Tyson Food’s revenue was down by a million dollars in 2023, but automation investments keep increasing for the supermajor. In 2022, the company announced plans “to invest more than $1.3 billion in capital in new automation capabilities over the next three years to increase yields, reduce labor costs and associated risks, and ultimately deliver cumulative savings.”
Despite the election year, food manufacturers continued investing in technology and smart manufacturing tools at the operations technology (OT) level. Companies are desperately searching for workforce solutions and need more throughput. FOOD ENGINEERING’s The State of Food Manufacturing in 2024 report shows that 50% of respondents said their budgets for production equipment, packaging and software solutions have increased.
Decision makers have recognized that automation and data-driven tools are needed for generative AI. "We have an (upcoming) meeting, and our board is dead set that we need AI, and I'm behind," says Michael Warter, SVP and CIO for Ruiz Foods Products at the 2024 IFT FIRST show. "They can't define what I'm behind on, so one of the first steps is to get people to understand what AI is in its various facets."
The 9th Annual State of Smart Manufacturing report, released in July by Rockwell Automation, reveals the top industry drivers for adopting digital technology and shows workforce issues as a recurring theme. There were 158 CPG managers and executives surveyed for the report:
- Worker and knowledge retention
- Deploying new technology and capturing and understanding data to improve their business
- Onboarding new employees
- Balancing quality and profitable growth
- Attracting employees with desired skill sets
- Capturing, understanding, interpreting and using data to improve their business
“This year’s report underscores the need for CPG manufacturers to prioritize workforce development, as ensuring employees are well-trained and equipped to leverage emerging technologies will be essential in overcoming industry challenges and achieving sustainable growth,” says Steve Deitzer, vice president of global industry CPG for Rockwell Automation.

From the report, decision makers see the best return on investment (ROI) centered around production monitoring systems. According to the report, the top five ROI are production monitoring, generative AI/machine learning, cloud/software as a service, digital thread and energy management. In July’s issue of FOOD ENGINEERING, G&J Pepsi needed accurate data visibility into its production stoppages due to manual data collection for OEE. G&J Pepsi adopted Sage Clarity’s ABLE (Automation Business Engine Logic) technology that allows food and beverage manufacturers to leverage production data from machine and line programmable logic controllers (PLCs). In keeping with current trends, this is a small technology investment but with big implications.
“The real ‘ah-ha’ moment was when we could see the Mean Time Between Failure (MTBF) number and lines stopping every three minutes, and the best line was stopping every 16.5 minutes,” says Jeff Erwin, VP of manufacturing and quality for G&J Pepsi. “With the real-time insights into performance, we’ve been able to increase MTBF to 30, 40, and in some instances 50 minutes MTBF, so we know the true value the data acquisition solution brings.”
The Smart Manufacturing Report for 2024 also revealed that spending in technology investment increased by 27% this year and landed between 21% to 27% of the operating budget for the 158 decision makers.
Goodman Fielder Bucks Automation Trends
Meeting customers where they live is a common refrain in 2024, especially when it comes to investments for automation technology and system software. Midsize and large food manufacturers are making capital investments, but many have adopted “proof-of-technology” projects to tackle overall equipment effectiveness or bolt-on technology for increased asset management.
However, some large food manufacturers are bucking trends and going big. Goodman Fielder is a major food manufacturer operating in Australia, New Zealand and the Asia-Pacific, and it supplies a range of grocery and foodservice products in these regions. Goodman Fielder recently added Inductive Automation’s supervisory control and data acquisition (SCADA) software and Sepasoft’s manufacturing execution system (MES) for three bakeries and five production lines.
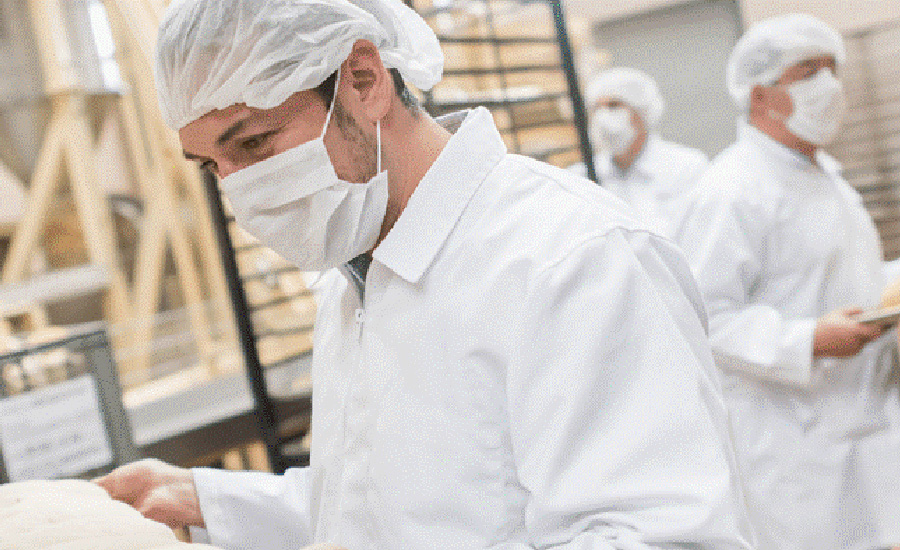
Before implementing these SCADA and MES platforms, Goodman Fielder introduced SAP’s Enterprise Resource Planning platform (ERP). Goodman’s goal with these system software platforms was to increase overall production efficiency and product quality.
For the MES and SCADA platforms, Goodman identified these objectives for the initial rollout across five baking lines and three sites:
- Right-first-time dough mixes
- Reduction in scrap
- Increase in dough mixer availability
Before implementation, production operators on the baking line received printed work order sheets from SAP and then re-entered this data into the mixing equipment, which led to inefficient mixing schedules and quality issues.
“The daily operations team relied on managing production using a combination of basic human machine interfaces (HMIs) as well as printed Excel sheets with no integration into other production or business systems,” states David Hermann, ANZ electrical, instrumentation and process automation manager for Goodman Fielder.
“If a production schedule was changed (in the past), an operator had to run through the line and modify/change the existing paperwork,” adds Richard Anderson, OT consultant for Deloitte.
“By implementing an MES system, we eliminated the manual handling of data and paperwork for our recipe and production schedule,” says Hermann. “A recipe management system was developed to allow the technical teams to manage all mixing recipes from anywhere onsite and from remote locations.”
For the integration, Goodman Fielder and Deloitte rolled out the recipe management pilot to a small audience. Within a short time, there was positive feedback, according to Deloitte at a recent presentation at ICC 2024. The technical baking staff was able to create, edit and delete recipes based directly on bill of materials (BOMs) pulled from SAP. The recipe parameters were written to the PLCs.

Inductive Automation’s MES/SCADA platform, via the MQTT industrial networking protocol, automatically pulls down production schedules—data—from the ERP system. For the integration, the MQTT publish and subscribe engine allowed integrators to discover the operations network in a few seconds, including thousands of PLCs with hundreds or thousands of tags. MQTT’s publish and subscribe technology reduces project integration time since PLC tags for equipment appear instantly. This networking tool eliminates the need to manually provide tag names and input engineering units and ranges. The MQTT protocol was also essential due to Goodman Fielder’s purchase of new baking equipment from UK-based Bakers Perkins.
“The equipment was under warranty, and we couldn't make changes to the PLC code,” adds Gordon Cornish, principal for Deloitte Smart Manufacturing. “In addition, it had its own scheduling system and recipe management. These had to be incorporated into the SCADA and MES integration.”
The SCADA platform uses an autonomous gateway for operations and connects to the business enterprise gateway. “System security always impacts the implementation of these systems,” says Cornish. “Communication paths were required from each (factory) site to the enterprise server. The enterprise server, in turn, required a connection. We worked closely with our IT team to ensure that we had reliable and secure connections between machines.”
A second obstacle for Goodman Fielder with older processes has been recipe management, governing ingredient additions and ratio parameters at the mixing equipment. Local mixing led to “siloing data” and inefficiencies with customized recipes at each mixer across the three plants.
“These (recipes) were originally administered at a local level without a master database. Now the master database contained in the new SCADA platform allows for any changes to be tracked and logged and reported on,” says Cornish. “This means they’re less likely to make mistakes in missing paperwork.”
In parallel with this commissioning, Goodman Fielder introduced new operator visualization and connectivity on the plant floor. Operators can receive reports on basic process parameters, change management, cut weights, a mix of parameters and minor ingredient dosing via handheld devices.

Operators now have agency and can troubleshoot before shift meetings. The new platform allows operators to download data to a client PC, and run real-time reports or produce historical data for comparison of present to previous. In addition, operators have a clearer picture into process parameter audits that allows for quicker analysis of |root cause analysis.
“There are a number of opportunities to connect and display new live data by introducing Internet of Things (IoT) devices and connecting through MQTT, including more data consumers through the limited web clients interfaces,” adds Anderson.
This continuous improvement project is still moving forward, which started in 2022. “We've already expanded on the original system and introduced the system to track baking pans to improve efficiency and the final product quality,” says Hermann. “New edge devices use the MQTT broker and the unified namespace to provide better inventory control.”