Optimizing CIP Further Drives Efficiencies and Sustainability
Reporting and analytics software seamlessly integrated provides many benefits.
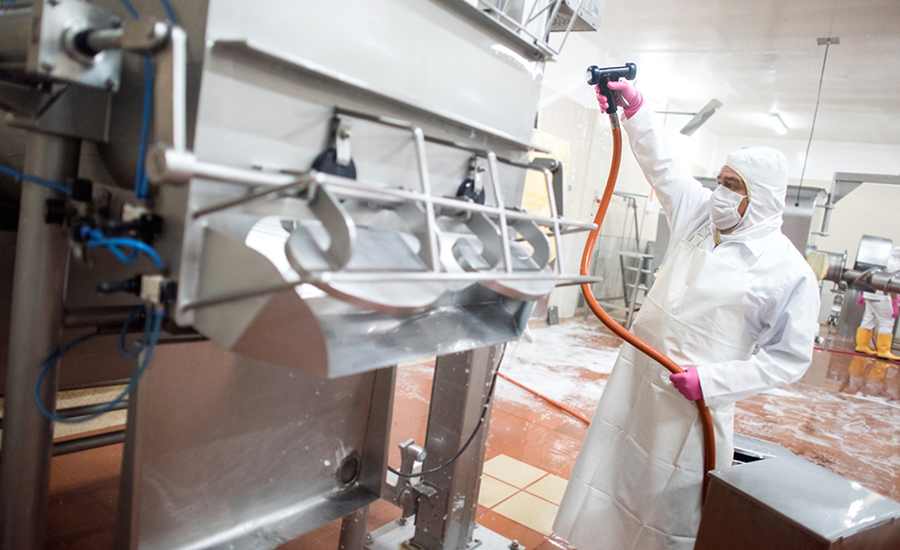
Image courtesy of Getty Images / Andresr
In the U.S., despite unemployment being at historically low levels, around 750,000 jobs are vacant in the overall manufacturing sector according to Bureau of Labor Statistics’ reports. The extreme shortage is reflected in a study by Deloitte and The Manufacturing Institute who predict that a staggering 2.1 million manufacturing jobs will remain unfilled in the U.S. by 2030.1
Additionally, according to the U.S. Chamber of Commerce, as of November 2023, U.S. employers posted 100 job openings for every 72 available workers and fell to less than 50 available workers for every 100 open jobs in at least sixteen states.2
To address this issue, improve food safety and remain competitive, food manufacturers are automating more of the work processes. This automation also facilitates smoother production flow because of mitigating disruptions caused by factors such as employee absenteeism. While clean-in-place (CIP) systems have been used in the food and beverage industry for 50 years, optimizing the process through the integration of reporting and data-analysis software to improve overall performance is fairly new.
Since CIP operations use nearly 30% of a plant’s utilities, incorporating reporting and data analysis into the CIP system can reduce cycle cost, energy use and water use by over 40%, and cycle times by more than 10%.
Clean-In-Place Benefits
A CIP system allow manufacturers to clean internal piping, tanks and machines from one batch to the next to meet government regulations and ensure product quality and safety. With these systems, cleaning can be completed in a fraction of the time, without needing to disassemble the equipment, minimizing production downtime, which can cost a processing plant a staggering $30,000 - $50,000 per hour.3
Individual processing units can be isolated and cleaned independently without impact to production in other areas, allowing for continuous 24-hour production.
Many plants take a manual approach to checking and reporting, which can incur $20,000 to $40,000 in labor costs and invite the margin of error that accompanies pencil-and-clipboard recording. Since CIP operations use nearly 30% of a plant’s utilities, incorporating reporting and data analysis into the CIP system can reduce cycle cost, energy use and water use by more than 40%, and cycle times by more than 10%. Additionally, this lessens solutions required for cleaning equipment and decreases the environmental impact of food production, which accounts for more than 26% of global greenhouse gas emissions.4
The result is a more sustainable and efficient food processing industry.
Using CIP systems means that cleaning processes can be programmed, monitored and controlled remotely, reducing the need for human intervention. This has improved consistency and lessened the risk of human error.

Data Analysis Drives Efficiencies
Monitoring and alarms can improve system efficiency, but they don’t automate the labor-intensive reporting process or provide much-need analytics that extract raw or summary values over a discrete time period such as a CIP cycle. Automated reporting software tracks the program setpoints, as well as the start, stop and step change times to precisely represent each cycle and highlight any deviations in the execution or results. The finished reports are then distributed directly to preferred destinations, which streamlines the decision-making process and enhances operational efficiency. The ability to harness this data effectively can lead to smarter decision making, improved processes and a competitive edge. Analyzing historical data allows operations management to identify patterns, trends and anomalies that may otherwise go unnoticed. Historical data analytics can help plants transition from reactive to proactive planning and keep planning aligned with operations.
With access to real-time process information via analytics software, manufacturers are equipped to automate and optimize various phases of the cleaning process for increased efficiency and maximum productivity.
Reporting
Reports provide a visualization of this real-time or historized process information and correlate related process variables, compute metrics on that data, and visually graph such data for easier pattern and anomaly detection. These reports are created through third-party software that seamlessly integrates with PLCs, SCADA and historian systems. Advanced reporting solutions can even pull information from remote alarm notification software, allowing further analysis and optimization of condition response times.
Reporting software enables organizations to turn raw process data into actionable information, thereby increasing efficiency and reducing costs. Furthermore, automated reporting solutions streamline regulatory compliance by consolidating data from disparate sources like instrumentation readings, program or recipe setpoints, HMI audit trails, alarm history and others. As the data is collected it is summarized as key metrics such as the deltas in the cleaning solution temperature or conductivity. The final output is published into a formatted document representing a detailed performance audit of the process execution.

Continuous Improvement
The fourth industrial revolution, rapid globalization, technological advancements, changing consumer preferences and evolving government policies are reshaping the food and beverage industry. Trying to meet these challenges with manually intensive processes and outdated technology is difficult. However, by leveraging advanced technology such as reporting and analytics software incorporated into CIP systems, operations can increase productivity and efficiency, reduce costs and lessen their carbon footprint.
Sources:
1 https://qupaq.com/news/food-manufacturing-labor-shortages-a-global-challenge/ (accessed March 13, 2024).
2 https://www.manufacturingdive.com/news/food-manufacturing-outlook-trends-to-watch-2024-labor-pricing-inflation/703684/ (accessed March 13, 2024).
3 https://blog.decon7.com/blog/reducing-food-processing-line-downtime-with-better-plant-sanitation (accessed March 13, 2024).
4 https://ourworldindata.org/environmental-impacts-of-food (accessed March 14, 2024).
Looking for a reprint of this article?
From high-res PDFs to custom plaques, order your copy today!