Track and Trace
Food Waste Mitigation via Transportation

Photo by Sara Stasi on Unsplash
It is estimated that 1.3 billion metric tons of food are lost or wasted annually, translating to a financial loss of $1 trillion (USD) annually. And without significant changes, this problem is expected to grow to 2.1 billion metric tons and $1.5 trillion (USD) by 2030.
Staggering as these numbers might be, they do not consider the hidden costs of food production, including labor, storage and salvage or the expenses related to customer dissatisfaction, lost opportunities and inventory/stocking level imprecision.
Shockingly, one-third of all food produced for human consumption is lost due to wastage, which has significant financial and environmental and social implications.
The commodities with the highest level of waste are:
- Fruits and vegetables (45%)— equivalent to 3.7 trillion apples
- Roots and tubers (45%) – equivalent to 1 billion bags of potatoes
- Fish and seafood (35%) – equivalent to 3 billion Atlantic salmon
- Meat (20%) – equivalent to 75 million cows
Food waste and loss are pervasive throughout the food value chain—"from farm to fork." A sensitive, temperature- and climate-controlled commodity, fresh and frozen food is vulnerable to spoiling from the beginning of processing to the finished product. Harvesting, manufacturing, packaging, transporting a stock rotation, and the consumers’ tendency to overbuy contribute to excessive waste and spoilage.
While many variables impact wastage, approximately 7-15% happens during transport. The fact that 10,000 shipping containers go missing yearly contributes to the situation. However, a more common problem relates to temperature control or refrigeration issues during transport—affecting the integrity of the food—making it unacceptable for human consumption. In fact, in the U.S., one-half of all fresh produce is lost due to suboptimal shipping conditions.
SeaCube recognizes the importance of effective equipment and technology to mitigate perishable wastage during transport. SeaCube is investing in a telematics technology solution in collaboration with Carrier. Every Carrier reefer in the SeaCube fleet will be equipped with the Carrier Lynx Fleet Management solution, which will provide enhanced visibility to show where the container is, how it is performing and what is happening inside the container.
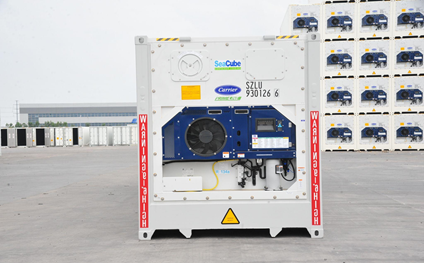
The Carrier Lynx Fleet solution includes proprietary technology that monitors reefer unit performance and provides early warnings, actionable diagnostics and predictive analytics down to the level of the machine’s components. SeaCube chose this system because it provides more detailed machine performance analysis capabilities than other telematics platforms. Lynx Fleet will offer prognostics and data analytics on Carrier and non-Carrier equipment with features that give such differentiation as improved fleet uptime, operational costs and incremental value through lower cargo spoilage.
Telematics technology in the intermodal supply chain allows for greater collaboration, increased transparency and real-time information on the location and inside temperature of a container. Software using advanced algorithms provides notification of any significant events on the route and predictive analysis that enables maintenance and repair planning before an event occurs.
Some food wastage is inevitable, but it is a company’s responsibility to utilize available technology to reduce waste and ensure perishables make it to their destination intact. Safeguarding this critical cargo's integrity helps clients satisfy their customers while protecting the environment and helping to keep the world’s population fed.
Looking for a reprint of this article?
From high-res PDFs to custom plaques, order your copy today!