The average factory electricity bill varies across the manufacturing industry. The dairy industry hovers around 5% to 8%, and breweries cite 5% to 10% of their operating costs on energy. Factory electricity bills for meat processors can reach 15%, and the sugar industry touches 30%.
However, food and beverage manufacturers are targeting energy, water and material consumption as they invest in automation tools, system software and modern processing equipment. The upshot of these digital plant investments is that companies are discovering inefficiencies and paths to continuous reductions in plant resources due to actionable plant data.
Operators have been adding equipment sensors and “quick-win” automation tools to produce more actionable data, while management is going big with evaluations of energy management systems. "Advances in instrumentation by various manufacturers have significantly enhanced data collection and analysis," says Tim Barthel, executive vice president at Cybertrol Engineering. "Modern systems now offer far more data than what was realized from an analog signal just four years ago."
Cybertrol Engineering, a full-service control system integrator and certified member of the Control System Integrators Association (CSIA), offers a configurable clean-in-place (CIP) solution that allows users to define and adjust cleaning parameters like flow rates, temperatures, chemicals and duration, and optimizing the process for various equipment via real-time monitoring.
According to the U.S. Energy Information Administration (EIA), the food and beverage manufacturing industry is one of the most energy-intensive manufacturing sectors in the country, accounting for approximately 8% of the total energy consumed by all manufacturers.
"Many companies are moving beyond legacy controls, which have limitations in capabilities, and toward newer, more advanced technologies," says Barthel. "These advancements not only improve the reliability and performance of CIP systems but also demonstrate measurable return-on-investment (ROI) through increased productivity and reduced downtime."
Many manufacturers also move beyond legacy controls and add new processing machinery to reduce energy costs and improve efficiencies. Handtmann, a supplier of a range of food processing equipment, offers smart OEM digital solutions that tackle specific applications. The company’s equipment offerings include the entire process line.
For Handtmann, servo motors are a part of its equipment designs. "Energy efficiency is one of the biggest talking points when it comes to purchasing," says Shawn Kentch, training manager at Handtmann. "Some suppliers have not switched to servos, and this type of motor is much more efficient than an asynchronous motor."
Handtmann's machinery uses advanced automation to produce controlled temperatures, integrated movements and continuous monitoring. The company's vacuum filling machines can limit product giveaways to less than 5 lbs. in a 10-ton production run and result in $144,000 in annual savings.
Proof-of-Technology Projects Save Money
A German cheese producer, Milchverwertung Ostallgäu (MVO), relies on advanced instrumentation and a turnkey solution from Endress+Hauser called the Steam and Water Analysis System (SWAS). The German cheese and butter producer processes more than 140,000,000 kg of milk annually, and water is treated at the plant's sewage treatment plant. The entire staff includes 45 employees.
Before acquiring the SWAS instrumentation, the company relied on manual readings of the boiler for pH or conductivity and created additional maintenance logs since these readings are required by law. The automated SWAS technology tracks quality-related water parameters within the boiler system and uses a compact panel to help operators gauge these levels.
At MVO, the SWAS panel includes:
- Sample cooler
- Pressure reducing valve
- Electrical temperature protection valve
- Overflow valve
- Flow assembly and Memosens sensors for conductivity and pH
- Liquiline transmitter
- Flow measurement
- EcoGraph T RSG35 recorder for paperless data recording of the measured values is mounted on the panel
The turnkey system can analyze the following parameters: pH/ORP, dissolved oxygen, conductivity (total, cationic/acid, differential), turbidity and total organic carbon (TOC). "We have been able to significantly increase operational reliability and meet our verification obligations with less effort," says Simon Gutensohn, managing director of Milchverwertung Ostallgäu.
“By focusing on proof-of-technology, companies can better allocate their resources, including labor, materials and capital, ensuring that only the most promising technologies move forward to larger-scale implementation,” says John Tertin, director of solutions engineering at Cybertrol Engineering.
Survey says you need Industry 4.0 before AI: "Regarding the role of #AI in predictive maintenance (#PdM), only 8% of those surveyed are currently operating a PdM strategy. However, 76.5% want to shift to PdM in the future."
In addition to turnkey solutions, original equipment manufacturers (OEMs) are adding features to reduce water and material consumption. Vanmark’s skid-mounted peeler machinery—for potatoes, apples, beets and more—reduces water consumption with its reclamation system that recirculates processed water.

"Water usage is a major consideration, and usage can be expensive," says Mike Barber, sales manager at Vanmark. "Customers are concerned, but potato processing requires water, so it's about conserving the freshwater used." Vanmark's machine equipment removes peel waste from process water, collects it for sale and recirculates filtered water back into the peeler in a closed loop. Then, the filtered water from the settling tank is pumped back to the infeed end of the spray bar system at each peeler.
Freshwater consumption per peeler is reduced to 0.5 to 2 gal./thousand (GPM) during regular operation. The recycled water is drained and flushed periodically. Moreover, the OEM also offers an option via its system starch separator for its line of Lamina Hydrocutting equipment. According to Vanmark, traditional potato processing includes 2% of water being bled out and is continuously replaced with clean water. The supplier's system starch separator creates a cyclone in the line that pushes the starchiest water to the pipe's edge and removes the water. This new feature reduces water consumption for the "bleeding process" while providing the right level of cleaning.
Brau Union Scales Energy Management System
As factory electricity bills increase, countries are working with industries to reduce demand and increase utilization at the plant level. According to the U.S. Energy Information Administration (EIA), the food and beverage manufacturing industry is one of the most energy-intensive manufacturing sectors in the country, accounting for approximately 8% of the total energy consumed by all manufacturers.
One solution to reduce electricity demand at plants is adding energy management platforms that are tied into automation in the plant. Capturing energy usage from equipment, processing operations and other applications allows large food and beverage companies to find substantial reduction in energy bills. Siemens’ new white paper “Energy Data Management in the Food and Beverage Industry,” explains the components, industry drivers and how to integrate real-time data into machines and automatically record and evaluate energy requirements. Siemens’ offerings include the SIMATIC Energy Manager and the S7 Energy Efficiency Monitoring interface that connects to the cloud-based Insights Hub, which is part of the Xcelerator business platform.

Brau Union, the parent company of Heineken, has been focusing on energy efficiency for decades. The brewer recently rolled out a proof-of-technology project that automatically records and evaluates all media and energy flows from six brewing sites. This ambitious project started by identifying approximately 1,000 measure points throughout the first five sites.
To acquire this energy data, low-voltage main distribution boards are retrofitted with SENTRON PAC 3200 power meters. These values are acquired by the Energy Manager in 15-minute cycles via Modbus/TCP networking to match the data intervals of the power utilities’ energy data acquisition. “If we later see a roll out at other sites, they can be seamlessly and easily integrated due to the scalable program layout of the SIMATIC Energy Manager PRO," says Johann Hölzl, head of process automation at Brau Union Austria.
In addition, batch processing data from the plants’ SIMATIC IT manufacturing execution system (MES) is also read by the energy management system for evaluation.
While batch processing energy usage at Brau Union is connected via controllers, other non-connected meters need traditional manual maintenance checks at the breweries. The Siemens energy manager app for iOS and Android allows maintenance to record energy consumption data from meters not connected to the energy data management system. Operators use the app to record energy data and transfer it to the central data management system. To do this, they simply scan the QR or barcode of the corresponding meter, enter the current reading into the smartphone and then SIMATIC Energy Manager displays the value.
The Austrian Wieselburg brewery is the first to implement the scalable energy solution and reduced its annual energy consumption by 0.6% in its first year.
This platform approach also allows food and beverage manufacturers to zoom out and understand possible capital expansion needs at plant sites. With growth comes capital expenditures on infrastructure like cabling, pipelines and supply systems. However, companies may not need to expand infrastructure if there is unused capacity, according to Siemens.
A 2% reduction in energy usage for U.S. food and beverage manufacturers would result in $180 million in annual savings.
General Mills Cracks Energy Savings
As companies began to address systematic energy usage, General Mills has improved energy usage across 26 U.S. manufacturing sites from 2012 to 2018. The company launched this energy savings leadership position by participating in the Department of Energy’s Better Plants Challenge. For the first six years, the company improved energy usage by 2 MMBTUS and saved more than $5 milion at its 26 plants.
Recently, General Mills worked with ThinkIQ and used its machine learning algorithms to forecast a savings of $480,000 annually with the food and beverage giant’s energy bills. ThinkIQ’s software as a service (SaaS) platform identifies and forecasts “blind spots” within manufacturing sites by implementing an informational model to capture data, visualize plant applications and promote machine learning.
“An information model brings a standardized approach to what the data should look like and ensures all constituents benefit and go to one place (for the data),” says Rob Schoenthaler, chief revenue officer at ThinkIQ in a June 2024 Food Engineering article.
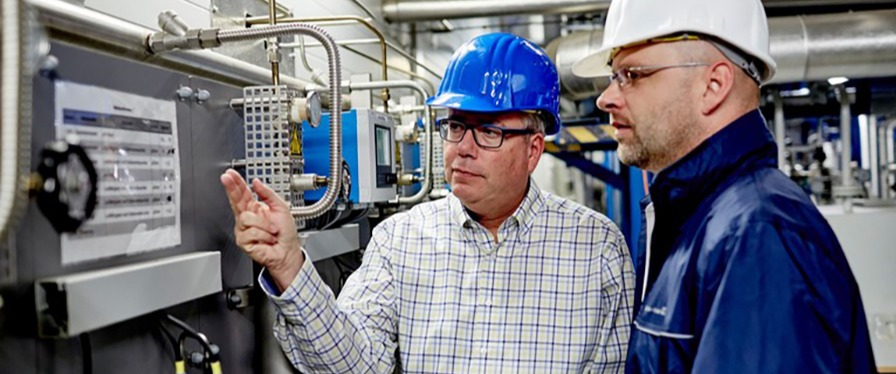
For this energy modeling project at General Mills, ThinkIQ created and applied new data modeling and analytics to quickly point out energy savings opportunities by identifying periods of high energy consumption.
Below are the components for the modeling at General Mills:
- Equipment and process energy models for a generic factory environment
- Pump SM profile
- Mixer SM profile
- Tank SM profile
- Python based machine learning predictive tools for power consumption and estimating energy usage at equipment and plant level
- Energy management tools for the CESMII SMIP
The data capture and visualization targeted common equipment, such as motors, drives and packaging equipment while building a user interface to enable users to build energy consumption models. The SaaS tools produced visualization for unknown energy consumption and deviations from baselines in the plant. The results of this project included an expected 2% reduction in energy utilization when General Mills’ Chanhassen plant implements these smart manufacturing tools.
ThinkIQ also licenses its technology to the Clean Energy Smart Manufacturing Institute (CESMII), which promotes adoption of Industry 4.0.