TECH FLASH
Robotic advancements to surge in manufacturing productivity
The new wave of industrial robots is near a point of takeoff that could boost productivity for many food and beverage manufacturers.
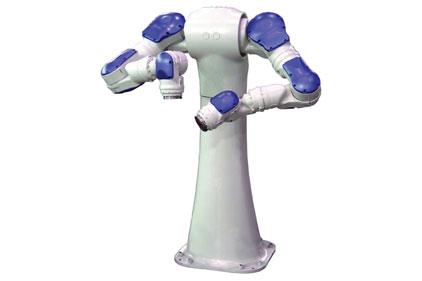
If they weren’t before, human factory employees may soon be considered an endangered species, as manufacturing companies adopt advanced robots that will power the next productivity surge in the industry.
According to new research by the Boston Consulting Group (BCG), by 2025, these new robots will boost productivity by up to 30 percent in many industries and lower the total cost of labor by 18 percent or more in countries like the US, South Korea, China, Japan and Germany. Estimates by BCG project the investments in industrial robots to accelerate, bringing an annual growth rate for robot investments that currently hovers around 2 to 3 percent up to 10 percent.
By 2025, labor costs are projected to be 18 to 33 percent lower in countries such as the US and China, which are at the forefront of robotic deployments. Specifically, BCG says a greater use of automation in China could compensate for a major part of the loss in cost competitiveness that is expected as a result of rising wages and the challenge of finding workers. On the opposite side, countries like France, Italy, Belgium and Brazil will likely see their manufacturing competitiveness fall because of a projected lag in robotic investments.
“As labor costs rise around the world, it is becoming increasingly critical that manufacturers rapidly take steps to improve their output per worker to stay competitive,” says Harold Sirkin, a BCG senior partner and coauthor of the firm’s series on the shifting economics of global manufacturing. “Companies are finding that advances in robotics and other manufacturing technologies offer some of the best opportunities to sharply improve productivity.”
According to BCG, robots currently perform only 10 percent of manufacturing tasks, despite years of their being used and the investments made in advancements. But by 2025, BCG estimates, the portion of “automatable tasks” performed by robots will be near 25 percent for all manufacturing industries worldwide.
So why will robotic investments take off at such a rapid pace in the next decade? Researchers say it is because of a number of forces that include performance improvements and a decline in cost.
According to BCG, advances in vision sensors, gripping systems and information technology are driving these improvements in performance, making robots smarter, highly networked and immensely more useful in a wider range of applications.
“For many manufacturers, the biggest reasons for not replacing workers with robots have been pure economics and technical limitations,” says Michael Zinser, a BCG partner who co-leads the firm’s manufacturing practice. “But the price and performance of automation are improving rapidly. Within five to 10 years, the business case for robots in most industries will be compelling, even for many small and mid-sized manufacturers.”
The adoption of these robotic advancements will vary by industry, however, with the transportation, computers and electronics industries leading the way. The food industry will adopt these automated advancements at a slower pace because many of its tasks remain difficult to automate, and wages are relatively low, according to BCG.
“Regardless of whether they’re ready to invest in next-generation robots, manufacturers everywhere should start preparing,” added Sirkin. “They need to understand how costs and automation technologies are changing in their industries and what their competitors are up to. They also need to start training their workforces for new skills. The coming robotics revolution could significantly reshape the global manufacturing landscape.”
Looking for a reprint of this article?
From high-res PDFs to custom plaques, order your copy today!