Food Safety
Make a commitment to educate your workforce
By properly educating staff and providing adequate resources to do this, a company protects its workforce, reputation, resources and itself.
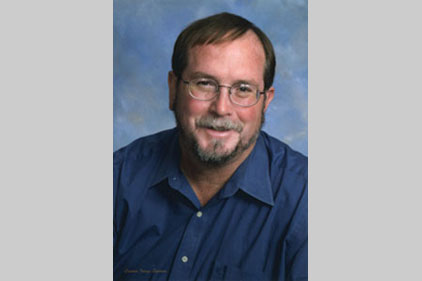
Everybody knows Murphy’s Law: Anything that can go wrong will go wrong. Anyone who works in the food industry knows this law applies. Strange and unexpected things can happen, so it is important for food manufacturers to learn from such mistakes or, better yet, work to keep them from happening in the first place. One way to keep Murphy from your door is through education. Make a commitment to allocate the resources and time to ensure staff members know not only how to their jobs but also how to do their jobs safely. Please note that the term education, and not training, is used. That’s because there is a difference. Training implies learning things by rote and not understanding why they have meaning. Staff needs to know how to do a task—and why it is important.
With a food safety management system or HACCP program, staff assigned to the task of monitoring critical control points should:
- Be properly educated in CCP monitoring techniques
- Fully understand the importance of CCP monitoring
- Have ready access to the monitoring activity
- Accurately report each monitoring activity
- Immediately report critical limit infractions so immediate corrective actions can be taken
- Understand the corrective and/or preventive actions that must be taken.
The same philosophy that is applied to ensure workers understand how to monitor critical control points should be included in the educational programs for every position in a food processing facility. In addition, management must develop, document and implement programs, such as tests and practicums, which will allow it to measure whether the educational process has been effective. But conducting educational programs is not enough; food and beverage manufacturers must also document that the programs were completed.
The educational process starts when a new employee walks through the front door. Along with addressing basic employment issues, the orientation session should encompass plant requirements for food safety, quality, sanitation, personal hygiene, worker safety, food defense and crisis management. Developing, documenting, implementing and maintaining these programs will help keep Murphy from your facility. They also address another key issue in today’s world of food processing: the demands of third-party audits.
A basic expectation in almost all third-party audits is that plant workers and management have received education based on documented procedures and work instructions. Companies that do not fully document what is required and rely on verbal instruction are asking for trouble. For example, when giving a new employee an assignment without a reference to a documented procedure, the mentor may forget something or teach the new hire how he or she does it, which may be wrong.
Take the time to fully educate people in all aspects of food plant operation, from receiving to shipping to grounds maintenance. Also address safety issues such as correct lifting techniques and how to properly maintain and use personal protective equipment.
By properly educating staff and providing the resources to do this, you can protect your company, as well as its workforce, reputation and resources.
Looking for a reprint of this article?
From high-res PDFs to custom plaques, order your copy today!