&FF's Michael Costa.)
Long-Term Effects of COVID-19 on Cold Storage Construction
According to research by commercial real estate firm CBRE, the long-term effects of COVID-19 will change the cold storage sector in five crucial ways:
1. E-commerce grocery will become more widely adopted. Given the increase in online grocery shopping, there will be heightened demand for cold storage capacity; however, the volume of perishable orders will need to grow in order to have a significant impact on cold storage real estate decisions. In general, there is a recent consumption trend toward food that drives demand for temperature-controlled space, like frozen meat and processed poultry. Until recently, consumers were not ordering a lot of perishables online, but that likely will change in a post-COVID-19 environment.
2. Since e-commerce is typically fulfilled by local grocery stores, retail footprints will include more storage and fulfillment space. As online orders rise, there will be a blending of retail and industrial space, as well as a greater need for infill temperature-controlled facilities in proximity to consumers. Space requirements will vary among food retailers, but additional modern space likely will be needed considering that the average age of cold storage warehouses is 34 years.
3. Restaurants may see a significant shift in dining formats with less dine-in options and more delivery or take-out that would require cold storage capacity. Foodservice companies that supply restaurants may look to second-generation cold storage space as a cost advantage in a limited dining environment.
4. There will be further consolidation among major PRWs to gain more control over the cold storage footprint in the U.S. This will lead to specialized development in major metros where large cold storage operators will partner with developers to strategically build a network in proximity to population clusters.
5. Automation will increase in cold storage facilities to efficiently fulfill orders and make up for a shortage of workers willing to work in the extreme conditions of these facilities. This will prompt higher-density, greater-height and smaller-footprint buildouts that will be required for around-the-clock operations.
Looking for a reprint of this article?
From high-res PDFs to custom plaques, order your copy today!